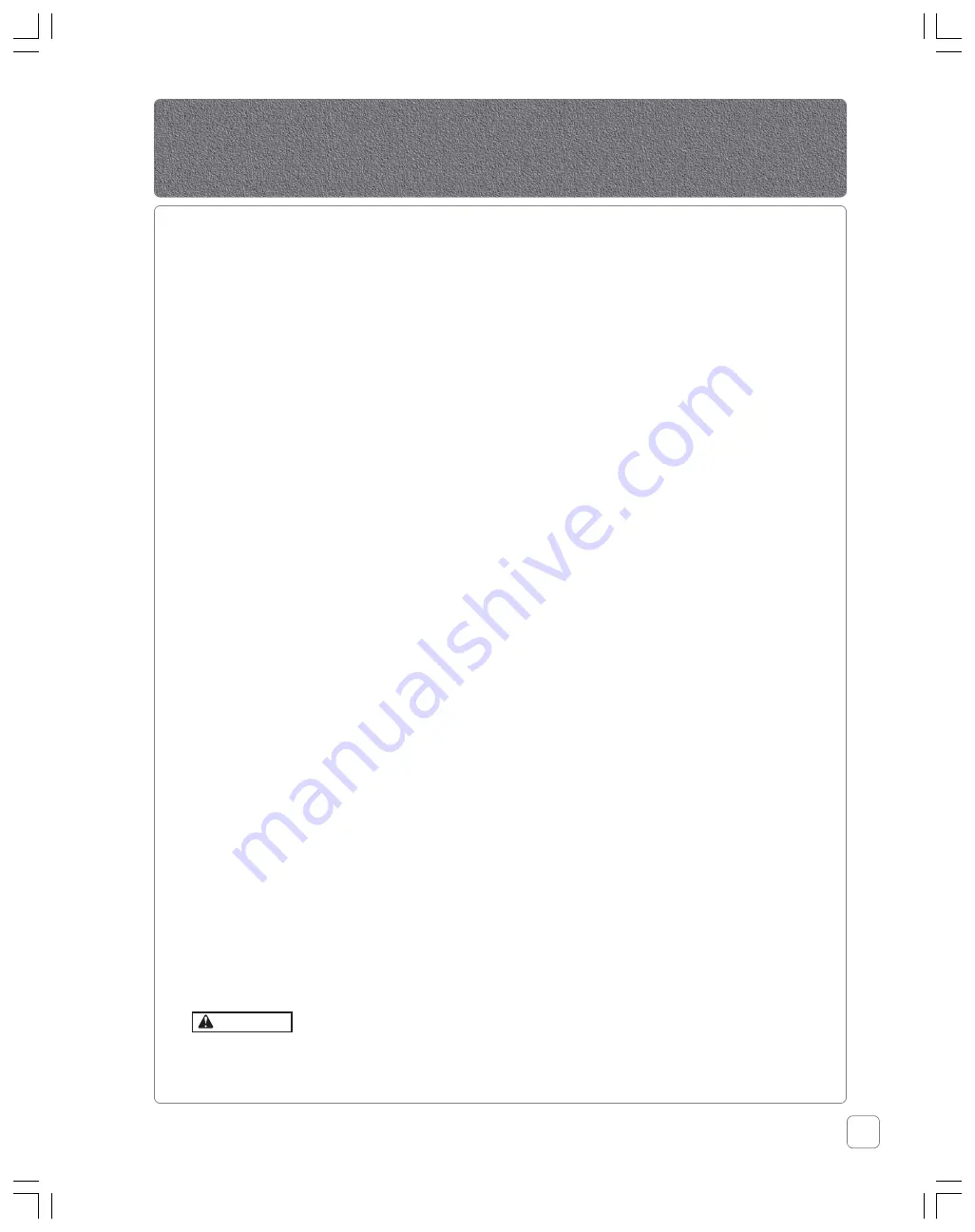
61
the top link force the top link spring (19)
(20) will deflect. This displacement is
passed to link outer draft sensing (5). The
movement of link outer draft sensing is
transfered to spool control valve (22) with
certain amplification through DC feedback
rod (8) and link DC actuating (12). This
results in lifting of implement in operation
till the set force is reached. If the implement
is lifted more then required which will
reduce the top link crank back ward will
lower the hitch till the set draft is achieved.
d. Check Valve
The ball is kept on its seat by the spring until
pressure in the pump line is approximately
75 PSI. This ensure that in the drop position
the lift arm fall will not be allowed by low
pressure oil, which is circulated by the pump
to the reservoir through the regulator port
the check valve also locks the oil in the
cylinder when controls are in the natural (or
hold) position.
e.
The Relief Valve
The relief valve ball become unseated
allowing the high pressure oil to drain to
the reservoir through port when the
pressure in the system exceeds the specified
figure and overcomes the spring. The relief
valve is not adjustable.
f.
Cylinder cushion valve
This valve is fitted on the cylinder pistion.
The purpose of the cylinder cushion valve
is to protect the system against shock loads
when driving over a bumpy road with a
bouncing implement. In this pressure way
due to shock loads or many thousand and
p.s.i. may result. As soon as these shocks
exceed specified limits the cylinder cushion
valve will become unseated, relieving
pressure in the power cylinder.
Never drive with the
position control lever against the upper
limit stop
g. Remote Cylinder
To operate, single-acting cylinders, the
adjustable stop is moved to contact the
upper limit stop, the position lever is then
used to raise the lift arms full. Close the
isolating valve. With the position lever
against the adjustable stop, the remote
cylinder is in the neutral or hold position.
To operate the remote cylinder the lever is
spring over the adjustable stop until it is in
contact with the limit stop. The valve
operation for remote cylinder LIFT and as
soon as, cylinders are extnded, return the
position lever to the hold position. To allow
the cylinder to retract, move the lever
forward from the hold position
4. TEST PROCEDURE
a.
General
Before Investigation any service problem
the following basic points should be
checked Hydraulic system that has failed
step by step.
–
Fluid level
–
Age condition, and type of fluid
–
External leakage
–
Air in the system
–
Operating temperature of 50º–20ºC.
The Test procedure covers the following tests.
1. Hydraulic pump capacity
2. Plain relief valve setting
3. Cylinder cushion valve setting
b. Hydraulic pump capacity may be
measured when pump is installed, or on
a test bench.
Test valves see specification.
Pump is designed for 16 Lts.
Maximum permissible operation speed
2500 rpm.
CAUTION :
Hy-tec Hydraulics
Содержание YUVRAJ 215
Страница 2: ......
Страница 4: ......
Страница 8: ......
Страница 34: ......
Страница 48: ......
Страница 50: ......
Страница 53: ...53 Schematic Layout Showing Details of Control Valve Components in Neutral Position Hy tec Hydraulics...
Страница 55: ...55 Lifting Position Hy tec Hydraulics...
Страница 56: ...56 Lowering Position Hy tec Hydraulics...
Страница 58: ...58...
Страница 59: ...59...
Страница 76: ......
Страница 85: ...85...