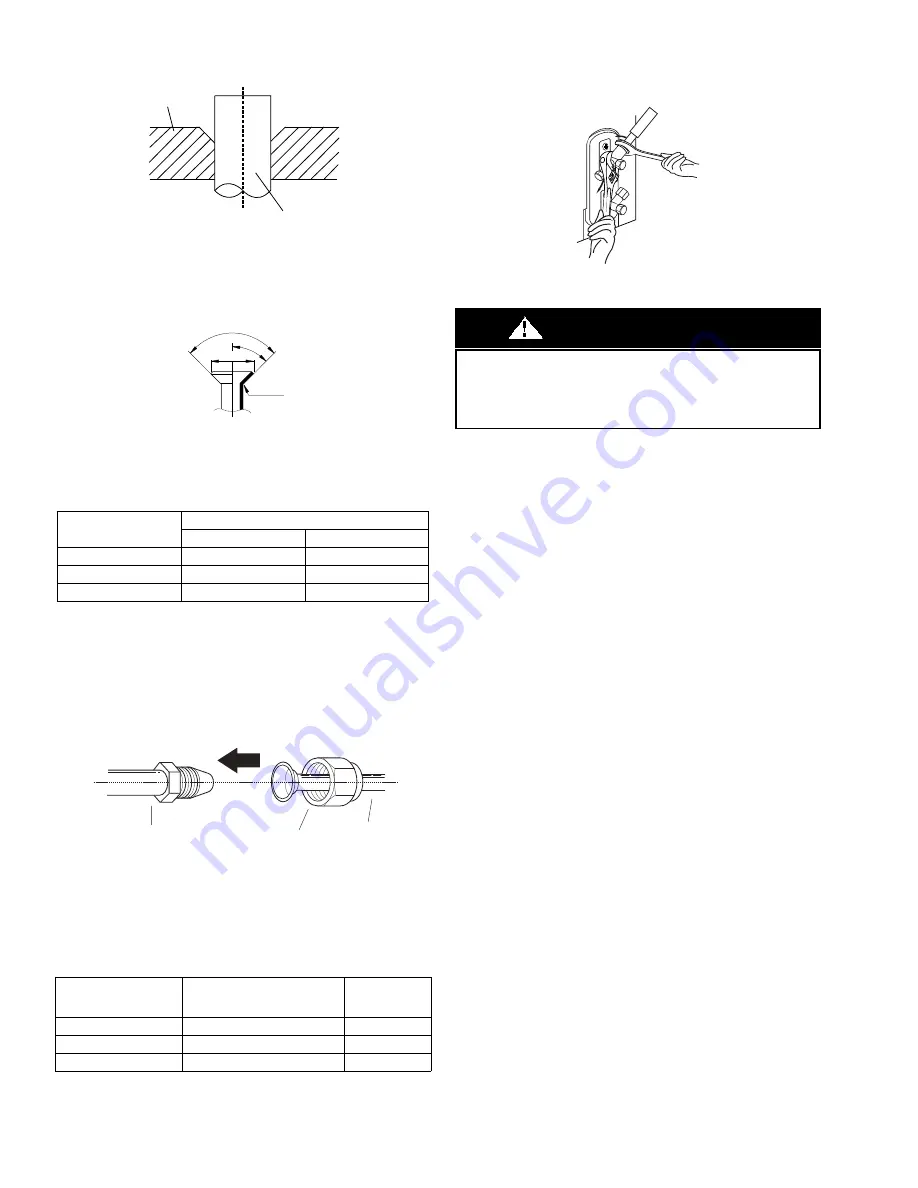
14
Specifications subject to change without notice. 32801002001
e. Clamp the flare block on the end of the pipe. The end of the
pipe must extend beyond the flare form.
Fig. 43 — Flare Block
f.
Place the flaring tool onto the form.
g. Turn the handle of the flaring tool clockwise until the pipe is fully
flared. Flare the pipe in accordance with the dimensions in Table 8
Fig. 44 —Flare Shape
h. Remove the flaring tool and flare block, then inspect the end of
the pipe for cracks and even flaring.
Table 8 — Flare Nut Spacing
6. Connect the Pipes
Connect the copper pipes to the outdoor unit first, then connect
the pipes to the indoor unit. Connect the low-pressure pipe first,
then connect the high pressure pipe.
1. When connecting the flare nuts, apply a thin coat of refrigeration oil
to the flared ends of the pipes.
2. Align the center of the two pipes that you will connect.
Fig. 45 — Align the center of the two pipes
3. Tighten the flare nut as much as possible by hand.
4. Using a wrench, grip the nut on the unit tubing.
5. While firmly gripping the nut, use a torque wrench to tighten the
flare nut according to the torque values listed in Table 9.
Table 9 — Tightening Torque
NOTE: Use both a backup wrench and a torque wrench when
connecting or disconnecting pipes to or from the unit.
Fig. 46 — Torque wrench with backup wrench
All tubing bends should be performed with a properly sized tubing
bender to prevent kinking or damaging the tubing.
6. After connecting the copper pipes to the outdoor unit, wrap the
power cable, signal cable and the piping together with binding tape.
NOTE: While bundling these items together, DO NOT intertwine
or cross the signal cable with any other wiring.
7. Thread this lineset through the wall to connect to the indoor unit.
8. The liquid line sweat connection is 3/8” O.D. copper and the
suction line sweat connection is 5/8” O.D. copper. Use the
appropriate adapters for tubing that runs from the outdoor unit. Cut
and deburr the tubing (review “Remove Burrs” on page 13) to
prepare it for brazing. Setup the nitrogen apparatus and connect to
the outside unit to flow nitrogen while brazing. Braze the tubing
and any fittings to obtain a proper seal.
9. Adjust the nitrogen apparatus to pressurize the system. Pressure test
the system to a maximum of 500 psig for at least 60 minutes.
10. Insulate both lines of the line set separately and completely,
including the outdoor unit valves.
OUTER DIAM. (MM)
A IN (MM)
MAX.
MIN.
Ø 3/8”(9.52)
0.06”(1.6)
0.04”(1.0)
Ø 1/2”(12.7)
0.07”(1.8)
0.04”(1.0)
Ø 5/8”(15.88)
0.09”(2.2)
0.08”(2.0)
BRASS FLARE SIZE
RECOMMENDED SEATING
TORQUE FOR BRASS
FLARE NUTS
N-M
Ø3/8
15-18 Ft. - Lbs
20.3 to 24.4
Ø1/2
28-32 Ft. - Lbs
38.0 to 43.4
Ø5/8
38-42 Ft. - Lbs
51.5 to 56.9
Flare block
Pipe
R0.4~0.8
45
qr
2
90
q
r
4
A
Pipe
Indoor unit tubing
Flare nut
Wrap insulation around the piping. Direct contact with the bare
piping may result in burns or frostbite. Ensure the pipe is properly
connected. Over tightening may damage the bell mouth and under
tightening may lead to leakage.
CAUTION