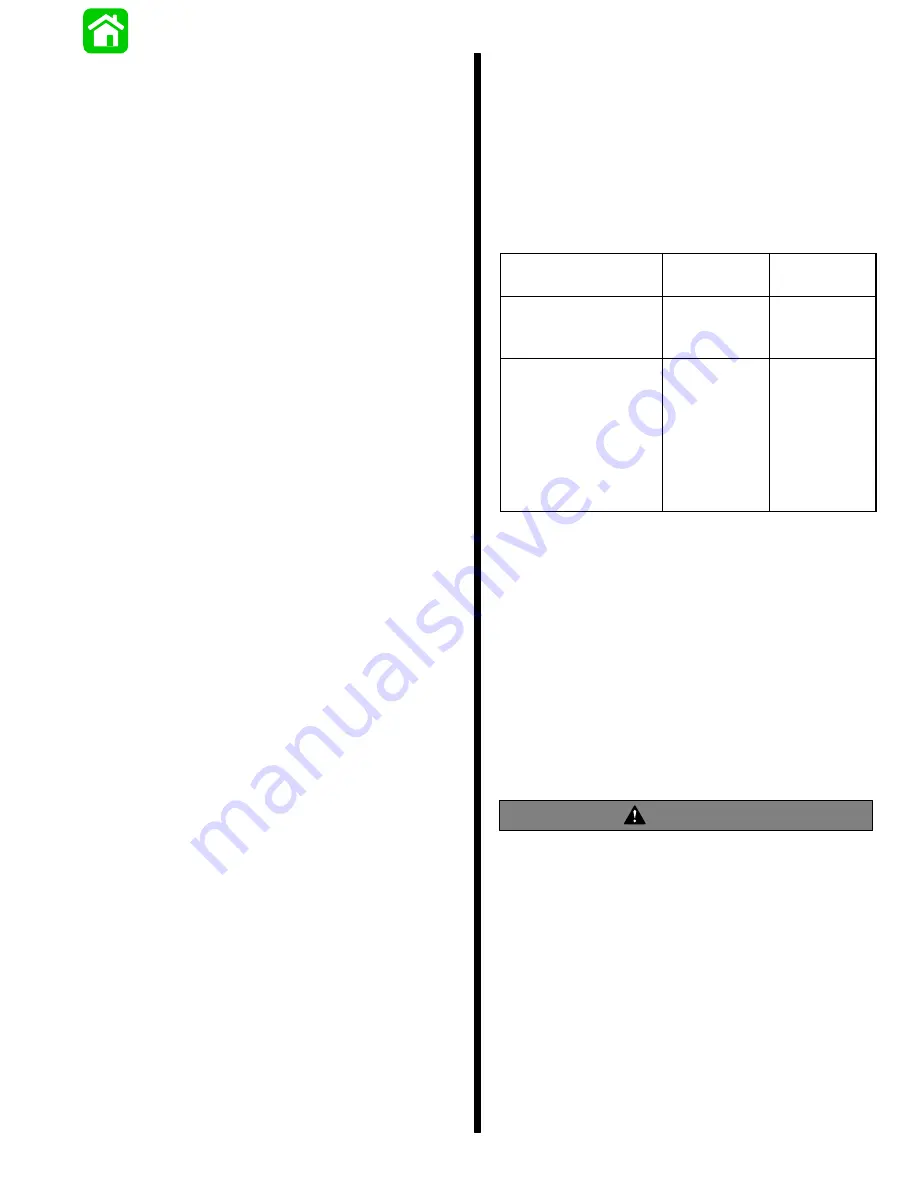
ELECTRICAL - 2B-5
90-852396 MAY 1996
Battery Charging System
Troubleshooting
General Troubleshooting
A fault in the battery charging system will usually
cause the battery to become UNDERCHARGED. A
defective VOLTAGE REGULATOR may also allow
the system to OVERCHARGE the battery.
If a problem exists in the charging system, visually
check the following:
1. Check for correct battery polarity [RED cable to
(+) POSITIVE battery terminal].
2. Check for loose or corroded battery terminals.
3. Check condition of the battery.
4. Visually inspect all wiring between stator and bat-
tery for cuts, chafing and disconnected, loose or
corroded connections.
5. Excessive electrical load (from too many acces-
sories) will cause battery to run down, even if the
system is operating correctly.
If the system is still OVERCHARGING the battery,
the VOLTAGE REGULATOR is most likely defective
and should be replaced.
If the battery is UNDERCHARGED, proceed with
REGULATOR, STATOR, and RECTIFIER tests, fol-
lowing.
Alternator System
STATOR TEST (ALTERNATOR COILS ONLY)
NOTE: Stator can be tested without removing from
engine.
1. Disconnect 2 YELLOW stator leads from bullet
connectors to voltage regulator/rectifier.
2. Use an ohmmeter and perform the following test:
Test Leads To-
Resistance
(Ohms)
Scale
Reading
Connect test leads
between 2 YELLOW
stator leads
.25-.45*
R x 1
RED test lead to 1
YELLOW stator
lead, and BLACK
test lead to engine
ground if stator is
mounted or to steel
frame of stator (if off
engine)
No
Continuity
R x 1000
* Resistance of these windings generally is less than
one ohm. A reading, that resembles a short, is ac-
ceptable. Copper wire is an excellent conductor but
will have noticeable differences from cold to hot.
Reasonable variation from specified reading is ac-
ceptable.
3. If meter readings are other than specified, re-
place stator assembly Refer to stator assembly
replacement in Section 2A.
TROUBLESHOOTING ALTERNATOR
SYSTEM
WARNING
Before connecting or disconnecting any electri-
cal connection, battery cables MUST BE RE-
MOVED from battery to prevent possible person-
al injury or damage to equipment.
IMPORTANT: The charging system may be con-
nected to one or more batteries during these
tests. However, these batteries MUST BE fully
charged. These batteries MUST NOT BE con-
nected to any other charging source.