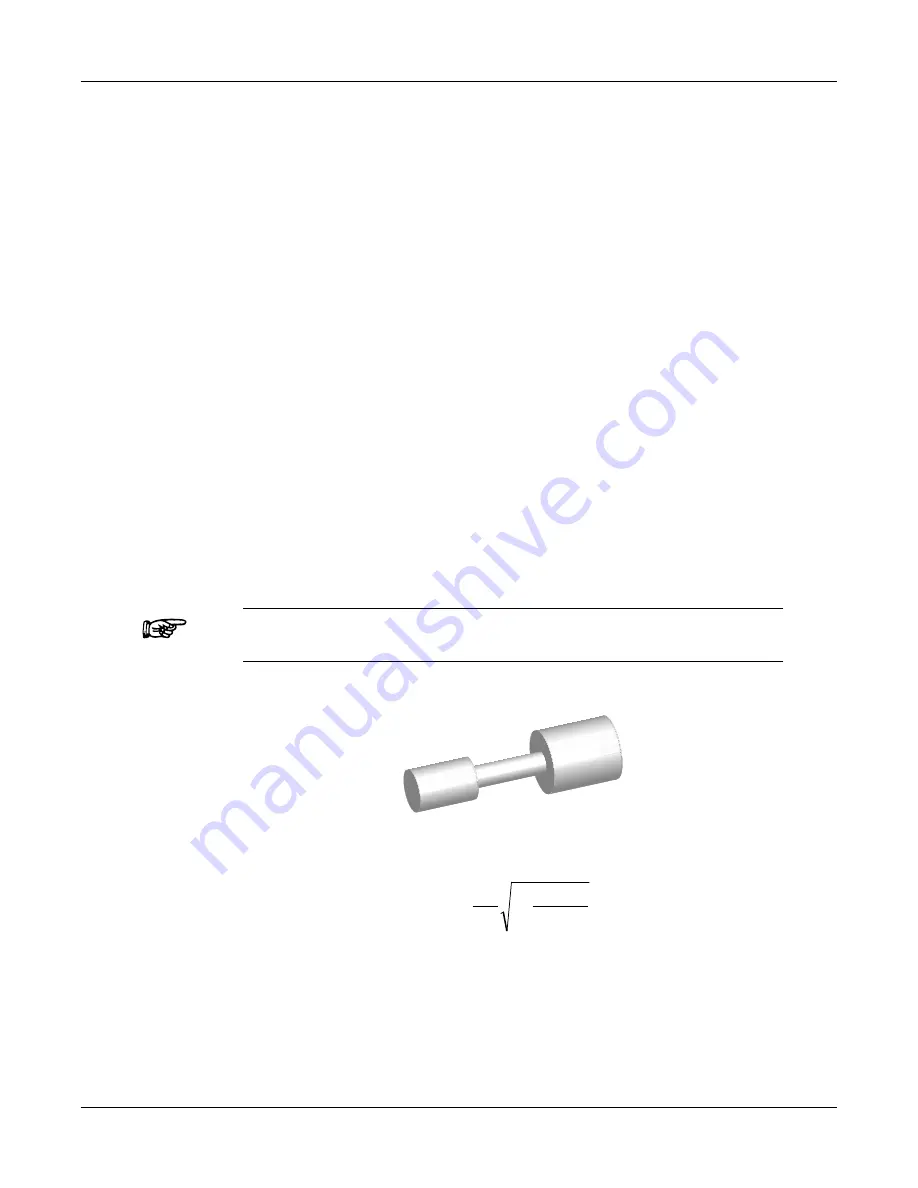
24
Magtrol TM Series In-Line Torque Transducers
Chapter 2 – Installation / Configuration
2.4
mounting limits
During static measurements, the nominal torque may be surpassed in order to reach the plastic
deformation torque limit. When exceeding the nominal torque, any extraneous loads such as axial,
shearing and bending forces must be avoided.
2.4.1
d
ynaMIc
T
orque
Static and dynamic measurements differ from one another by the evolution of torque over time. A
constant torque produces static measurements, whereas varying torques can only be determined by
dynamic measurement.
Magtrol TM Series Torque Transducers are designed for the measurement of both static and dynamic
torque, without the need for recalibration.
2.4.2
n
aTural
F
requency
oF
d
rIVe
T
raIn
In order to determine the dynamic torque and frequency response, and to prevent any damage to the system,
it is necessary to calculate the natural frequency of the drive train torsional oscillations. In this system,
however, the deformation area of the measuring flange is the weakest link in the rotating measuring chain
and is subject to torsional vibrations.
In practice, this situation can generate rather complex relations which require demanding calculations.
This may be, for instance, the case for the physical model in which the drive chain is a combination of
torsion springs with intermediate flywheel masses. however, the following simplified model of a drive
chain (
Figure 2–7
) can often be used.
Note:
For a detailed analysis of dynamic response, publications on structural
mechanics should be consulted.
J
1
J
2
C
t
Figure 2–7 Simplified Drive Train Model
2
1
2
1
0
2
1
J
J
J
J
C
f
t
⋅
+
=
π
With: f
0
Natural frequency of system [hz]
C
t
Measuring shaft torsional stiffness [Nm/rad]
J
1
Moment of inertia (driving m co ½ of the measuring shaft) [kgm²]
J
2
Moment of inertia (driven m co ½ of the measuring shaft) [kgm²]