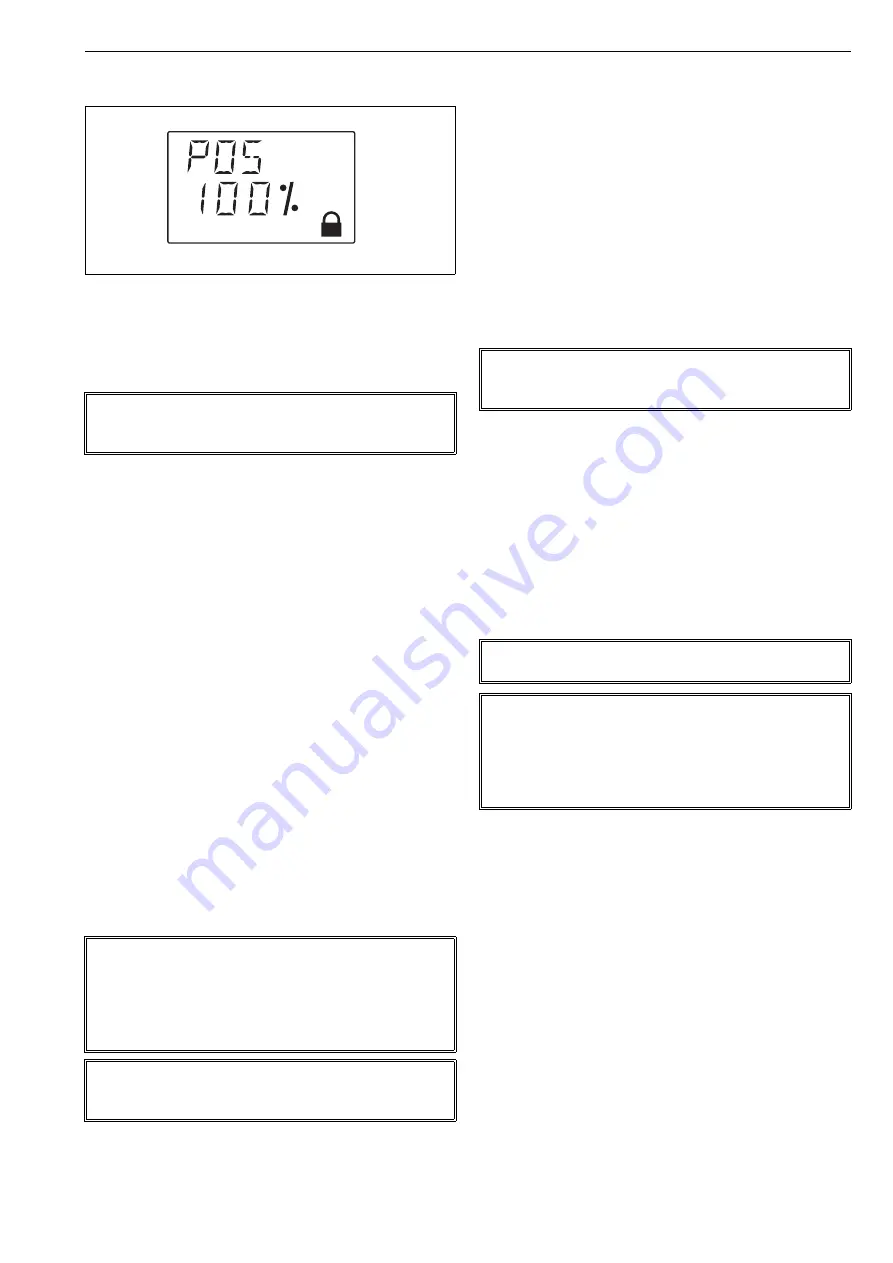
7 VG9H 70 en
21
When the HART write protection is on, the lock symbol will
be activated on the display, see Fig 21.
4.9
HART burst mode
In burst mode, a device can send a HART reply repeatedly
without repeated command. This can be used for sending
e.g. device status information.
4.9.1
Burst mode control
Set burst mode control parameter to On for activating the
burst mode. Default is Off.
4.9.2
Burst mode command
The command number sent in burst mode in HART commu-
nication. Allowed commands are as follows:
3: Read dynamic variables and loop current
9: Read device variables with status
33: Read device variables
169: Read short status
4.9.3
1st, 2nd, 3rd and 4th burst variable
codes
Following device variables can be selected to the burst vari-
ables:
Valve position
Input signal
Safety signal state
Actuator pressure difference
Supply pressure
Housing pressure
Device temperature
5
MAINTENANCE
The maintenance requirements of the ValvGuard depend
on the service conditions, for instance, the quality of instru-
ment air. Under normal service conditions there is no
requirement for regular maintenance.
When maintaining the ValvGuard ensure that the supply air
is shut off and pressure is released. In the following text the
numbers in brackets ( ) correspond to the part numbers in
the exploded view as shown in Chapter 11, unless other-
wise stated.
The ValvGuard VG9000H includes the following modules:
prestage unit (120), spool valve (420), communication cir-
cuit board and controller circuit board with position and
pressure sensors (210).
The spool valve is located on the bottom side of the device
while the other modules are located below the cover (100).
In the event of failure the whole module must be changed.
The module retrofit must be assembled in a clean, dry envi-
ronment. On reassembly apply a thread-locking compound
(for instance, Loctite 243) and tighten the screws firmly.
5.1
Opening and closing of the cover
Open VG9000H cover (100) by opening the M4 screw
(107) first until it is not anymore attached to the
housing (2). Then turn the cover counter-clockwise
until it can be removed.
Close the cover (100) in reverse order. Mount it first
on top of the housing (2) and then turn it clockwise
until threads are tight and the screw (107) is facing
the spring (111) in the housing (2). Tighten the M4
screw (107).
5.2
Prestage
5.2.1
Removal
Loosen the M8 stop screw (110) in the position indi-
cator (109) and turn the position indicator from the
shaft (11). Remove the inner cover (39) attached with
M3 screws (42, 3 pcs.).
Unplug the prestage wire connector from the con-
nector board (182). Unscrew the M4 screws (139, 2
pcs.) and lift up the prestage unit (120). Remove the
O-ring (140).
5.2.2
Adapter plate removal
Remove the screw (412) and remove the adapter
plate. Adapter plate is only needed to be removed
when replaced with new one.
5.2.3
Installation
Install the new adapter plate, if it has been removed.
Make sure the O-rings (411) are properly installed.
Tighten the screw (412).
Place a new O-ring (140) into the groove in the pre-
stage mounting plate (400) and press the prestage
into place. Make sure the nozzle is guided into the O-
Fig. 24
Device write protected
NOTE:
Burst mode can only be set and configured remotely via
HART (DTM).
Ex d NOTE:
Maintenance of the parts of the flameproof enclosure
is not allowed!
Device type VG9_E6_:
Housing (2), Cover (100), Shaft assembly (11), Limit switch
housing (300).
NOTE:
VG9000 maintenance can be done by Metso certified ser-
vice personnel only.
NOTE:
Whenever any maintenance operations have been done
for the VG9000H, the device should be calibrated.
NOTE:
Prestage cannot be changed in the field.
NOTE:
The prestage and adapted plate must be handled care-
fully. In particular the moving parts of the prestage should
not be touched when the inner cover (39) is not in place.
Make sure the prestage and adapter plate are kept clean
during the maintenance.