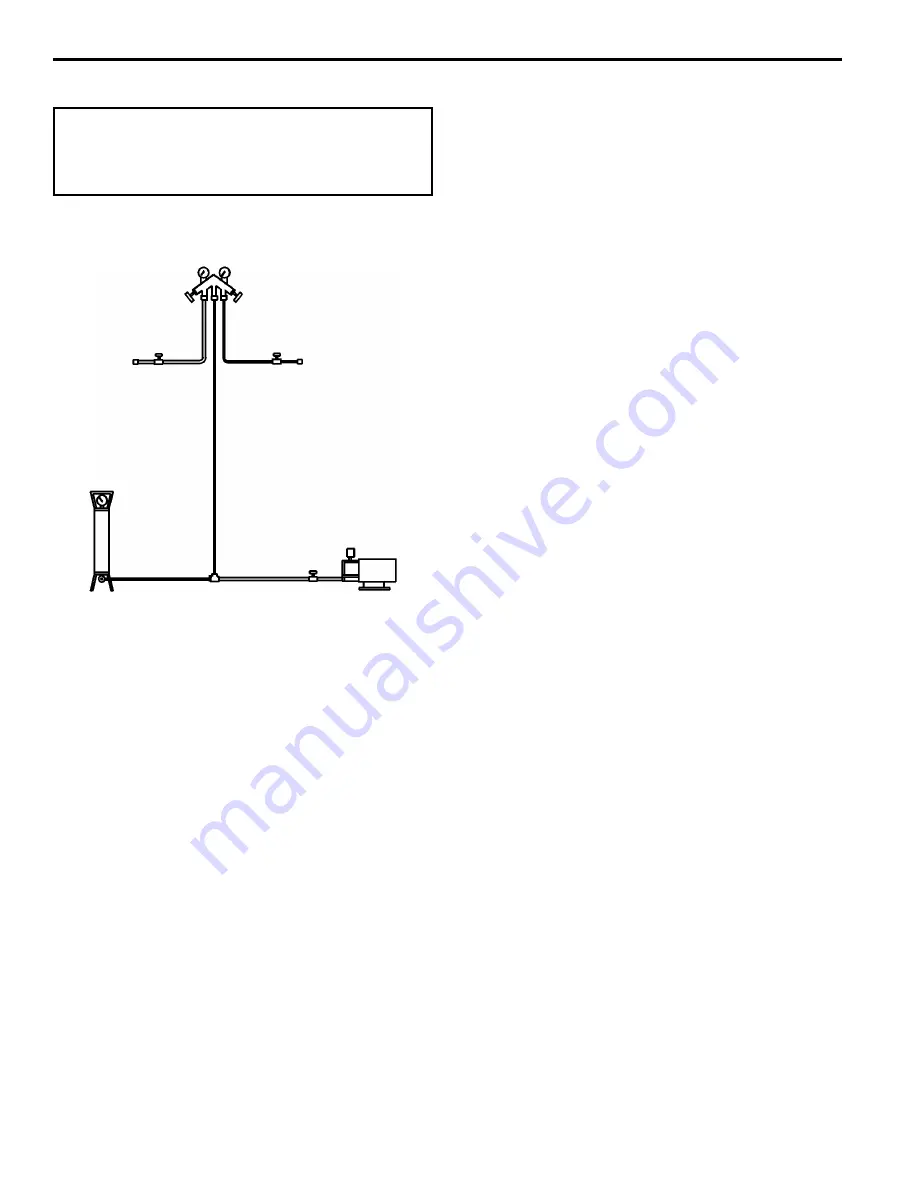
46
Refrigeration System
Self-Contained Charging Procedures
2.
Close the vacuum pump valve, the low side
service valve, and the low side manifold gauge
valve.
Important
The charge is critical on all Manitowoc ice
machines. Use a scale or a charging cylinder to
ensure the proper charge is installed.
3.
Open the high side manifold gauge valve, and
backseat the high side service valve.
1.
Be sure the toggle switch is in the OFF position.
4.
Open the charging cylinder and add the proper
refrigerant charge (shown on nameplate)
through the discharge service valve.
HIGH SIDE
SERVICE
VALVE
SIDE
VICE
VALVE
BACKSEATED
FRONTSEATED
OPEN
CLOSED
MANIFOLD SET
OPEN
CLOSED
VACUUM PUMP/
RECOVERY UNIT
CHARGING
CYLINDER
SV1404B
5.
Let the system “settle” for 2 to 3 minutes.
6.
Place the toggle switch in the ICE position.
7.
Close the high side on the manifold gauge set.
Add any remaining vapor charge through the
suction service valve (if necessary).
LOW
SER
NOTE: Manifold gauges must be removed properly
to ensure that no refrigerant contamination or loss
occurs.
8.
Make sure that all of the vapor in the charging
hoses is drawn into the ice machine before
disconnecting the charging hoses.
A.
Run the ice machine in freeze cycle.
B.
Close the high side service valve at the ice
machine.
C.
Open the low side service valve at the ice
machine.
Charging Connections
D.
Open the high and low side valves on the
manifold gauge set. Any refrigerant in the
lines will be pulled into the low side of the
system.
E.
Allow the pressures to equalize while the ice
machine is in the freeze cycle.
F.
Close the low side service valve at the ice
machine.
Remove the hoses from the ice machine and install
the caps.
Содержание Marine Q 1000
Страница 60: ...56 Refrigeration System Section 7 ...
Страница 61: ......