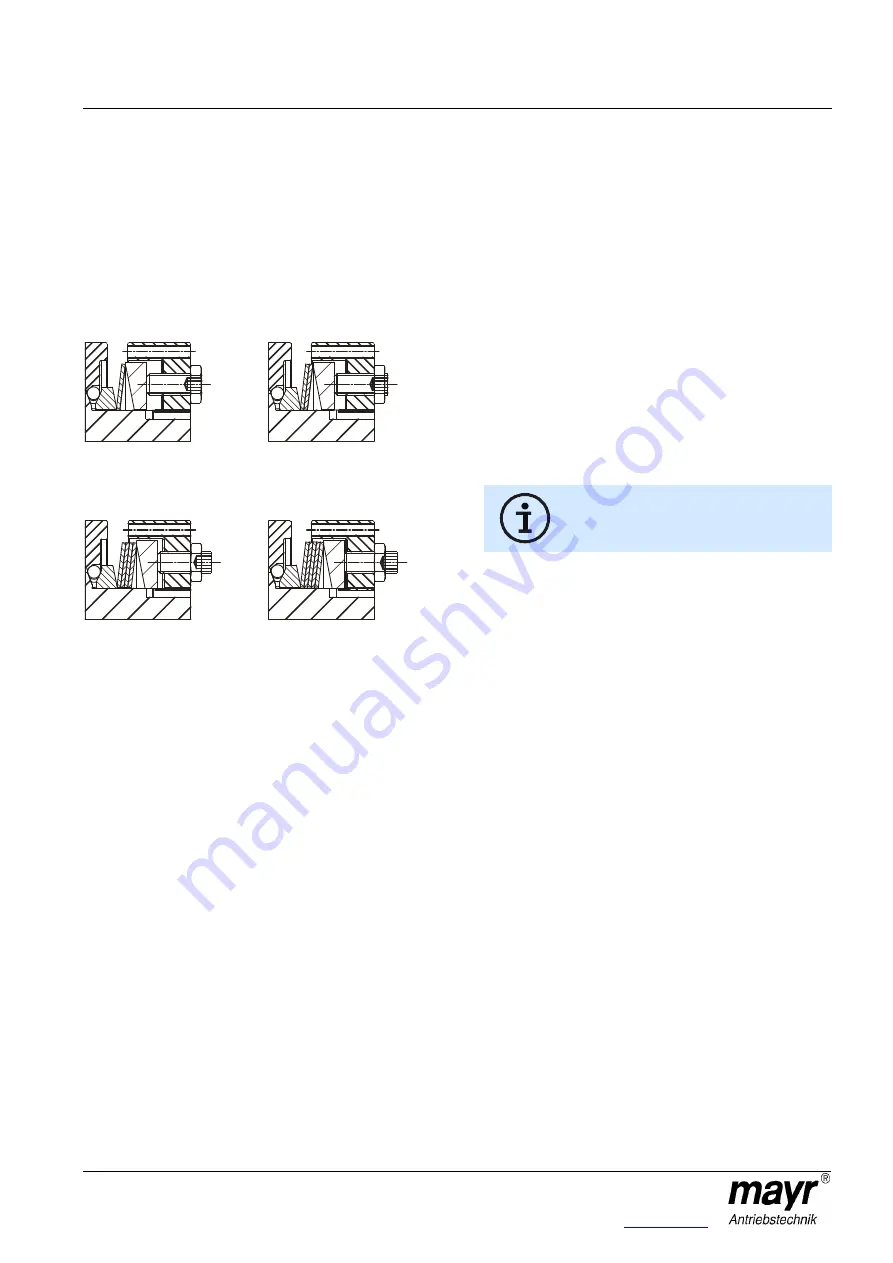
Installation and Operational Instructions for
EAS
®
-Compact
®
overload clutch,
Type 49_._ _4._ Sizes 4 and 5
(B.4.14.6.GB)
25/01/2013 GC/NH/GH/SU
Chr. Mayr GmbH + Co. KG
Tel.: +49 8341 804-0
Eichenstraße 1
Fax: +49 8341 804-421
D-87665 Mauerstetten
www.mayr.com
Page
11
of
21
Germany
E-Mail:
Cup Spring Layering (Fig. 12)
Correct cup spring layering is a prerequisite for problem-free
clutch function and torque adjustment.
For the lower torque range,
one
cup spring
(Type 49_.
5
_ 4._),
for the medium torque range,
two
cup springs
(Type 49_.
6
_ 4._),
for the high torque range,
four
cup springs
(Type 49_.
7
_ 4._)
and for the maximum torque range
five
cup springs (Type 49_.
8
_ 4._) are installed.
1x layered
2x layered
Type 49_.5_4._
Type 49_.6_4._
4x layered
5x layered
Type 49_.7_4._
Type 49_.8_4._
Fig. 12
Mounting onto the Shaft
EAS
®
-Compact
®
clutches include cone bushings or keyways as
part of the standard delivery.
Please observe the following when mounting cone
bushings:
Shaft tolerances from h8 to k6 are permitted.
Shaft surface: finely turned or ground
(Ra = 0,8 µm)
Shaft material: yield point at least 400 N/mm
2
,
e.g. St 60, St 70, C 45, C 60.
Degrease or remove preservation layers on the shafts and
bores before installing the clutch.
Greasy or oily bores or shafts do not transmit the
torques defined in the catalogue.
Mount the clutch or clutch hubs onto both shaft ends using a
suitable device and bring it / them into the correct position.
Tighten the tensioning screws (Item 14) in 2 steps cross-
wise and then in 3 to max. 6 tightening sequences evenly
using a torque wrench to the torque stated in Table 2.
The transmittable torques of the shaft-hub connection are
dependent on the bore diameter and the quality of the drive
shafts used. Please observe the respective transmission
tables in the valid and applicable product catalogue.
The clutch or the clutch hub carries out an axial
movement in the direction of the cone bushing
(13) when tightening the cone bushing (13).
De-installation
In the cone bushing (13), tapped extracting holes are located
next to the tensioning screws (14).
1) Loosen all tensioning screws (14).
2) Screw out the tensioning screws (14) located next to the
tapped extracting holes and screw them into the tapped
extracting holes up to their limits.
Then tighten these screws until the tensioning connection
loosens.