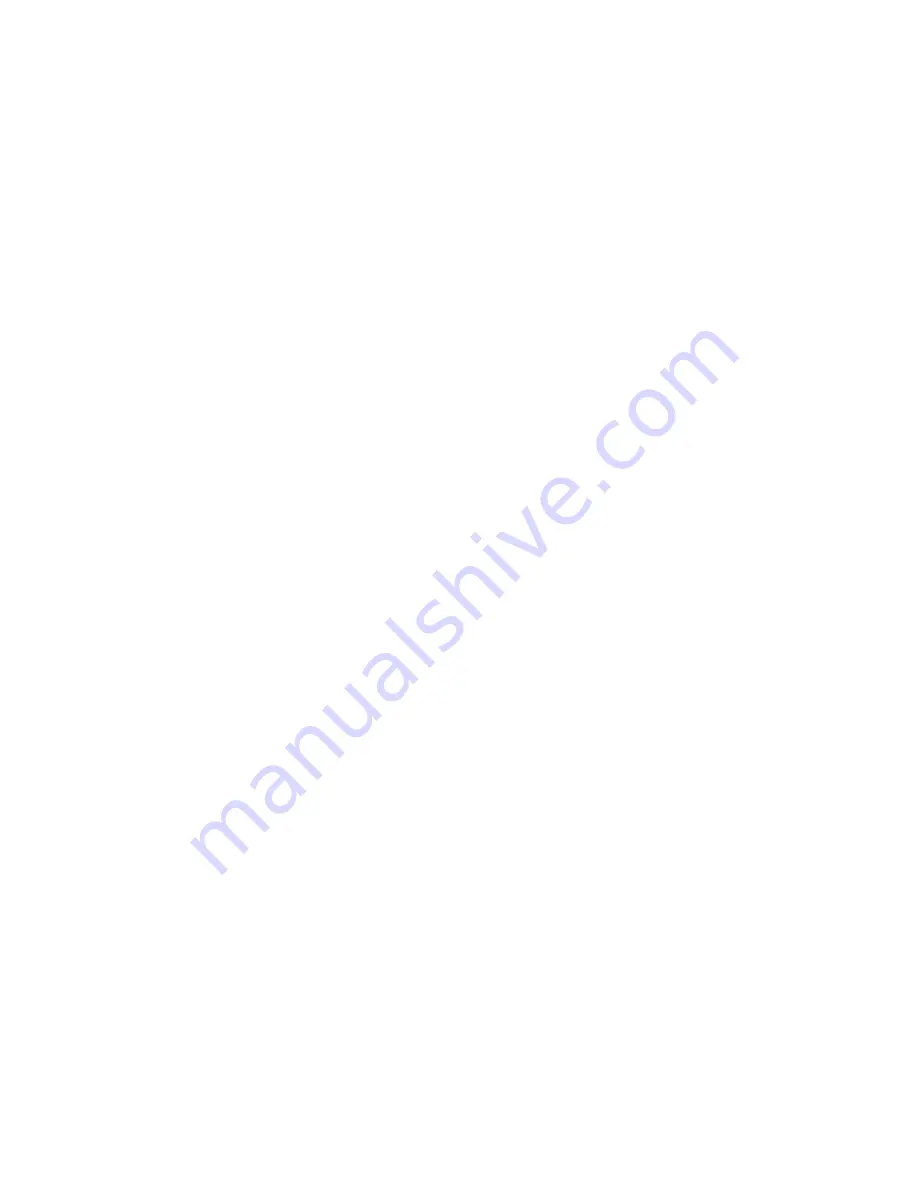
18
5
All piping must be supported independently of the
pump. The piping should always line up naturally
with the pump flanges. Never draw the piping to
the suction or discharge flanges of the pump.
Outside installations should be properly compen-
sated for changes in ambient temperatures. Refer
to pipe manufacturers standards for proper
installation. Omission of this could result in severe
strain transmitted to the pump flanges.
The piping should be as short and direct as possible.
Avoid all unnecessary elbows, bends and fittings,
as they increase friction losses in the piping.
suctioN pipiNg
A) To minimize friction loss, the length of the suction
pipe (from process to pump inlet) should be as
short as possible. It is important that NPSH
available to the pump is greater than the
NPSH required by the pump, long suction runs
greatly affect NPSH and should be considered
carefully. See pump performance curve for
NPSH requirements.
B) The diameter of the suction pipe should be as
large as the pump suction. If long suction runs
are encountered, the suction pipe diameter
should be increased to reduce the NPSH
required.
C) Increasers or reducers, if used, should be
eccentric and installed with the eccentric side
on the bottom of the pipe to prevent air traps.
D) Elbows, fittings, valves or expansion joints
should be avoided at the suction flange. Allow
a straight run of at least 10 pipe diameters into
the suction of the pump.
E) If a valve is to be installed in the suction
piping, only full flow valves offering a minimum
flow disturbance should be used (ball, plug
types). These valves should be for shut-off
only when the pump is not running, and not for
throttling or controlling flow. Centrifugal pumps
should never be throttled on the suction side.
F) Provisions for a suction pressure gauge should
be included.
discharge pipiNg
A) Installation of a valve in the discharge line that
can be used as a block for inspection and
maintenance is recommended. It should be of
a design to allow throttling or flow control.
B) The diameter of the discharge pipe should be
as large or larger than the pump discharge.
C) Provision for a discharge pressure gauge
should be included.
aNcillary pipiNg
A) The diameter of the ancillary or seal piping
should be large enough to meet the seal flush-
ing requirements. Typically this is 1/4-1/2 GPM
at a pressure of 15-25 PSI above the suction
pressure for most mechanical seals. Refer to
pages 25 and 26 for recommended seal flush
flow rates and piping installations.
B) Where the ancillary piping is connected to the
pump only plastic fittings shall be used.
WarNiNg: Failure to use plastic
FittiNgs may result iN damage to
the pump.
C) Many modern flush systems incorporate elec-
trically actuated solenoid valves to conserve
and control the flow of flush liquids, ensure that
the flush liquid is flowing to the seal before the
pump is started.
D) On double seal arrangements with flush in and
flush out connections, flow control valves
should be installed in the flush out or down-
stream side.
The pump shaft should turn freely by hand after
the piping has been connected to the pump. This
is to insure that the piping has not caused binding
in the pump. If binding occurs, check for cause
and correct.
1530 series seal aNd stuFFiNg box arraNgemeNts
EXTERNAL FLUSH: A
n external source of clean fluid is required at the stuffing box
to provide lubrication and cooling. Use plastic fittings only.
Содержание Fybroc series 1530
Страница 15: ...15 1530 series group 1 ...
Страница 16: ...16 1530 series group 2 ...
Страница 19: ...19 Flush pipiNg For siNgle mechaNical seal Flush FloW rate For siNgle seal ...
Страница 20: ...20 Flush pipiNg For double iNside mechaNical seal Flush FloW rate For double seal ...
Страница 21: ...21 Notes ...