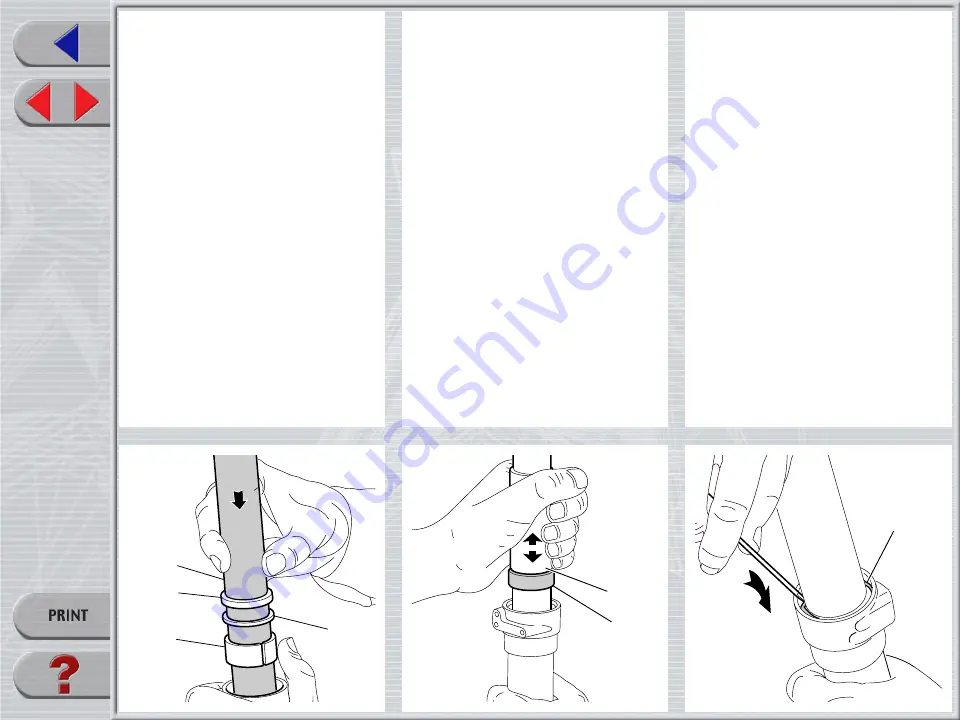
Monster
T
18
16
13
17
16
B
15
FIG. 18
Gently insert the stanchion tube
(13)
into
the slider from the bushing side.
Fit the guide bushing
(18)
and the bushing
washer
(17)
into the slider seat by hand.
FIG. 19
Press the oil seal
(16)
into place until it
touches the lower washer
(17)
by using the
seal press
(B)
.
FIG. 20
Insert the stop ring
(15)
making sure it is
properly seated into place.
Use buffer
(B)
to properly seat the ring into
the slider.