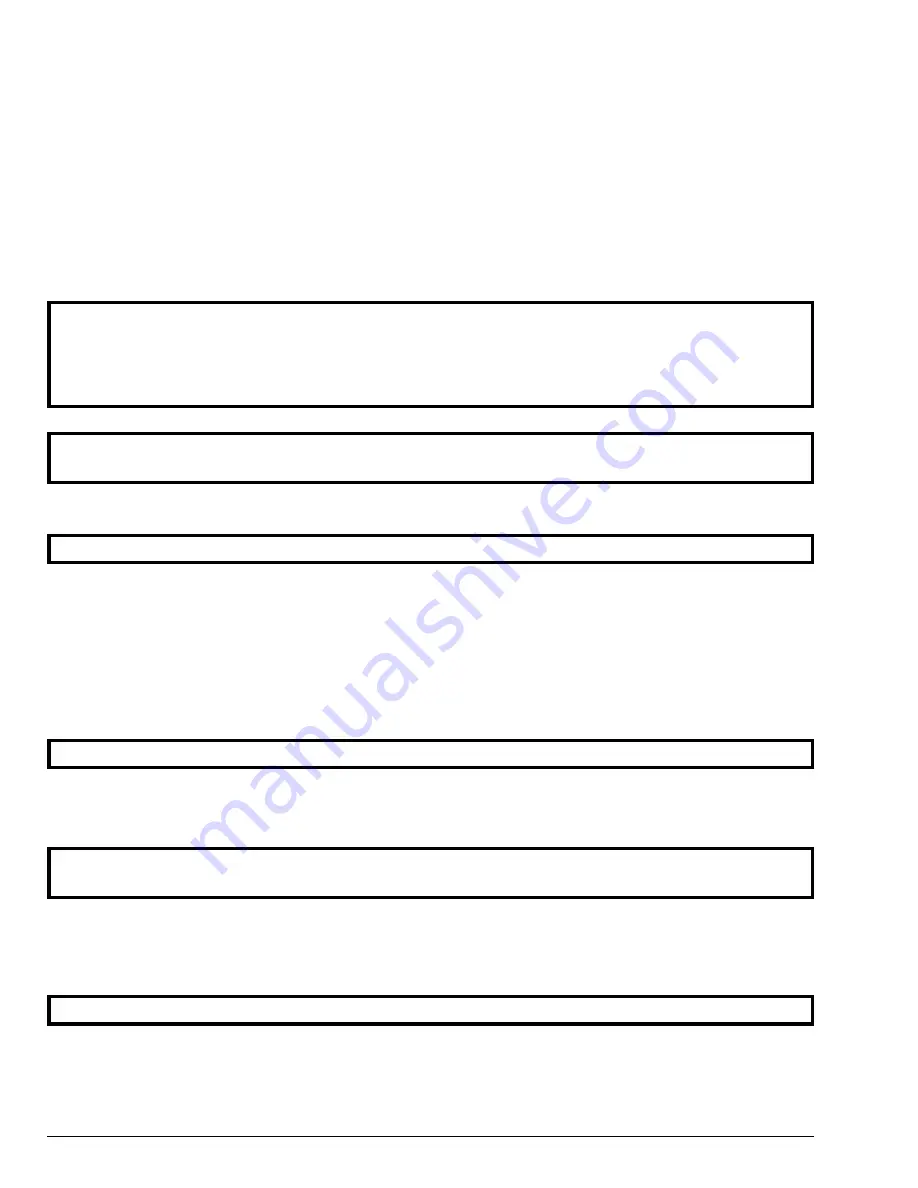
6
Maytag Co.
450365 - 1
SECTION II
ROUTINE MAINTENANCE
A. CLEANING
A program or schedule should be established for periodic inspection, cleaning, and removal of lint from various areas
of the dryer, as well as throughout the ductwork system. The frequency of cleaning can best be determined from
experience at each location. Maximum operating efficiency is dependent upon proper air circulation. The accumulation
of lint can restrict this airflow. If the guidelines in this section are met, a Maytag dryer will provide many years of
efficient, trouble free, and most importantly, safe operation.
WARNING: LINT FROM MOST FABRICS IS HIGHLY COMBUSTIBLE. THE ACCUMULATION OF
LINT CAN CREATE A POTENTIAL FIRE HAZARD.
KEEP DRYER AREA CLEAR AND FREE FROM COMBUSTIBLE MATERIALS,
GASOLINE, AND OTHER FLAMMABLE VAPORS AND LIQUIDS.
NOTE:
Suggested time intervals shown are for average usage which is considered six to eight
operational (running) hours per day.
Clean lint drawer and screen every third or fourth load.
NOTE:
Frequency can best be determined at each location.
DAILY
Beginning of each work shift.
Clean lint from the drawer and screen. Inspect lint screen and replace if torn.
WEEKLY
Clean lint accumulation from lint chamber, thermostat, and microprocessor temperature sensor (sensor bracket)
area.
WARNING:
To avoid the hazard of electrical shock, discontinue electrical supply to the dryer.
STEAM DRYERS
Clean steam coil fins using compressed air and a vacuum cleaner with brush attachment.
NOTE:
When cleaning steam coil fins, be careful not to bend the fins. If the fins are bent,
straighten by using a fin comb, which is available from local air conditioning supply houses.
90 DAYS
Remove lint from tumbler, drive motors, and surrounding areas. Remove lint from gas valve burner area with a
dusting brush or vacuum cleaner attachment.
NOTE:
To prevent damage, avoid cleaning and/or touching the ignitor/globar probe assembly.
Remove lint accumulation from inside control box and at rear area behind control box.