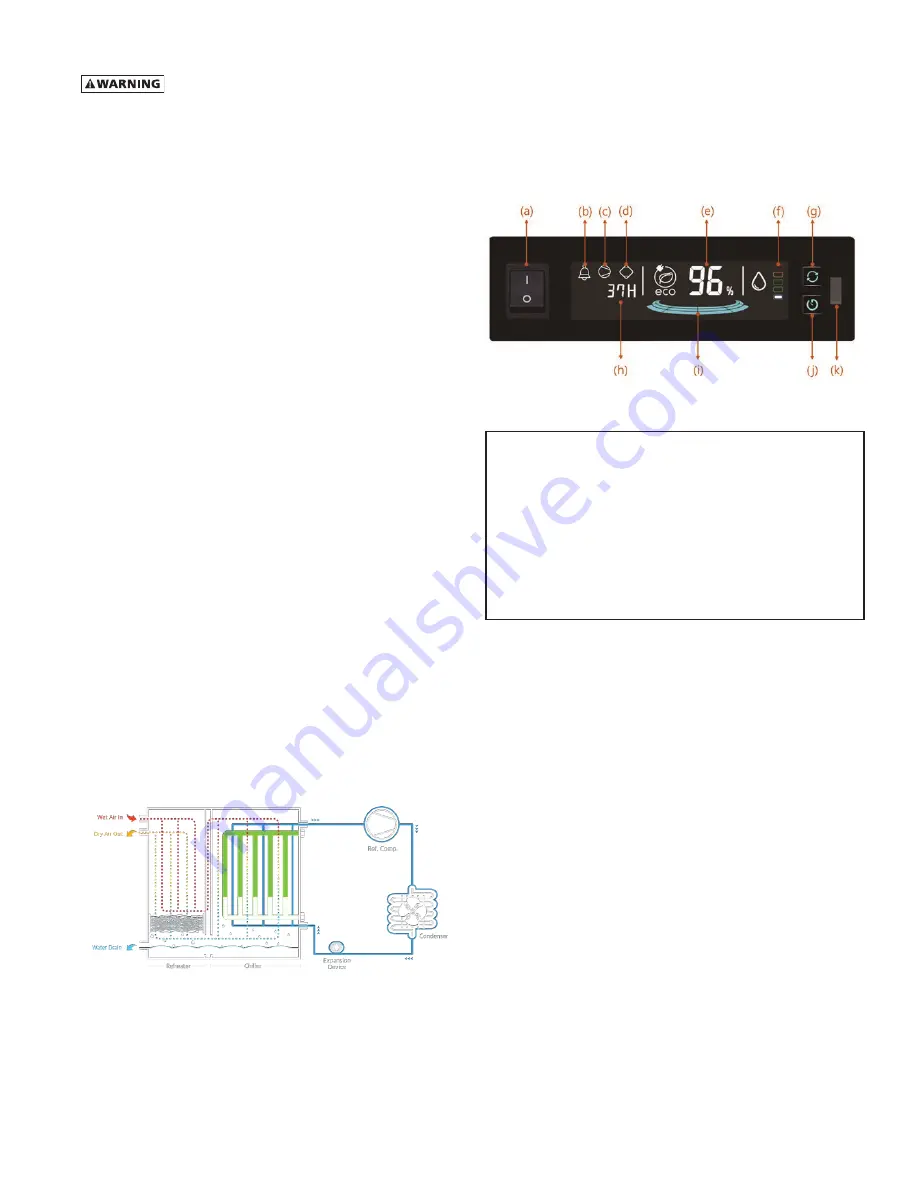
3
Electrical Connections
Operation of dryers with improper line voltage constitutes
abuse and could affect the dryer warranty.
The dryers are constructed according to NEMA Type 1 electrical
standards. Field wiring must comply with local and national fire,
safety and electrical codes. Installation must be in accordance
with the National Electrical Code. Confirm that your line voltage
is the same as the voltage listed on the dryer data plate. Refer
to Figure 5 electrical schematics.
HOW IT WORKS
Phase Change Mechanism of the FLEX Dryer
1. When the refrigeration compressor and the condenser fan
are running, the cold refrigerant in the chiller (evaporator)
cools the liquid Phase Change Material (PCM) which gradu-
ally solidifies.
2. When the PCM is sufficiently cooled and solidified, the
refrigeration compressor and condenser fan will stop.
3. The compressed air is continuously cooled by the PCM
while the refrigeration compressor is inactive. No power
is consumed during this period.
4. The PCM gradually liquefies as it adsorbs heat from the
compressed air, and when fully melted, the refrigeration
compressor and condenser fan resume to cool the PCM.
Compressed Air flow
The dryers use refrigeration cooling to condense entrained
moisture out of the air stream. Warm saturated air enters the
air-to-air heat exchanger where it is cooled by outgoing cold
air. The inlet air is further cooled in the refrigeration chiller. The
condensate is removed from the air stream by an electronic
drain valve.
The cold, dry air is reheated by incoming warm air as it passes
back through the air-to air heat exchanger. Using the outgo-
ing air to pre-cool the inlet air condenses up to 65 percent of
the moisture out of the inlet air before it reaches the chiller.
Pre-cooling the inlet air reduces the heat load on the refriger-
ant compressor, permitting the use of a smaller refrigerant
compressor.
Figure 2.
Schematic diagram of the compressed air flow and
refrigerant
CONTROLLER
The controller provides ease of monitoring and operating
status for Energy Savings (%), dryer operating time, refrigera-
tor compressor operating time, and active fault message dew
point status. The controller also provides advanced functions
like communication and operating status data storage.
Figure 3.
Controller
a: DRYER ON/OFF SWITCH
b: ALARM LIGHT
c: REFRIGERANT COMPRESSOR RUNNING LIGHT
d: DRYER RUNNING LIGHT
e: ENERGY SAVING RATIO (%)
f: DEWPOINT TEMPERATURE INDICATOR
g: RUNNING TIME SELECT BUTTON
h: DRYER RUNNING / REFRIGERANT COMPRESSOR RUNNING TIME
i: ENERGY SAVING (GRAPH)
j: TIMER BUTTON
(LEVEL 2 ONLY)
k: MICRO-USB CONNECTION PORT
(LEVEL 2 ONLY)
Controller Functions
1. Dryer On/Off
2. Display energy saving ratio (%)
3. Display alarm signal
4. Display dryer and refrigerant compressor running time
5. Display dew point level by indicator
6. Save the operating data
a. Refrigerant compressor on/off status, Alarm, Dew
point level, Inlet air temperature
b. Memory chip can save maximum 30 days
c. When there is no space to save, then erase the first
one
7. MICRO-USB connection port
a. Automatically download operating data
b. Automatically upgrade firmware program
8. Communication port
a. RS485: Modbus monitoring
MCGUIRE AIR COMPRESSORS INC
1-888-229-9999
MCGUIRE AIR COMPRESSORS INC
1-888-229-9999