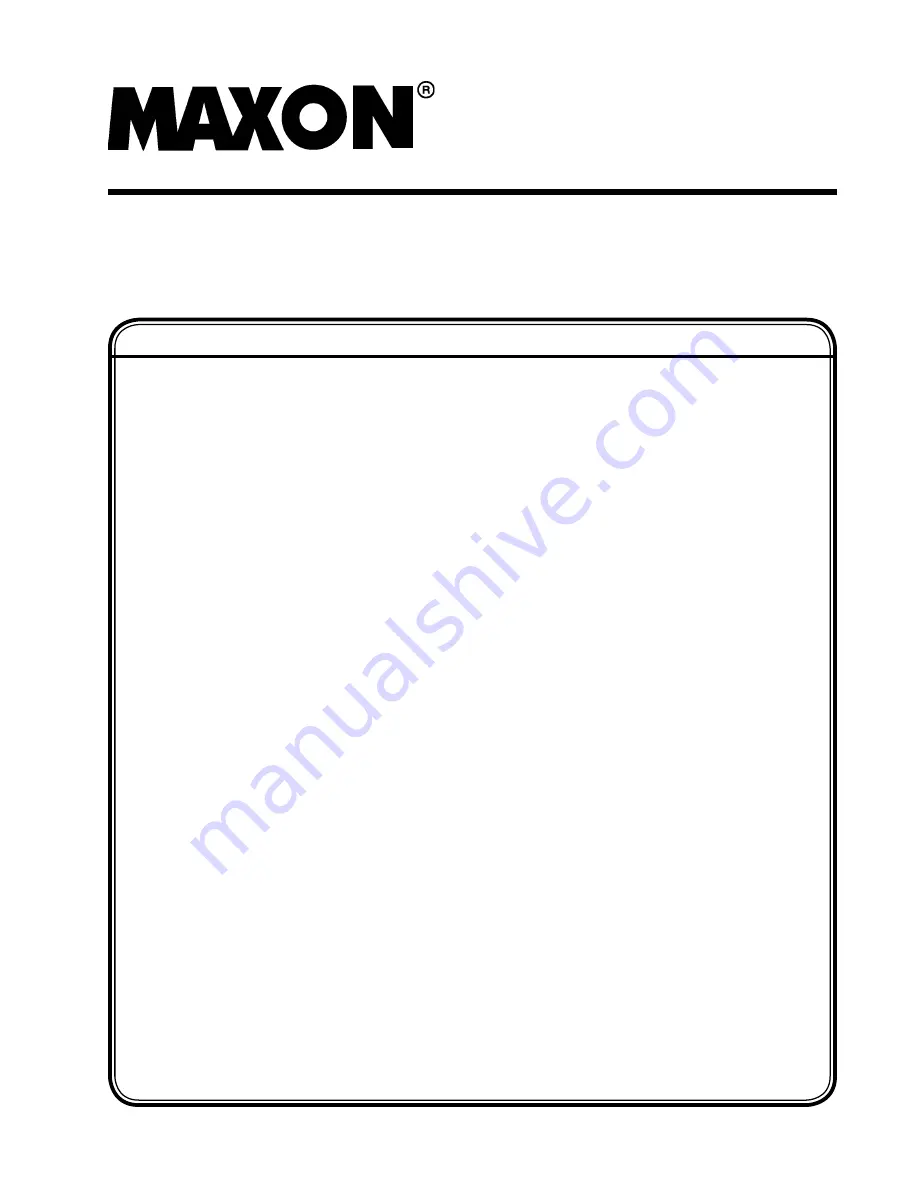
LIFT CORP.
11921 Slauson Ave.
Santa Fe Springs, CA. 90670
CUSTOMER SERVICE:
TELEPHONE (562) 464-0099 TOLL FREE (800) 227-4116
FAX: (888) 771-7713
WARRANTY/ RMA POLICY & PROCEDURE
NOTE: For latest version of all Manuals (and replacements), download the
Manuals from Maxon’s website at www.maxonlift.com.
LIFTGATE WARRANTY
Type of Warranty:
Full Parts and Labor
Term of Warranty:
Standard Liftgates - 2 years from ship date or 6,000 cycles
Premium Liftgates - 2 years from ship date or 10,000 cycles
This warranty shall not apply unless the product is installed, operated and maintained in accordance with MAXON Lift’s specifi cations as set forth in
MAXON Lift’s Installation, Operation and Maintenance manuals. This warranty does not cover normal wear, maintenance or adjustments, damage or
malfunction caused by improper handling, installation, abuse, misuse, negligence, or carelessness of operation. In addition, this warranty does not
cover equipment that has had unauthorized modifi cations or alterations made to the product.
MAXON agrees to replace any components which are found to be defective during the fi rst 2 years of service, and will reimburse for labor based on
MAXON’s Liftgate Warranty Flat Rate Schedule. (Copy of the Flat Rate is available at
www.maxonlift.com
.)
All warranty repairs must be performed by an authorized MAXON warranty facility. For any repairs that may exceed $500, including parts and labor,
MAXON’s Technical Service Department must be notifi ed and an “Authorization Number” obtained.
All claims for warranty must be received within 30 Days of the repair date, and include the following information:
1. Liftgate Model Number and Serial Number
2. The End User must be referenced on the claim
3. Detailed Description of Problem
4. Corrective Action Taken, and Date of Repair
5. Parts used for Repair, Including MAXON Part Number(s)
6. MAXON R.M.A. # and/or Authorization # if applicable (see below)
7. Person contacted at MAXON if applicable
8. Claim must show detailed information i.e. Labor rate and hours of work performed
Warranty claims can also be placed online at
www.maxonlift.com.
Online claims will be given priority processing.
All claims for warranty will be denied if paperwork has not been received or claim submitted via Maxon website for processing by MAXON’s Warranty
Department within 30 days of repair date.
All components may be subject to return for inspection, prior to the claim being processed. MAXON products may not be returned without prior written
approval from MAXON’s Technical Service Department. Returns must be accompanied by a copy of the original invoice or reference with original
invoice number and are subject to a credit deduction to cover handling charges and any necessary reconditioning costs.
Unauthorized returns will be
refused and will become the responsibility of the returnee.
Any goods being returned to MAXON Lift must be pre-approved for return, and have the R.M.A. number written on the outside of the package in plain
view, and returned freight prepaid. All returns are subject to a 15% handling charge if not accompanied by a detailed packing list. Returned parts
are subject to no credit and returned back to the customer. Defective parts requested for return must be returned within 30 days of the claim date for
consideration to:
MAXON Lift Corp.
10321 Greenleaf Ave., Santa Fe Springs, CA 90670
Attn: RMA#__
MAXON’s warranty policy does not include the reimbursement for travel time, towing, vehicle rental, service calls, oil, batteries or loss of income due to
downtime. Fabrication or use of non Maxon parts, which are available from MAXON, are also not covered.
MAXON’s Flat Rate Labor Schedule takes into consideration the time required for diagnosis of a problem.
All Liftgates returned are subject to inspection and a 15% restocking fee. Any returned Liftgates or components that have been installed or not returned
in new condition will be subject to an additional reworking charge, which will be based upon the labor and material cost required to return the Liftgate or
component to new condition.
PURCHASE PART WARRANTY
Term of Warranty: 1 Year from Date of Purchase.
Type of Warranty: Part replacement only. MAXON will guarantee all returned genuine MAXON replacement parts upon receipt and inspection of parts
and original invoice.
All warranty replacements parts will be sent out via ground freight. If a rush shipment is requested, all freight charges will be billed to the requesting
party.
Содержание RA-35
Страница 1: ...M 13 03 REV C MAY 2016 MAXON Lift Corp 2016 MAINTENANCE MANUAL RA 35 RA 45 ...
Страница 2: ......
Страница 36: ......