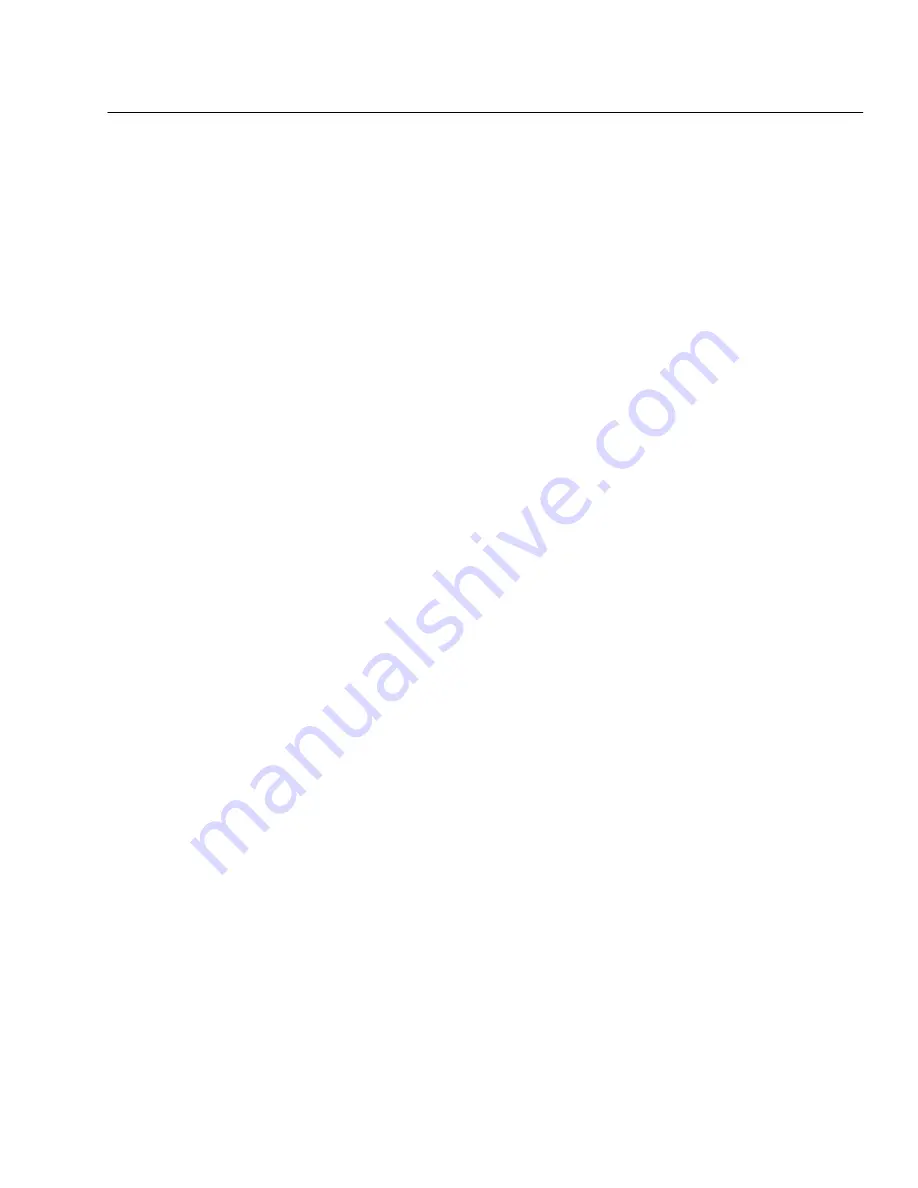
CSP-HE/HS-1
General
ROTORCRAFT FLIGHT MANUAL
MD 500
(Models 369HE/HS/HM
)
Revision 6
1-1 1
belts are provided for all positions. In the military version, the center seat is
eliminated.
An instrument panel is located forward of the seat at the aircraft centerline.
The panel incorporates standard flight and engine instruments in addition to
warning and caution lights. The panel also contains adequate space provisions
for various arrangements of communication and navigation equipment.
The lower fuselage structure beneath the pilot/passenger floor contains com−
partment space for the aircraft battery and provision for small cargo storage or
installation of avionics equipment. Access to the compartments is through two
floor door plates.
The cargo compartment in the center of the aircraft contains provisions for in−
stallation of a bench or individual folding type passenger seats, which are ad−
justable in height.
Seat belts are provided with several styles being offered. The seats and belts
are easily removed. Cargo compartment bench−type seats may be easily folded
out of the way or completely removed for accommodating cargo.
During cargo carrying operations, the compartment floor serves as the cargo
deck. Removable and interchangeable cargo tiedown fittings are available.
The aft section includes the structure for the tailboom attachment and engine
compartment. Access to the engine compartment is provided through clamshell
doors contoured to the shape the fuselage.
The lower section is divided by the center beam and provides a housing for the
two fuel cells. Provisions for the attachment of a cargo hook are located on the
bottom of the fuselage in line with the center beam.
Four doors are installed on the helicopter−two on each side. The two forward
doors permit access to the forward compartment for pilot and passengers. The
two aft doors allow entry to the passenger/cargo compartment. Transparent
tinted windows are contained in the doors.
The power plants used are either the Allison Model 250−C18 gas turbine en−
gine with a takeoff power rating of 317 shp or the Allison 250−C20 with a
take−off power rating of 400 shp. Only 278 shp at 104 percent N
2
RPM is used
for takeoff; 243 maximum continuous shp provides sufficient power for all oth−
er flight modes.
Limiting the maximum power to less than the maximum rated power provides
a higher engine critical altitude. The power turbine governor provides automat−
ic constant speed control of rotor RPM.
The overrunning clutch transmits power from the engine to the main drive
shaft. The clutch has no external controls and disengages automatically during
autorotation and engine shutdown. The main drive shaft connects to the main
rotor transmission input shaft. The engine oil cooler blower is belt driven off
the main drive shaft. The oil cooler blower draws cooling air from the air inlet
fairing to supply ambient air to the engine oil cooler and to the engine com−
partment.