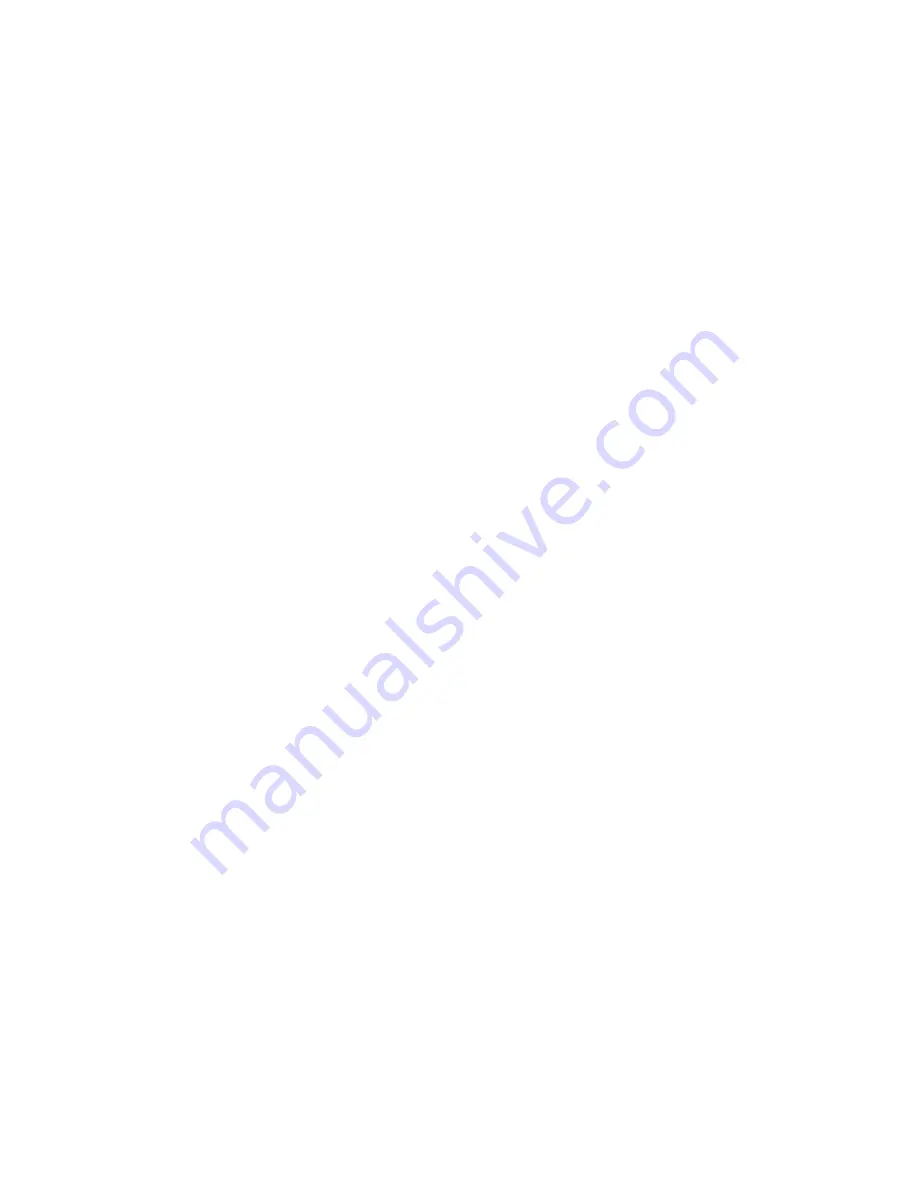
CONSOLE
The only way to field test a console is to con nect it to a
harness on a vehicle with a known working console or
install it on an E-POP (Elec tron ic Point of Purchase) dis play
stand.
HARNESS
The harness can be checked using an ohm me ter or continuity
tester. The main wiring diagram shows the pin out of all
connectors.
ELECTRICAL INTERFERENCE
Erratic operation of the system may be the result of electrical
interference from ignition wires or inductive loads (electrical
clutch, fan, solenoid, etc.). Always try to route wires as far
away from suspect areas as possible. If problems occur, you
may need to relocate the console and/or wiring harness, or
install a noise suppressor.
POWER
Check power source with the MT-101 tester or a test light.
If there is no pow er, trace cable toward battery look ing for
breaks. Also check any fuses or circuit break ers that supply
pow er to the console.
ACCESSORY POWER
The speed, RPM and run/hold cables all have an ac ces so ry
power wire. Check for 12 volts between B (usu al ly white) and
C (usually black) of these con nec tors. If power is not present,
make sure the ac ces so ry pow er wire is not open or shorted
to ground or to another wire. If this wire has a prob lem, the
con sole may ex hib it erratic behavior or not function at all.
VANSCO RADAR SPEED SENSOR
Carefully check your installation and operating instructions.
The following are tips for troubleshooting;
1. Disconnect the radar adapter cable from the console
harness.
2. Check for 12 VDC between pins B and C of the main
harness connector (yellow tie). If not present, console or
harness may be defective.
3. Using a jumper wire (paper clip bent into a “U”), rapidly
short together positions A and C of the main harness
speed connector (yellow tie) several times. The console
should respond with some speed reading. If not, the
console or harness may be defective.
4. Reconnect the radar adapter cable to the main harness
speed connection (yellow tie).
5. Disconnect the radar from the radar adapter cable.
6. Check for 12 VDC between pins 1 and 3 of the radar
adapter connector. If it is not present but was present in
step 2, the radar adapter cable may be defective.
7. Using a jumper wire (paper clip bent into a “U”), rapidly
short together positions 2 and 3 of the radar connector
(round 4-pin) several times. The console should respond
with some speed reading. If not but had a reading in step
3, the radar adapter cable may be defective.
8. If system passes all above tests, the radar may be
defective.
39
TROUBLESHOOTING THE SENSOR, SPEED, RUN/HOLD
AND PROXIMITY SENSORS
CAUTION: Improper connection or voltage could damage the
sensor.
1. Disconnect the sensor in question from the input
2. C12VDC to pin B
3. Connect pin C to Ground
4. Using a voltmeter set to ohms, connect one lead to pin
A and the other to Ground
5. Holding the tip of either the Speed or Run/Hold sensor
up to the north pole of a magnet (non-perforated side
of a Micro-Trak magnet) the meter should read a very
high resistance, while holding the tip of the sensor up
to the south pole should result in a very low resistance
(around 300 ohms). The proximity or gear tooth sensor
works much the same only instead of using a magnet you
would test with a large bolt or other ferrous metal object.
Holding the sensor tip away from ferrous metal object
will give a very high resistance reading while holding the
sensor tip close to a ferrous metal object will result in a
low resistance reading (around 50 ohms).
Also check for proper distance between the tip of the
sensor to target complies with the following:
Speed Sensor (green sensor) tip to magnet spacing should
not exceed 1/2”
Run/Hold (black sensor) tip to magnet spacing should not
exceed 1/2”
Proximity or gear tooth Sensor tip to ferrous metal object
(gear tooth) should not exceed 1/8”
If the sensor fails the above test, replace sensor, if not test
sensor input to controller.
MOTOR BYPASS VALVE
To test the solenoid coil, measure the resistance across
the two terminals in the connector, a good solenoid coil
will measure between 6.8 and 10.8 ohms. If the resistance
is either much lower or higher, replace the solenoid coil.
If the resistance tests ok and the Section Bypass Valve
output tested good, then remove the solenoid coil from the
cartridge stem by removing the 11/16” nut. Slide the coil
off the cartridge stem to expose the 1” hex at the base of
the cartridge. Remove the cartridge and inspect O-rings for
damage. The internal moving part of the cartridge should
move freely up and down, this plunger will be moved up
in the cartridge by the flow of hydraulic oil and when the
solenoid coil is energized, the plunger is forced down closing
the valve thus diverting the oil flow through the motor. If the
plunger will not move, remove the O-rings and submerge the
cartridge in solvent in an attempt to remove foreign material
causing the plunger to bind. If successful, allow cartridge to
dry then replace O-rings and dip cartridge in clean oil prior to
assembly. If unsuccessful, replace cartridge. Screw cartridge
in by hand until the top O-ring is met, then wrench tighten
to 25-27 ft.-lbs. Slide solenoid coil onto cartridge stem and
tighten 11/16” nut to 7-10 ft. -lbs.
Troubleshooting
(cont)
Checking Individual Components
Содержание ProPlant
Страница 1: ...Reference Manual ProPlant TM Automatic Seed Rate Controller...
Страница 41: ...41 Appendices...
Страница 47: ......