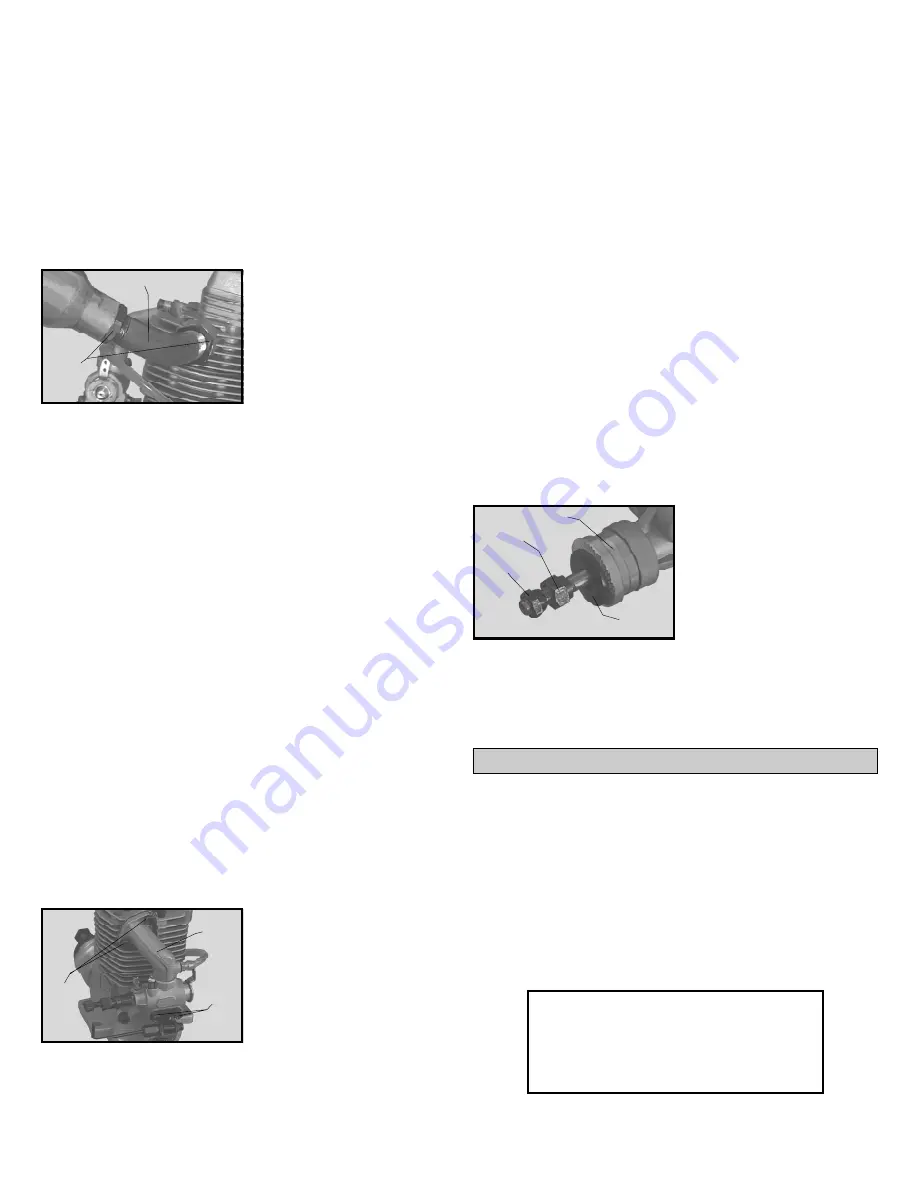
PROPELLER, FUEL & GLOW PLUG
q
Propeller Recommendation
The diameter and pitch of the propeller needed for the XL 1.20RFS will
vary greatly depending on the application the engine is used in. The weight,
drag and the type of model and how you intend to fly it are all factors in
determining the correct size propeller to use. Experimentation will be nec-
essary to find the optimal size propeller for your particular application.
Ideally you want a propeller that the engine will turn in the 8,000 - 9,000
R.P.M. range, yet power the airplane sufficiently. Using a propeller that is
too small will cause the engine to run at too high an R.P.M. Using a pro-
peller that is too large will cause the engine run at too low an R.P.M. and
cause it to lug down too much. In both instances this can lead to premature
engine wear and eventual failure.
Propeller Size Recommendations
q
Engine Bolts and Firewall Requirements
The engine should be mounted to a heavy duty glass filled nylon or a metal
engine mount. Use only high quality steel cap screws and related hard-
ware to mount the engine to the motor mount. The firewall in the airplane
should be aircraft grade 5-ply plywood and be no less than 1/4” thick. The
firewall should also be reinforced to meet the torque and weight of the XL
1.20RFS engine.
q
Muffler and Exhaust Pipe Installation
The muffler threads onto an exhaust pipe, which then threads into the en-
gine head. First thread one cinch nut onto each end of the exhaust pipe.
Thread the muffler on one end. The
muffler should be threaded on at
least 1/4” to prevent vibration from
damaging the threads. Once you
have threaded the muffler onto the
exhaust pipe use an open end
wrench and tighten the cinch nut up
against the muffler. This will pre-
vent the muffler from loosening.
The exhaust pipe is adjustable to better match the scale appearance and
installation of your particular application. Thread the exhaust pipe into the
engine’s cylinder head. The pipe should be threaded in no less than 1/4”
to prevent vibration from damaging the threads. Once you have threaded
the exhaust pipe in place and into the proper position for your application,
use an open end wrench and tighten the cinch nut against the cylinder head.
This will prevent the exhaust pipe from loosening.
q
Tank Size and Orientation to Carburetor
Ideally the stopper in the fuel tank should be even with the high speed
needle valve or just slightly below the high speed needle valve. Most
models will only allow the fuel tank to be mounted higher than the ideal
location. A fuel tank that is positioned higher than the ideal location usu-
ally doesn’t pose any problem except when it is mounted excessively higher
and/or used in conjunction with an inverted mounted engine or during ex-
treme aerobatic flight. If mounting your engine inverted it is advised to
lower the fuel tank so the stopper is slightly below the high speed needle
valve. Doing this will prevent fuel from siphoning into the engine and
flooding it when the fuel tank is full. If you cannot lower the fuel tank far
enough, we suggest lowering it as far as can be allowed in your particular
application.
The size of the fuel tank used should be 12oz. - 16oz. depending on
the model and the length of flights desired. Use of a 16oz. tank will pro-
vide between 15 - 20 minutes of run time at full throttle. Use of a fuel tank
any larger than 16oz. can lead to excessive leaning of the engine during
flight and is not recommended.
q
Carburetor Orientation
In some cases the particular installation of the engine in your model may
make it necessary to change the position of the carburetor. You may want
the throttle arm on the opposite side
than how it comes preinstalled. You
can remove the carburetor and re-
install it in the opposite direction
with no effect on performance. To
remove the carburetor loosen the
two screws holding the intake mani-
fold in place. Next, remove the two
screws holding the choke assembly/
carburetor to the engine. Remove the carburetor by gently pulling it down
off the intake pipe. To reinstall the carburetor reverse the process. We
highly recommend applying machine oil to the o-ring inside
the carburetor mounting base and on the carburetor mounting flange on the
intake pipe. This will prevent the o-ring from being inadvertently cut when
reinstalling the carburetor.
q
Needle Valve Extension
If an extension is required to adjust the high speed needle valve, use a
1.5mm diameter wire of the necessary length. Loosen the set screw in
the side of the needle valve, insert the wire into the end of the needle
valve and tighten the set screw firmly. If the extension is more than 3”
long we recommend supporting the outer end of the extension to prevent
excessive vibration.
q
Propeller Installation
Your engine comes equipped with a main propeller nut and one safety nut.
For your safety, we recommend using both the propeller nut and the safety
nut to secure the propeller in place.
Note: Before installing any propeller it must be properly balanced.
Running an engine, especially of this size, using an improperly balanced
propeller can lead to excessive vibration causing excessive stress and wear
on both the engine and the airframe. Balance the propeller using the recom-
mended method of the propeller manufacturer. Several products are avail-
able to properly balance propellers. Ask your local retailer for more infor-
mation about these items.
Using a 5/16” drill bit or a prop reamer, drill out the hole in the propeller
hub to fit the crankshaft. The crankshaft is 5/16” in diameter. Slide the
propeller onto the crankshaft, up against the thrust washer. Slide the pro-
peller washer up against the propel-
ler. Thread the prop nut onto the
crankshaft. Notice that the prop nut
has a flange on the back of it. This
flange fits inside the washer. Com-
pletely tighten the prop nut to se-
cure the propeller in place. Install
the safety nut onto the crankshaft
then tighten it against the prop nut.
When tightening the prop nut and
safety nut, use the proper size open end wrench. Do not use pliers.
Note: If you are installing a spinner onto your engine the cone of the
spinner must not rub against the propeller. If the spinner cone rubs against
the propeller this could lead to propeller damage and eventual propeller
failure.
15 x 6
15 x 8
15 x 10
16 x 6
16 x 8
Use 15 x 6 for initial break-in procedures
Muffler
Exhaust Pipe
Cinch
Nuts
Loosen
Intake
Pipe
Remove
Thrust Washer
Prop Nut
Safety
Nut
Prop Washer