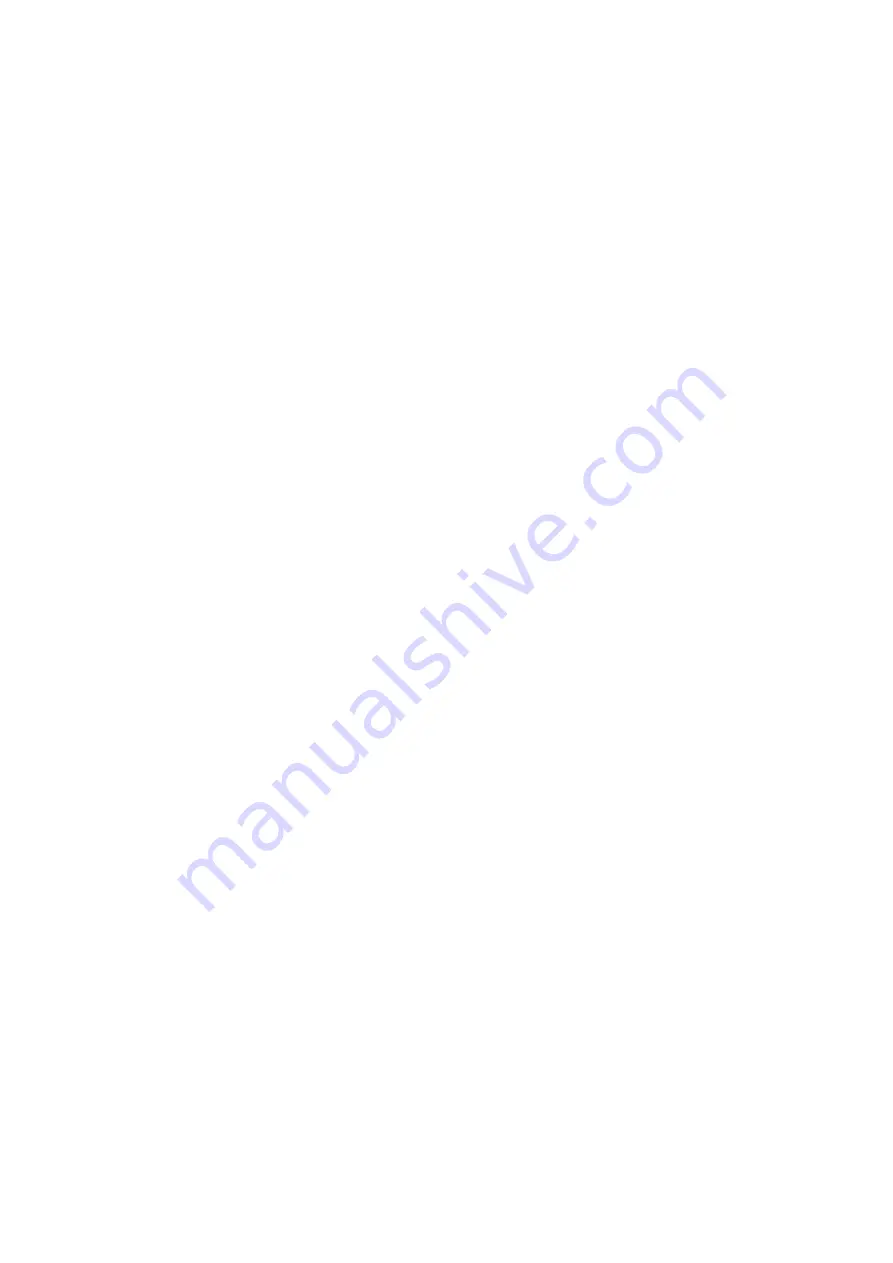
FSD-TD - Installation Operation and Maintenance Instructions
2.
Important continued
2.6 Refer to actuator label for wiring of actuator and page 12.
2.7 Refer to section 19 for testing. Complete Installation Check List (at end of this document) and retain
for future reference.
2.8 For existing dry walls – When cutting the opening for damper, and (partial) removal of stud is
unavoidable, ensure the structure is sufficiently supported to conform to the design specification.
See Page 2.
2.9 Dry wall openings must be lined. Please see page 2.
2.10 Ensure that appropriate ‘fire-rated’ plasterboard is used throughout the construction of drywall
partitions that need to act as fire separation barriers.
2.11 Ductwork to be fitted and connected to the damper spigot in accordance with DW 144/145.
Aluminum rivets should be used (to act as breakaway joint).
2.12 Where more than one duct penetrates a wall or floor, adjacent fire damper assemblies should be
separated by a structural element with a minimum width of 200mm (to comply with
BS EN1366-2 13.6).
2.13 EMinimum distance from adjacent dampers and structures.
Fire dampers must be separated by a structural 200mm minimum distance between cases and
have a minimum 75mm between the fire damper case and a construction element (wall/floor).
Other services should not share the same opening as the installed damper.
3.
Equipment Required
3.1 Equipment and tools will vary dependent upon the fire barrier construction that the damper is being
installed within. Standard equipment normally used for the building of the particular barrier should
suffice.
3.2 Access-equipment as necessary.
3.3 Temporary support equipment (to retain damper in position).
3.4 Cordless drill with 2,5mm and 10mm drill bits for fitting TF.
3.5 4mm (drywall) and 8mm (concrete/masonry) drill bits as required, for the AF fixing frame fixing
holes.
3.6 Phillips №2 screwdriver to suit thermal fuse screws.
3.7 Screwdriver to suit junction box terminals.
3.8 8mm A/F spanner for motor fixing bolt.
3.9 12mm A/F Spanner for TD drive shaft.
4.
Preparation for Installation
4.1 For each damper installation type, refer to the relevant installation detail below.
4.2 Remove packaging materials with the exception of the actuator packaging - leaving this in place will
protect the actuator wiring / thermal fuse whilst the damper is being installed.
4.3 Before installation, the damper should be inspected to ensure that it has not been damaged and is
in good condition.
4.4 Check damper (label) reference and size to site specification.
4.5 Determine required position of damper. Check sufficient space exists to fit the product. Ensure any
services (e.g. electrical/plumbing) within the structure or running close to the structure will not be
affected.
4.6 Consideration should be given to the depth of the wall, relative to damper case length, ensuring that
the case is not exposed once fitted.
4.7 Drill the relevant peripheral EASY FIX ® pilot holes for the wall type.
Page 2