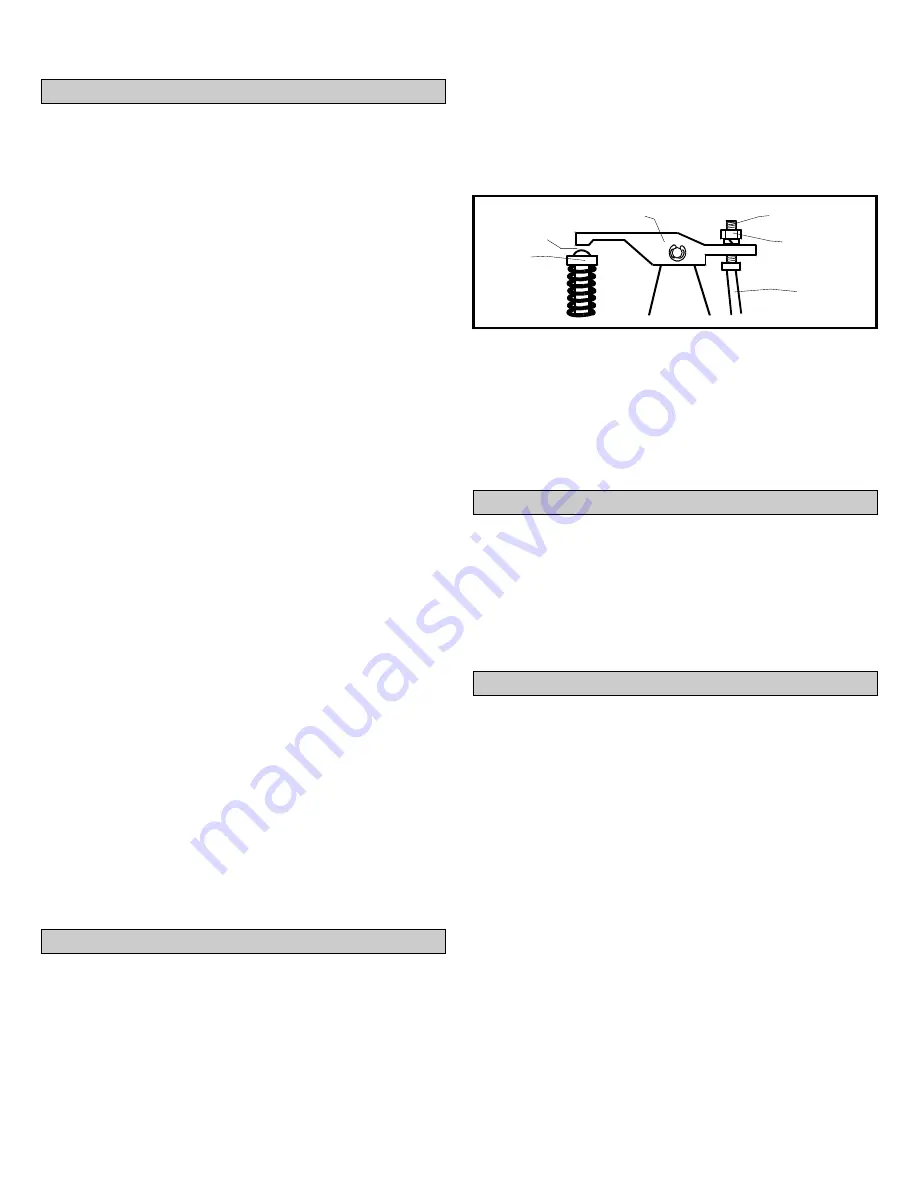
SETTING THE MIXTURE
Now that your engine is broken in, you can set the high and low speed
needle valves for optimum performance.
Note: Be careful to never lean the engine out too much. Remember
that the lubricants for your engine are suspended in the fuel. If you lean
out the fuel mixture too much you will also be lowering the amount of
lubricant entering your engine. Less lubricant means more chance of your
engine overheating and possible engine failure.
q
Setting the High Speed Needle Valve
q
1)
Start the engine and remove the power from the glow plug. Al-
low the engine to warm up for about 1 minute.
q
2)
After the engine has warmed up slowly lean the high speed mix-
ture until the engine reaches peak R.P.M. After reaching peak R.P.M. richen
the mixture slightly until an audible drop in R.P.M. is heard. If you are
using a tachometer this should be between a 200 - 300 R.P.M. drop.
o
3)
With the engine running at full power, carefully lift the nose of
the airplane about 45º into the air. The mixture should not become too
lean, but you may hear a slight increase in R.P.M. If the engine sags, or
loses R.P.M. when you hold the nose up, the mixture is too lean.
Note: R.P.M. will increase about 10% - 30% in the air. This is due to
the forward motion of the aircraft as it is flying. Because of this more air
is entering the carburetor, at a higher force, and causes the mixture to lean
out. Additionally, as the fuel level in the fuel tank goes down, fuel draw
becomes more difficult for the engine, especially during aerobatics, thus
causing the mixture to go lean. It is imperative that you set the mixture
rich while on the ground to compensate for the leaning tendencies that will
happen in the air. Always watch the exhaust during your flight. The en-
gine should leave a noticeable white smoke trail at all times. It there is no
smoke trail, the engine is running too lean. You should land immediately
and reset the mixture.
q
Setting the Low Speed Needle Valve
q
1)
Start the engine and lean out the high speed needle valve as per
the previous steps. Close the throttle until the slowest reliable idle is reached.
Allow the engine to idle for about 30 seconds.
q
2)
Quickly advance the throttle to full. If the engine just stops run-
ning as soon as the throttle is advanced, the idle mixture is too lean. With
the engine stopped, richen the idle mixture about 1/8 of a turn.
q
3)
Repeat steps # 1 and # 2 until the engine will transition from idle
to full throttle smoothly. Minor hesitation in the transition will be normal.
q
4)
If you quickly advance the throttle from idle to full and the en-
gine seems to be very rich during transition (i.e. lots of smoke coming
from the exhaust), the mixture is too rich. With the engine stopped, lean
the idle mixture about 1/8 of a turn.
q
5)
Repeat steps # 1 and # 4 until the engine will transition from idle
to full throttle smoothly. Minor hesitation in the transition will be normal.
VALVE ADJUSTMENT
q
Adjusting the Valves
The Valve clearances are preset from the factory, but will require periodic
adjustment. Reset the valves after the first 1 hour of engine running. After
that, the valves can be checked and adjusted about every 8 hours of run-
ning. Some signs that the valves need adjusting are loss of power, rattling
sounds at low idle or if you have repaired the engine after a crash.
q
1)
With the engine cold, remove the rocker cover on top of the cyl-
inder head by unscrewing the two socket cap screws.
q
2)
Rotate the crankshaft until the piston is at top dead center. Both
valves are closed at this point.
q
3)
The required valve clearance is between .04mm and .10mm mea-
sured between the valve stem and the rocker arm. Use feeler gauges to
check the clearance. The .04mm gauge should pass through the gap with
only slight friction. The .10mm feeler gauge should be tight.
q
4)
Working with one valve at a time, loosen the lock nut using a
small wrench. Use a screwdriver and turn the adjustment screw counter-
clockwise about 1/2 turn. This will open the gap slightly. Slide the .04mm
feeler gauge between the rocker arm and the valve stem. Carefully turn the
adjustment screw clockwise until the rocker arm contacts the feeler gauge.
Using a small wrench, tighten the lock nut.
q
5)
Remove the feeler gauge and double check the gap. Repeat step
# 4 if necessary to achieve the correct setting. Repeat for the second valve.
SERVICE
All Magnum engines returned for warranty service must be within the warranty
terms as stated on the warranty card provided with your engine. Do not return the
engine to the place of purchase. They are not authorized or equipped to perform
warranty work on Magnum products. When requesting warranty service, please
observe the following:
F
Always send the complete engine including the carburetor and muffler. The
engine must be removed from the model.
F
Include a note detailing the problem or service you are requesting. Service
cannot be provided without this information. Include your daytime phone number
in the event we need more details pertaining to the service requested.
F
You may request an estimate of services at the time you return your engine for
service. An omission of this request implies permission for the Magnum Service
Center to service your engine at our discretion.
F
Include a method of payment for any service charges. If not specified, the unit
will be returned to you C.O.D.
F
Please include a check or money order in the amount of $6.50 to cover postage
and handling charges for the return of your engine. Do not send cash.
F
Send the engine to us by United Parcel Service, Federal Express or by Insured
Mail. Postage in not refundable. Send to:
Magnum Service Center
18480 Bandilier Circle
Fountain Valley, CA 92728
Phone (714) 963-0329
Fax (714) 964-6236
Email: [email protected]
MAINTENANCE
q
Avoid running the engine under dusty conditions.
q
At the end of every flying day, purge the engine of fuel by disconnect-
ing the fuel line and allowing the engine to run dry of fuel.
q
Use a high quality after run oil in the engine after you have purged the
engine of fuel. Inject the oil into the engine through the carburetor and
through the glow plug hole.
q
Wipe the outside of the engine dry using a soft cloth.
q
Use a fuel filter between the fuel tank and the carburetor.
Rocker
Arm
Valve
Stem
Pushrod
Lock Nut
Adjustment
Screw
Gap