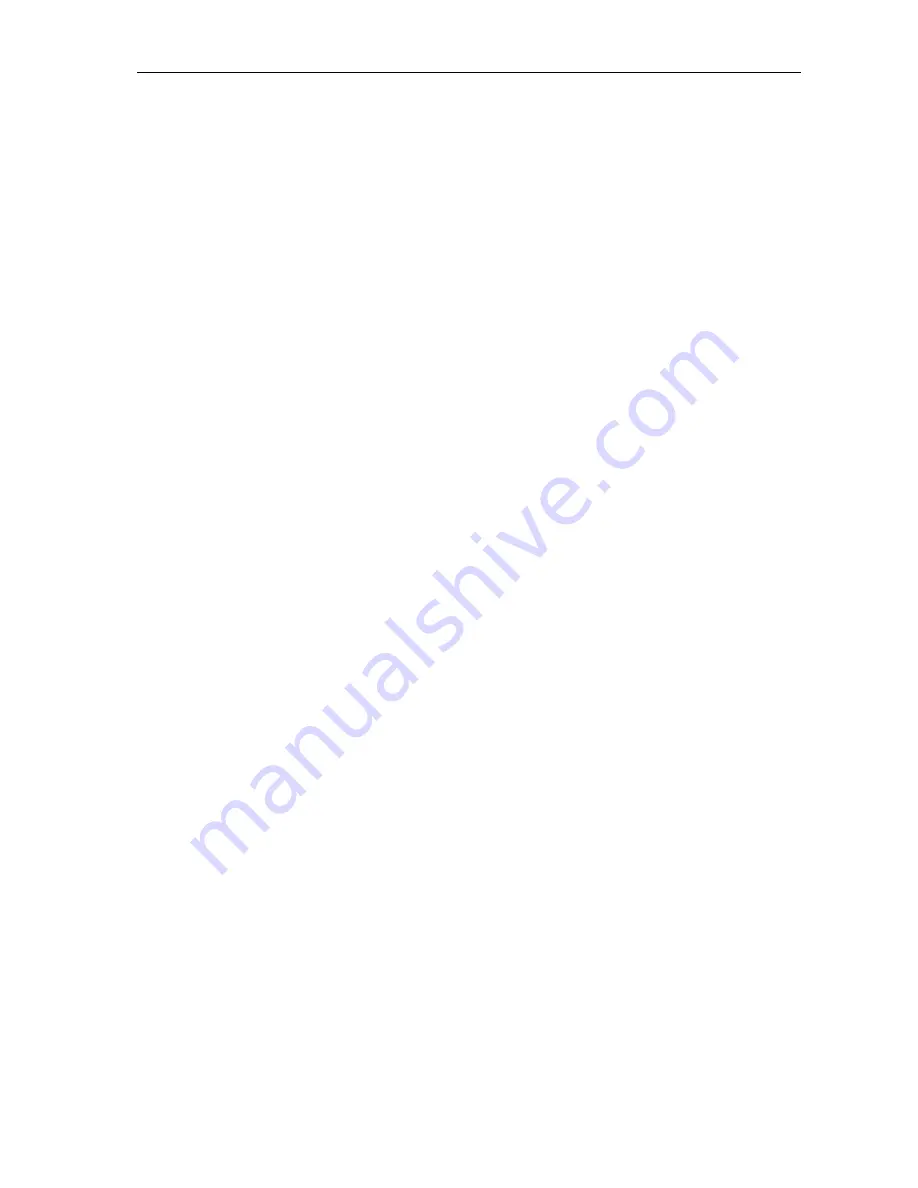
TWIN F 3.0 A / TWIN F 3.0 U
D1 5002BA1-GB01
37
9 CHAPTER 9 - MAINTENANCE
O
NLY TRAINED PERSONNEL WHO KNOW HOW THE LIFT WORKS
,
MUST BE
ALLOWED TO SERVICE THE LIFT
To service properly the lift, the following has to be carried out:
•
use only genuine spare parts as well as equipment suitable for the work
required
•
follow the scheduled maintenance and check periods shown in the manual
•
discover the reason for possible failures such as too much noise, overheating,
oil blow-by, etc.
•
Refer to documents supplied by the dealer to carry out maintenance:
•
functional drawing of the electric and hydraulic equipment
•
exploded views with all data necessary for spare parts ordering
•
list of possible faults and relevant solutions.
B
EFORE CARRYING OUT ANY MAINTENANCE OR REPAIR ON THE LIFT
,
DISCONNECT THE POWER SUPPLY
,
PADLOCK THE GENERAL SWITCH AND KEEP
THE KEY IN A SAFE PLACE TO PREVENT UNAUTHORISED PERSONS FROM
SWITCHING ON OR OPERATING THE LIFT
.
9.1 Ordinary
maintenance
The lift has to be properly cleaned at least once a month. Use self-cleaning clothes.
T
HE USE OF WATER OR INFLAMMABLE LIQUID IS STRICTLY FORBIDDEN
.
Be sure the rod of the hydraulic cylinders is always clean and not damaged since this
may result in leakage from seals and, as a consequence, in possible malfunctions.
9.2 Periodic
maintenance
Every 3 months
Hydraulic circuit
- check oil tank level; refill with oil, if
needed;
- check the circuit for oil leakage. Check
seals for proper conditions and replace
them, if necessary.
Foundation bolts:
- check bolts for proper tightening
Hydraulic pump
- verify that no noise changes take place
in the pump of the control desk when
running and check fixing bolts for proper
tightening
Safety system
- check safety devices for proper
operation
Every 6 months
Oil:
Check oil for contamination or ageing.
Contaminated oil is the main reason for
failure of valves and shorter life of gears
Содержание Twin Series
Страница 4: ...TWIN F 3 0 A TWIN F 3 0 U D1 5002BA1 GB01 II ...
Страница 6: ...TWIN F 3 0 A TWIN F 3 0 U D1 5002BA1 GB01 IV ...
Страница 8: ...TWIN F 3 0 A TWIN F 3 0 U D1 5002BA1 GB01 VI ...
Страница 10: ...TWIN F 3 0 A TWIN F 3 0 U D1 5002BA1 GB01 VIII ...
Страница 14: ...TWIN F 3 0 A TWIN F 3 0 U D1 5002BA1 GB01 4 ...
Страница 19: ...TWIN F 3 0 A TWIN F 3 0 U D1 5002BA1 GB01 9 Figure 2 LIFT ...
Страница 21: ...TWIN F 3 0 A TWIN F 3 0 U D1 5002BA1 GB01 11 Figure 3 CONTROL DESK ...
Страница 34: ...TWIN F 3 0 A TWIN F 3 0 U D1 5002BA1 GB01 24 ...
Страница 37: ...TWIN F 3 0 A TWIN F 3 0 U D1 5002BA1 GB01 27 Figure 16 HYDRAULIC PIPES CONNECTION Platform 1 Platform 2 ...
Страница 45: ...TWIN F 3 0 A TWIN F 3 0 U D1 5002BA1 GB01 35 ...
Страница 46: ...TWIN F 3 0 A TWIN F 3 0 U D1 5002BA1 GB01 36 ...
Страница 51: ......