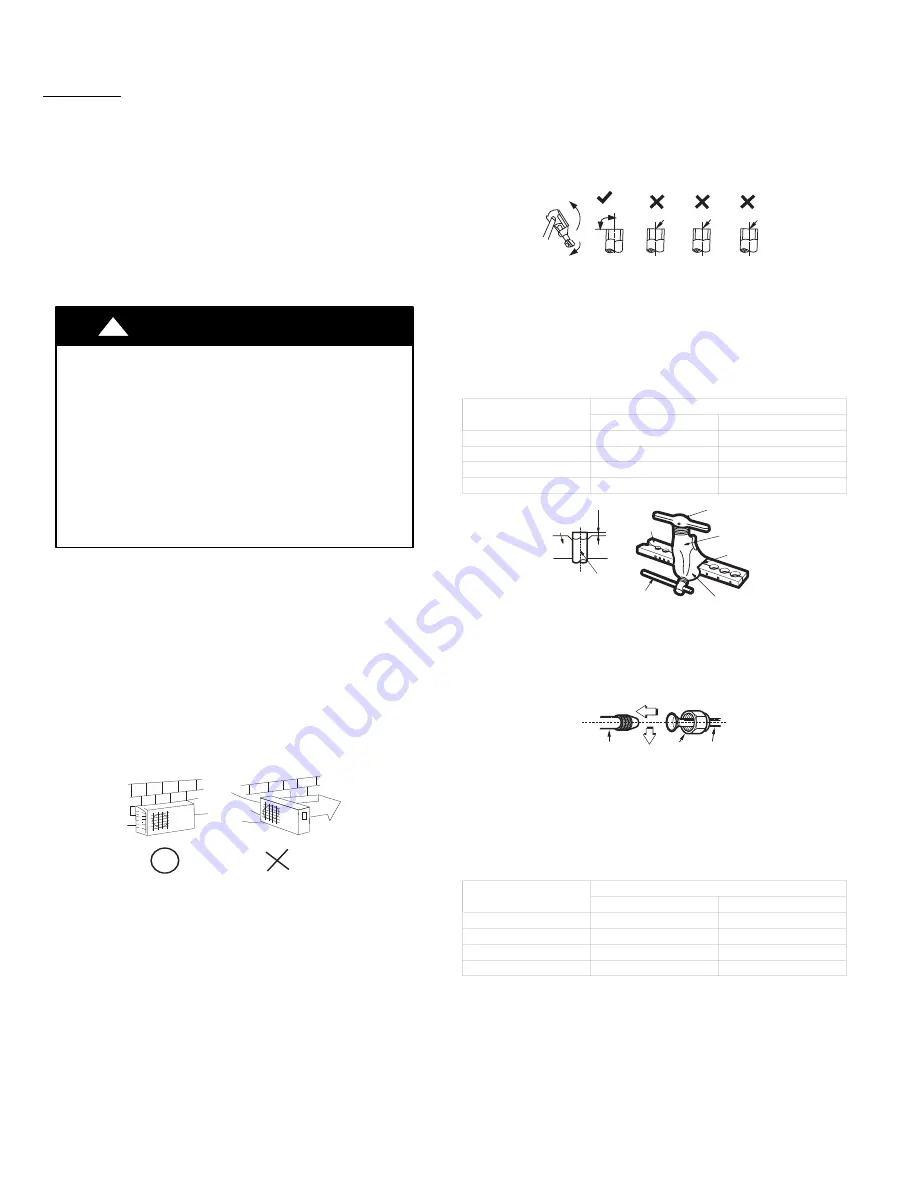
8
32801000801
Specifications subject to change without notice.
INSTALLATION TIPS
Ideal installation locations include:
Outdoor Unit
S
A location which is convenient to installation and not exposed to
strong wind.
S
A location which can bear the weight of outdoor unit and where the
outdoor unit can be mounted in a level position.
S
A location which provides appropriate clearances (see Fig. 3).
S
Do not install the indoor or outdoor units in a location with special
environmental conditions. For those applications, contact your
Ductless Split representative.
OUTDOOR UNIT INSTALLATION
1. Use a rigid base to support unit in a level position.
2. Locate outdoor unit and connect piping and wiring.
CAUTION
!
EQUIPMENT DAMAGE HAZARD
Failure to follow this caution may result in equipment damage
or improper operation.
In regions with snowfall and cold temperatures, avoid
installing the outdoor unit in areas where it can be covered by
snow. If the outdoor unit is installed in areas where heavy
snow is expected, a field supplied ice or snow stand and/or
field supplied−installed wind baffle should be installed to
protect the unit from snow accumulation and/or blocked air
intake. Blocking the air intake may result in reduced airflow,
significantly reduced performance and damage to the
equipment.
NOTE: Install the outdoor unit on a rigid base to reduce noise
levels and vibration. Determine the optimal air outlet direction to
prevent discharged air from being blocked. If the installation site
is exposed to strong winds such as a coastal areas, ensure the fan’s
proper operation by installing the unit lengthwise along the wall
or use dust or shield plates. If the unit needs to be suspended, the
installation bracket should comply with the suspension
requirements in the installation bracket diagram. The installation
wall should be solid brick, concrete or the same intensity
construction, or take steps to reinforce and dampen the support.
The connection between the bracket and the wall as well as the
bracket and the air conditioner should be firm, stable and reliable.
Ensure there is no obstacle which may block the radiating air.
Strong
wind
A07350
Fig. 5
-
High Wind Installation
MAKE REFRIGERANT PIPING CONNECTIONS
(OUTDOOR UNIT)
IMPORTANT:
Use refrigeration grade tubing ONLY. No other type
of tubing may be used. Use of other types of tubing will void
manufacturer’s warranty.
Do not open service valves or remove protective caps from
tubing ends
until all the connections are made.
Bend tubing with bending tools to avoid kinks and flat spots.
Keep the tubing free of dirt, sand, moisture, and other contaminants
to
avoid damaging the refrigerant system.
Avoid sags in the suction line to prevent the formation of oil
traps.
Insulate
each tube with minimum 3/8−in. (10 mm) wall thermal pipe insulation.
Inserting the tubing into the insulation before making
the connections will
save time and improve installation quality.
1. Remove the service valve cover, if provided with the unit.
2. Cut the pipe, with a pipe cutter, at 90 degrees (see Fig. 6).
3. Remove the service connection, if provided with the unit.
Oblique
DŽ
90
Roughness
Burr
A150767
Fig. 6
-
Cut the Pipe
4. Remove all the burrs from the cut cross section of the pipe
avoiding any burrs inside the tubes.
5. Remove the flare nuts attached to the indoor and outdoor units.
6. Install the correct size flare nut onto the tubing and make a flare
connection. Refer to Table 6 for the flare nut spaces.
Table 6—Flare Nut Spacing
OUTER DIAM. (mm)
A (mm)
Max.
Min.
Ø1/4”(6.35)
0.05 (1.3)
0.03(0.7)
Ø3/8”(9.52)
0.06 (1.6)
0.04(1.0)
Ø1/2”(12.7)
0.07 (1.8)
0.04(1.0)
Ø5/8”(15.88)
0.09 (2.2)
0.08(2.0)
Bar
Copper pipe
Clamp handle
Red arrow mark
Cone
Yoke
Handle
Bar
"A"
A150768
Fig. 7
-
Flare Nut Spacing
7. Apply a small amount of refrigerant oil to the flare connection
on the tubing.
8. Align center of the pipes and/or service valve.
Indoor unit tubing
Flare nut
Piping
A150769
Fig. 8
-
Align Pipe Center
9. Connect both the liquid and gas piping to the indoor unit
10. Tighten the flare nut using a torque wrench as specified in the
Table 7.
11. Complete the installation.
Table 7—Tightening Torque
PIPE DIAMETER
INCH (mm)
TIGHTENING TORQUE
Ft-lb
N-m
Ø1/4” (6.35)
10 to 13
13.6 to 17.6
Ø3/8” (9.5
2
)
24 to 31
32.5 to 42.0
Ø1/
2
” (1
2
.7)
37 to 46
50.1 to 62.3
Ø5/8” (15.88)
50 to 60
67.7 to 81.3