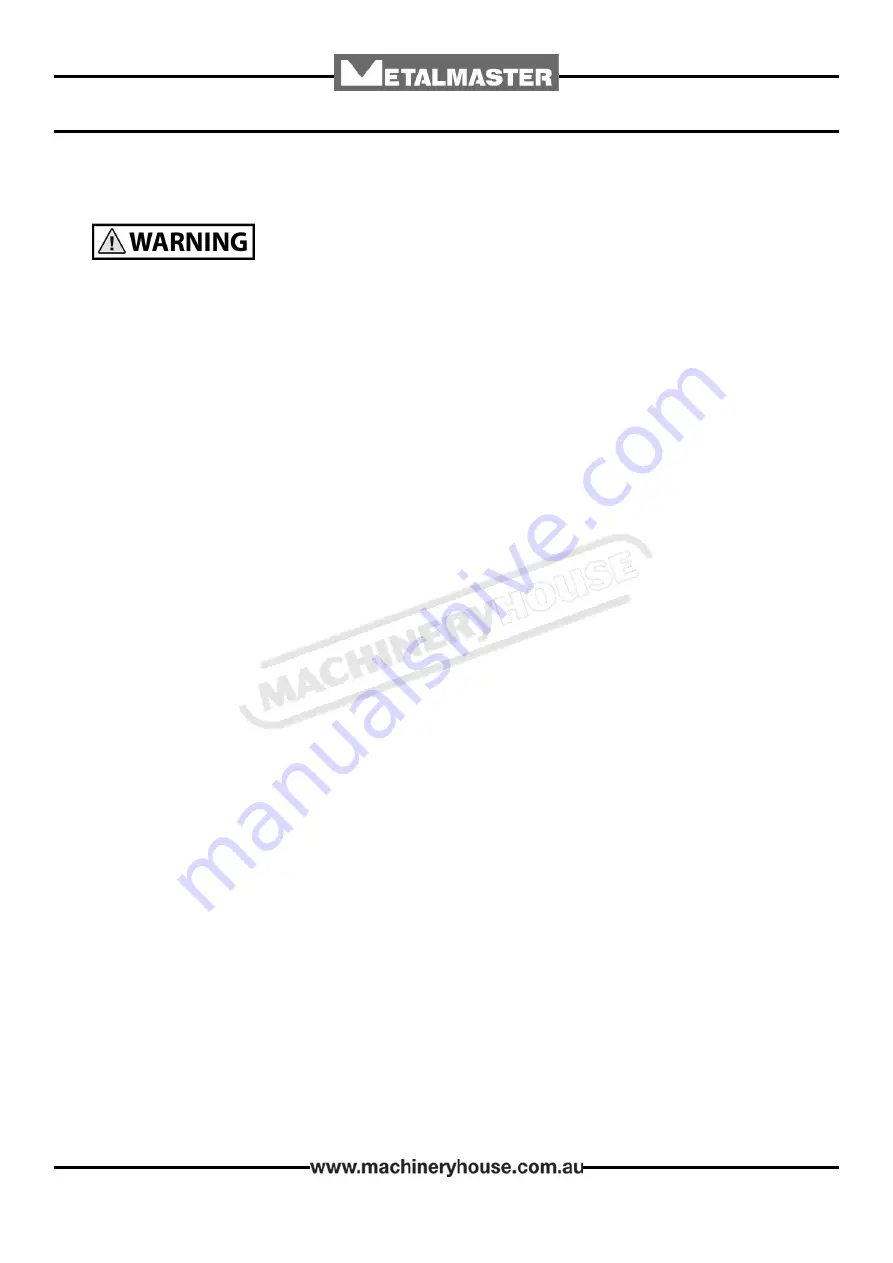
6
OPERATION MANUAL
:
When using any tool, basic safety precautions should always be followed
to reduce the risk of personal injury and damage. Read the instruction manual before using any
tool or machine!
1. Keep work area clean.
Cluttered areas invite injuries.
2. Observe work area conditions.
Do not use machines or power tools in damp or wet
locations. Don’t expose to rain. Keep the work area well lit. Do not use electric power tools
or machinery in the presence of flammable gases or liquids.
3. Keep children away.
Children must never be allowed in the work area. Do not let them
handle machinery, tools, or extension cords.
4. Store idle equipment.
When not in use, tools must be stored in a dry location to inhibit
rust. Always lock up tools and keep out of reach of children.
5. Do not force tool
. It will do the job better and more safely at the rate for which it was
intended. Do not use inappropriate attachments in an attempt to exceed the tool capacity.
6. Use the right tool for the job.
Do not attempt to force any machine, tool or attachment to
do the work of a larger industrial tool. Do not modify, and do not use any tool for a
purpose for which it was not intended.
7. Dress properly
. Do not wear loose clothing or jewelry as they can be caught in moving
parts. Protective, electrically non-conductive clothes and non-skid footwear are
recommended when working. Wear restrictive hair covering to contain long hair.
8. Use eye and ear protection.
Always wear ANSI approved impact safety goggles. Wear
a full face shield if you are producing metal filings or wood chips. Wear an ANSI approved
dust mask or respirator when working around metal, wood, and chemical dusts and mists.
9. Do not overreach.
Keep proper footing and balance at all times. Do not reach over or
across running machines. Keep hands and fingers clear of moving parts.
10. Maintain tools with care
. Keep tools clean for better and safer performance. Follow the
instructions for lubricating and changing accessories. Handles must be kept clean, dry,
and free from oil and grease at all times.
11. Remove adjusting keys and wrenches.
Check that keys and adjusting wrenches are
removed from the tool or machine work surface before plugging it in.
12. Stay alert.
Be attentive and use common sense. Do not operate any machine or tool when
you are tired.
13. Check for damaged parts.
Before using any machine or tool, parts that appears damaged
should be carefully checked to determine that it will operate properly and perform its
intended function safely. Check for alignment and binding of moving parts. Any broken
parts or mounting fixtures, or any other condition that may affect proper operation. Any
part that is damaged should be properly repaired or replaced by a qualified technician. Do
not use the machine or tool if any switch does not turn on and off properly.
2.1 GENERAL METALWORKING MACHINE SAFETY
Содержание EWM-75
Страница 13: ...13 OPERATION MANUAL SPARE PARTS DIAGRAM ...