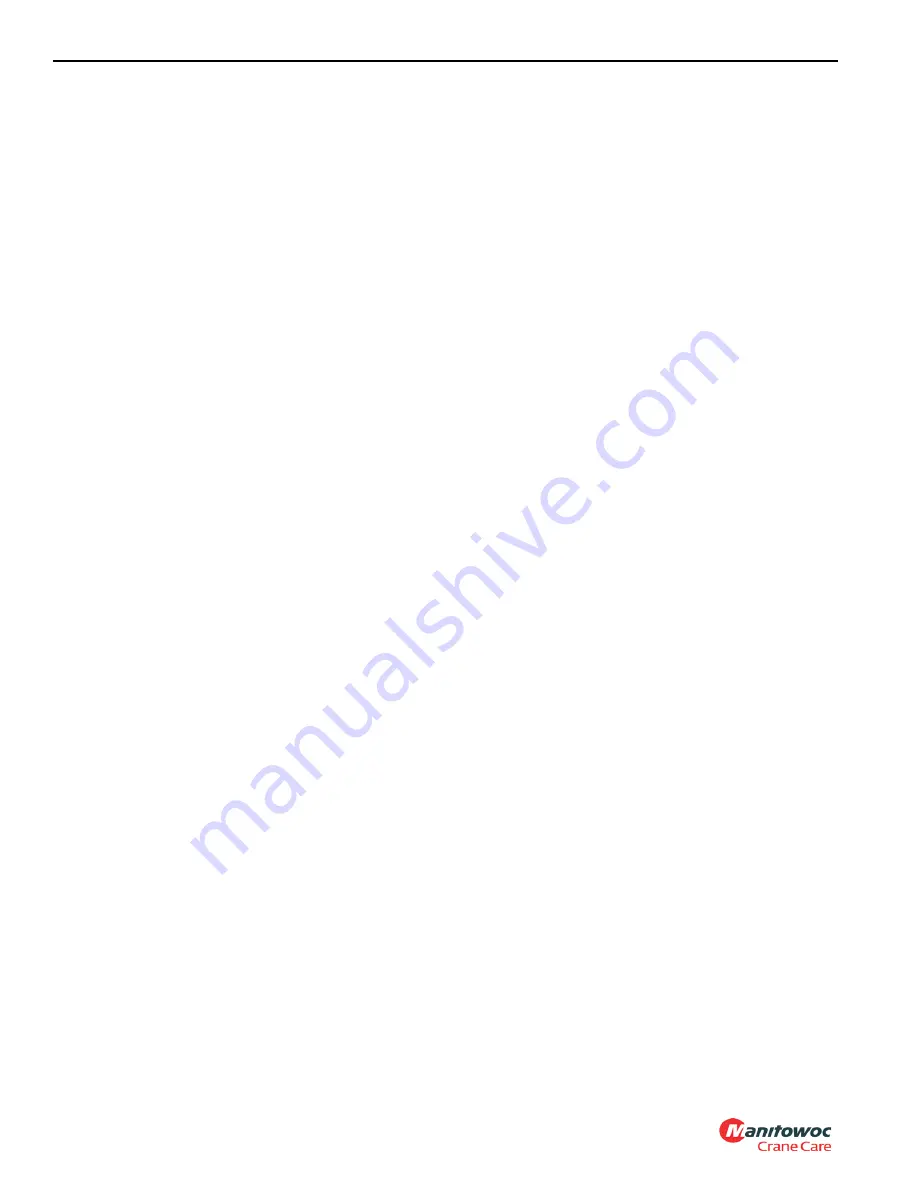
UNDERCARRIAGE
RT770E
8-26
Published 11/26/2014, Control # 447-05
PARK BRAKE SOLENOID VALVE
Description
The park brake solenoid valve is located on the front side of
the carrier aft center frame cross member. The valve is a
three-way two position solenoid valve. The park brake valve
is used to control the application of the crane’s spring-
applied, hydraulically-released parking brake.
Positioning the Park Brake Switch to OFF shifts the three-
way, two-position solenoid valve so hydraulic oil can flow to
the parking brake actuator, extending it. When the actuator
extends, it releases the park brake.
Positioning the Park Brake Switch to ON shifts the three-way,
two-position solenoid valve so hydraulic oil can drain from
the actuator. The parking brake actuator’s rod retracts,
forcing hydraulic oil through the valve and the case drain
manifold back to the transmission reservoir. As the actuator
retracts, it applies the parking brake.
A pressure switch is installed in the line to the actuator.
When the park brake is applied, a lack of hydraulic oil
pressure keeps the pressure switch closed, which turns on
the red LED indicator located in the steering column display.
When the park brake is released, pressure buildup opens the
switch, which turns off the indicator.
Maintenance
Removal
1.
Tag and disconnect the electrical connector from the
valve.
2.
Tag and disconnect the hydraulic lines attached to the
valve. Cap or plug lines and ports. Remove the valve.
Installation
1.
Position the valve and connect the hydraulic lines to the
valve as tagged during removal.
2.
Connect the electrical connector to the valve as tagged
during removal.
3.
Apply and release the park brake several times. Verify
the park brake holds the crane when applied. Verify the
park brake doesn’t drag when released.
4.
Check for leaks. Make repairs as needed.
OUTRIGGER
Outrigger Circuit
Description
The outrigger circuit consists of four extension cylinders, four
jack cylinders, an integrated outrigger/rear steer valve, front
and rear outrigger control manifolds, pilot operated check
valves and an Outrigger Monitoring System (OMS)
(Optional—Standard in North America). The front two
extension cylinders are mounted in the front outrigger beams
and the rear two extension cylinders are mounted in the rear
outrigger beams. The front and rear outrigger beams are
mounted on their respective outrigger boxes; in turn the jack
cylinders are mounted on the end of each outrigger beam.
The integrated outrigger/rear steer valve is mounted on the
front face of the carrier frame front cross member. The front
and rear outrigger control manifolds are mounted on the
inside center of their respective outrigger box. The OMS (if
equipped) consists of a string potentiometer sensor mounted
inside each outrigger box. The sensor is connected by a
cable to the outrigger beam to monitor its position—full, half
or retracted.
The outrigger control station is are located in the left front of
the cab. Both the integrated outrigger valve and the manifold
solenoid valves are electrically actuated from these controls.
The solenoid switches must be held depressed to actuate
the solenoid valve. The integrated outrigger valve switch is
spring loaded to the off position. The console is placarded
with switch positions.
A sight bubble level is mounted on the left side of the cab be
the door latch plate. The sight bubble level provides the
operator with a visual indication of crane level attitude.
Theory Of Operation
The appropriate Extension/Stabilizer Switch must be
depressed before the Outrigger Extend/Retract Switch is
depressed. Depressing one of the outrigger selector
switches causes that solenoid valve to open. As the
Outrigger Switch is moved, the integrated outrigger valve
spool shifts allowing flow to either the extend or retract line
as applicable. If the Outrigger Switch is in the EXTEND
position, the flow continues through the open solenoid valve
to the piston side of the cylinder. If the jack cylinder is to be
extended, the flow first unseats the cylinder check valve then
extends the cylinder. The oil from the rod end flows through
the integrated outrigger valve, and then to the reservoir.
When the Outrigger Switch is in the RETRACT position, the
flow through the selector valve is directed to the rod side of
the cylinder. The oil in the piston side flows through the open
solenoid back to the integrated outrigger valve. If a jack
cylinder is to be retracted, then pilot pressure from the
pressurized retract line unseats the cylinder check valve
allowing oil to flow from the piston side through the open
solenoid valve to the integrated outrigger valve. The
integrated outrigger valve directs the flow to the reservoir.
The integrated outrigger/rear steer valve contains one relief
valve that is set at 2500 psi (17,200 kPa).
Содержание Grove RT770E
Страница 3: ...Service Maintenance Manual Grove RT770E ...
Страница 4: ......
Страница 40: ...INTRODUCTION RT770E SERVICE MANUAL 1 26 Published 11 26 2014 Control 447 05 THIS PAGE BLANK ...
Страница 124: ...HYDRAULIC SYSTEM RT770E 2 84 Published 11 26 2014 Control 447 05 THIS PAGE BLANK ...
Страница 126: ...ELECTRICAL SYSTEM RT770E SERVICE MANUAL 3 2 Published 11 26 2014 Control 447 05 FIGURE 3 1 7983 ...
Страница 149: ...4 5 Published 11 26 2014 Control 447 05 RT770E SERVICE MANUAL BOOM 4 GROVE FIGURE 4 2 ...
Страница 150: ...BOOM RT770E SERVICE MANUAL 4 6 Published 11 26 2014 Control 447 05 FIGURE 4 2 continued ...
Страница 151: ...4 7 Published 11 26 2014 Control 447 05 RT770E SERVICE MANUAL BOOM 4 GROVE FIGURE 4 2 continued ...
Страница 152: ...BOOM RT770E SERVICE MANUAL 4 8 Published 11 26 2014 Control 447 05 FIGURE 4 2 continued ...
Страница 153: ...4 9 Published 11 26 2014 Control 447 05 RT770E SERVICE MANUAL BOOM 4 GROVE FIGURE 4 2 continued ...
Страница 154: ...BOOM RT770E SERVICE MANUAL 4 10 Published 11 26 2014 Control 447 05 FIGURE 4 2 continued ...
Страница 224: ...5 24 Published 11 26 2014 Control 447 05 HOIST AND COUNTERWEIGHT RT770E This Page Blank ...
Страница 276: ...POWER TRAIN RT770E 7 30 Published 11 26 2014 Control 447 05 THIS PAGE BLANK ...
Страница 300: ...UNDERCARRIAGE RT770E 8 24 Published 11 26 2014 Control 447 05 FIGURE 8 28 ...
Страница 321: ...9 9 RT770E LUBRICATION 9 Published 11 26 2014 Control 447 05 GROVE 7114 17 1 4 2 7114 20 7114 10 3 FIGURE 9 1 ...
Страница 323: ...9 11 RT770E LUBRICATION 9 Published 11 26 2014 Control 447 05 GROVE 7114 17 11 12 7114 9 FIGURE 9 2 8130 1 ...
Страница 329: ...9 17 RT770E LUBRICATION 9 Published 11 26 2014 Control 447 05 GROVE 42 7114 25 7114 24 41a 7649 21 FIGURE 9 5 40 8130 2 ...
Страница 331: ...9 19 RT770E LUBRICATION 9 Published 11 26 2014 Control 447 05 GROVE FIGURE 9 6 8130 1 51 52 50 ...
Страница 336: ...LUBRICATION RT770E 9 24 Published 11 26 2014 Control 447 05 72 73 74 73 74 72 73 74 73 74 FIGURE 9 8 8133 ...
Страница 343: ...9 31 RT770E LUBRICATION 9 Published 11 26 2014 Control 447 05 GROVE 84 7114 30 FIGURE 9 11 85 7115 33 8130 2 ...
Страница 347: ...9 35 RT770E LUBRICATION 9 Published 11 26 2014 Control 447 05 GROVE 7649 22 101 100 FIGURE 9 13 8130 2 ...
Страница 348: ...LUBRICATION RT770E 9 36 Published 11 26 2014 Control 447 05 FIGURE 9 14 102 8130 2 ...
Страница 356: ......
Страница 357: ......