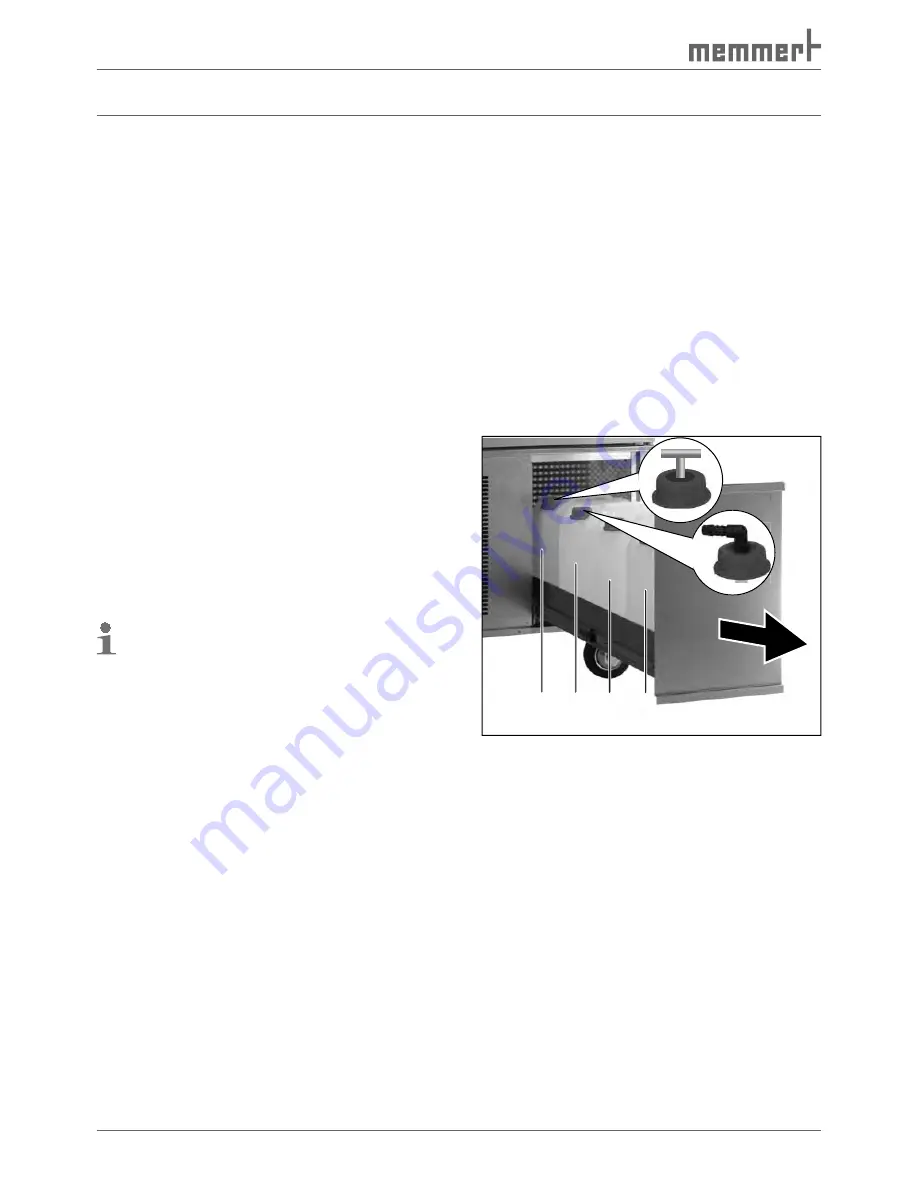
24
Operation and control
5.
Operation and control
5.1
Operating staff
The test chamber may only be operated by persons who are of legal age, and who have re-
ceived instructions for the test chamber. Personnel who are to be instructed or who are under-
going general training may only work with the test chamber under the continuous supervision
of an experienced person.
5.2 General information on operation
The condensation pressure of the cooling unit is controlled by the automatic speed adjust-
ment of the condenser fan. The fan can therefore automatically run faster or slower in opera-
tion, depending on the thermal energy extracted. The speed of the interior fan can also vary:
At low temperatures the fan speed is automatically reduced. In strong heating operation it is
automatically increased.
5.3
Before starting
1. Empty the condensation water tank. To do
so, pull out the tank drawer from the test
chamber (for CTC climatic test chambers,
see Fig. 16) or open the flap (for TTC
temperature test chambers).
2. Screw open the lids of the condensation
water tanks A1 and A2, remove tanks,
empty and then re-insert them and screw
the lids back on.
Caution:
Do not mix up the lids, otherwise conden-
sation water may leak. Screw on the lid
with the T-connector onto the tank at the
rear (A1) (Fig. 16), so that condensation
water can flow into tank A2 when tank
A1 is full.
3. For the climatic test chambers CTC, fill
the two fresh water tanks (B1 and B2) as
described on page 22.
4. Check whether the silicone plugs have
been inserted into the feed-through on
the right side of the appliance and if the
seal is tight (see Fig. 18 on page 26 ).
A1 A2 B1 B2
Fig. 16
Tank drawer (shown in figure:
CTC climatic test chamber, the TTC tem-
perature test chamber has just one con-
densation water tank behind a flap, and no
freshwater tank)
A1, A2 2 condensation water tanks, 10 l
each
B1, B2 2 freshwater tanks, 10 l each