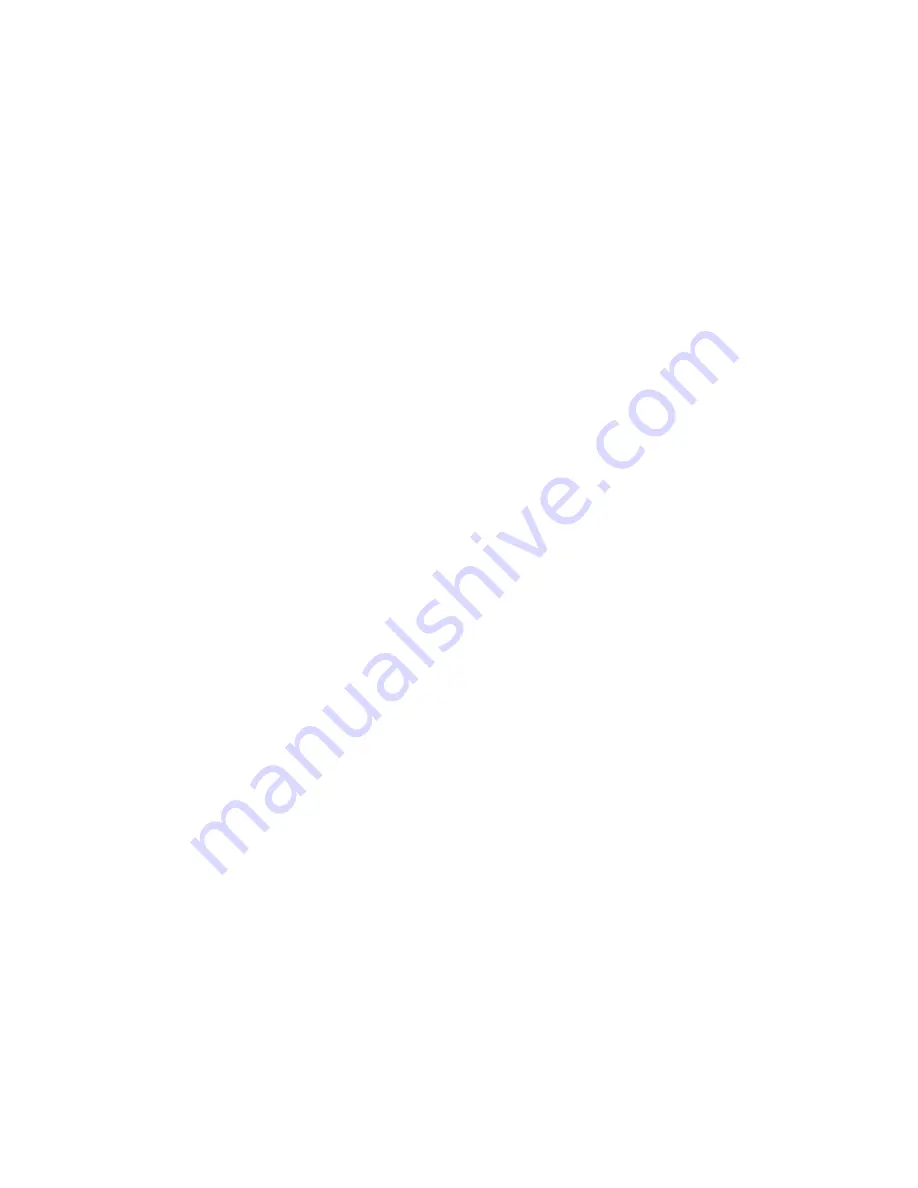
4
1.0 SAFETY PRECAUTIONS
1.1 Danger from Electrical Hazard
Since this feeder is electric motor driven and includes electrical components,
the hazard of electrical shock can exist. Installation and wiring of electrical
components should be in accordance with all applicable codes.
1.2 Operational
Hazards
To avoid possible personal injury, the following guidelines should be
followed:
a)
Do not operate feeder with helix or with lid removed.
b)
Do not operate feeder with electrical component enclosures not in place or
closed.
c)
Any leakage or spillage of feed material should be cleaned up without
delay in accordance with the applicable MSDS safety guidelines and/or
plant instructions.
1.3 Safety
a)
Before operating feeder or attempting to service, become familiar with
contents of the Instruction Manual.
b)
Observe all precautions established by plant safety procedures.
c)
Observe all feed material handling instructions provided by any
applicable MSDS guidelines.
d)
Do not over paint or remove nameplates, labels or tabs.
e)
If motor replacement is required, be certain that speed is the same as
original motor.
f)
If feeder is to be used for other than original service, first ascertain that it
is suitable for new conditions and material compatibility.
g)
Establishment of and adherence to a regular preventive maintenance
program can prevent problems by early detection of unusual conditions.
Such a program should include checking for unusual noise, overheating
and leakage.
Содержание 100 VOLUMERIK Series
Страница 2: ...2 ...