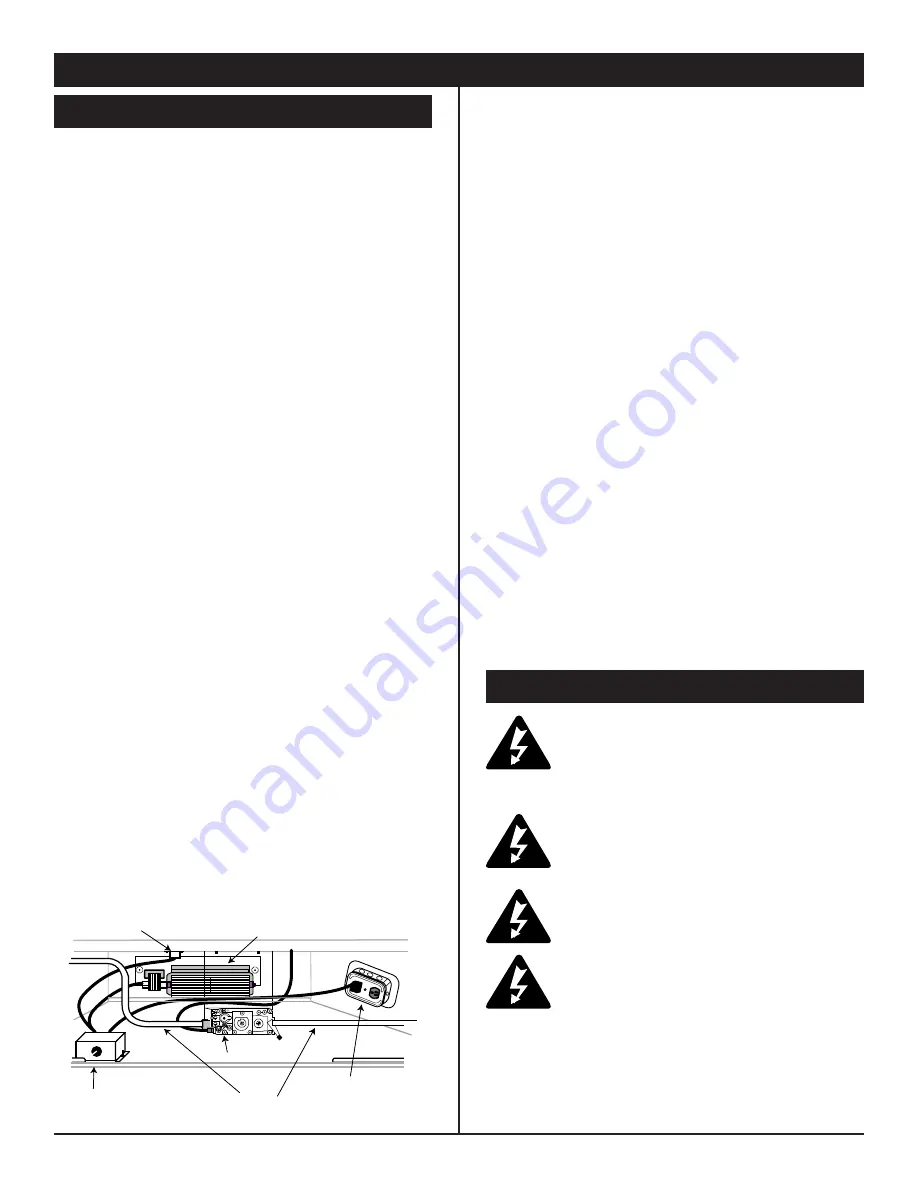
33/36/39/43 BDVT
-32-
10002555/0
Vermont Castings, Majestic Products.
O
PTIONAL
A
CCESSORIES
A
VAILABLE
F
AN
K
ITS
FK24 Fan Assembly
This auxiliary fan system increases the efciency of the circu-
lation of the heating air.
The FK24 fan kit allows variable speed control of the circula-
tion fan and also incorporates a heat sensor in the circuit.
Specications
115 Volt / 60 Hz / 56 Watts
Maintenance
The fan itself does not require regular maintenance, however
periodic cleaning of the fan and the surrounding area is
required.
Check the area under the control door (lower louvre assembly)
and in front of the fan and wipe or vacuum this area at least
once a month during the operating season.
Installation
The fan assembly and other components are supplied fully
wired eliminating the need for a licensed electrician to carry
out the installation
If hard wiring the fan in using Method B (following) we
strongly recommend the use of a licensed electrician.
1 Open the lower Louvre assembly. Maneuver the fan &
bracket assembly around the gas valve and lines to locate
the unit onto the screw studs on the back of the replace
2 Install the thermal sensor under the bottom of the rebox,
locating it over the two 10 mm studs and secure it with
nuts.
3 Locate the fan speed control unit. This can be tted
behind the lower louvre assembly as in Fig. 54 or located
remotely in a conveniently located wall mounted electrical
box. Remote location of the speed control will require
suitable extension of the component wiring.
4 The power supply may be connected in 2 ways:
Method A
Route the 6' lead tted to the unit to a conveniently
located wall socket.
Method B
The EB1 receptacle box (Pt. # ZA1200) may be hard
wired into the house supply. The fan lead is then plugged
into the EB1 box.
FK12
This auxiliary fan system increases the efciency of the circu-
lation of the heating air.
The FK12 Fan Assembly is a xed speed fan system and does
not allow for variable speed control. It does not use the speed
control unit or the heat sensor used in the FK24 Kit.
Specications
115 Volts / 60 Hz / 56 Watts.
Maintenance
The fan itself does not require regular maintenance, however
periodic cleaning of the fan and the surrounding area is
required.
Check the area under the control door (lower louvre assembly)
and in front of the fan and wipe or vacuum this area at least
once a month during the operating season.
Installation
The fan assembly is supplied fully wired eliminating the need
for a licensed electrician to carry out the installation
1. Open the lower Louvre assembly. Maneuver the fan &
bracket assembly around the gas valve and lines to locate
the unit against the back wall of the appliance, resting on
the base.
2. With the protective cover removed from the self-adhesive
‘Velcro’ strips apply mild pressure to the fan & bracket
unit to secure the strips to the metal panels. No further
securing is required.
3. Power to the fan can be supplied by plugging the supplied
lead into a conveniently located wall socket or by using a
hard-wired EB1 connector box.
FAN SPEED SWITCH
VALVE
GAS
LINES
ELECTRICAL
BOX
FAN
THERMAL SENSOR
W
IRING
I
NSTRUCTIONS
The replace, when installed, must be electri-
cally connected and grounded in accordance
with local codes or, in the absence of local
codes, with the current CSA C22.1 Canadian
Electric Code.
For U.S.A. installations follow the local codes
and the national electrical code ANSI/NFPA No
70.
Should this fan require servicing or repair the
power supply must be disconnected. For rewir-
ing of any replacement parts see Fig. 55
Any electrical re-wiring of this fan must be done
by a licensed electrician.
Method A
(Not using EB1, Fig. 55)
1. Connect the ground wire of the power supply line to the
ground stud located on the base of the rebox.
2. Connect the black wire of the supply line to either termi-
nal of the speed control unit.
Fig. 54