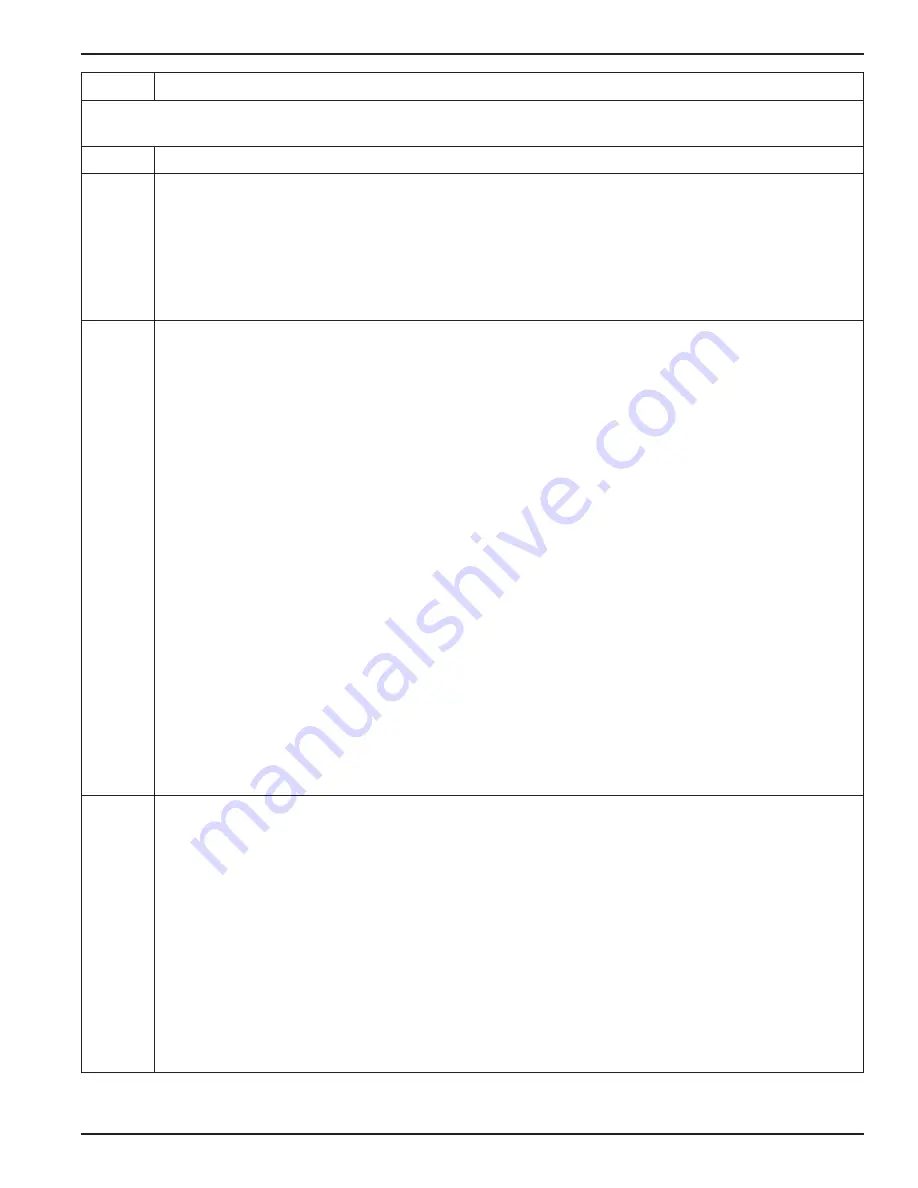
11
51-650 Model 961/962 Echotel SIL Safety Manual -– Loop Version
Step
Proof Test – Echotel Model 961 Loop
Refer to the Model 961 installation and operation manual and the SIL Safety Manual
(note the chart in section 2.5.2.4 of the I & O Manual).
1
Bypass the PLC or take other action to avoid a false trip.
2
Inspect the Unit in detail outside and inside for physical damage or evidence of environmental or
process leaks
a.) Inspect the exterior of the Unit housing. If there is any evidence of physical damage that may
impact the integrity of the housing and the environmental protection, the unit should be repaired
or replaced.
b.) Inspect the interior of the Unit. Any evidence of moisture, from process or environment, is an
indication of housing damage, and the unit should be repaired or replaced.
3
Observe and record the settings of the HI/LOW and 22/3.6 DIP switches, the LED indicators, Loop
Current and Sensor GAP condition (WET or DRY).
If the FAULT LED is lighted, diagnose the fault and repair or replace the unit.
Confirm proper operation of the unit: WET/DRY GAP condition; 8mA LED or 16mA LED is lighted;
Loop current = 8mA ±1mA or 16mA ±1 mA.
a.) Press LOOP TEST push button and confirm change; 8mA >> 16mA or 16mA >> 8mA.
Release the button and unit returns to proper operation.
b.) Change HI/LOW DIP switch position. Confirm both LED & Loop Current change state;
8mA >> 16mA or 16mA >> 8mA. Observe the time delay from change of DIP switch until
LED and Loop current change. Delay is set by Time Delay Pot, so delay may be as long as
15 seconds. Change HI/LOW DIP switch back to original setting and confirm proper operation,
after the delay.
c.) Press FAULT TEST push button and confirm: FAULT LED lights; Loop current
≥
22mA or
≤
3.6mA
based on 22/3.6 switch. Release button.
d.) Change the 22/3.6 DIP switch position. Press FAULT TEST push button and confirm: FAULT
LED lights; Loop current
≥
22mA or
≤
3.6mA as expected. Release push button. Return 22/3.6
switch to original setting
e.) Adjust the Time Delay Pot to maximum delay, fully clock-wise up to 20 turns. Change HI/LOW
DIP switch position and observe the time delay from change of DIP switch until LED and Loop
current change. Confirm delay
≥
10 seconds. Change HI/LOW DIP switch back to original set-
ting and confirm
≥
10 seconds delay. Adjust the Time Delay Pot to minimum delay, fully counter-
clock-wise ~20 turns. Change HI/LOW DIP switch position and observe the time delay. Confirm
delay
≤
1 seconds. Change HI/LOW DIP switch back to original setting and confirm minimum
delay.
4
When possible moving the process level will provide a more complete proof test.
Confirm proper operation of the unit: WET/DRY GAP condition; 8mA LED or 16mA LED is lighted;
Loop current = 8mA ±1mA or 16mA ±1 mA.
a.) Move the process level and confirm the GAP condition has changed. Confirm proper operation
of the unit: WET/DRY GAP condition; 8mA LED or 16mA LED is lighted;
Loop current = 8mA ±1mA or 16mA ±1 mA.
b.) Move the process level and confirm the GAP condition has returned to orginal state. Confirm
proper operation of the unit: WET/DRY GAP condition; 8mA LED or 16mA LED is lighted;
Loop current = 8mA ±1mA or 16mA ±1 mA.
c.) If unit fails the tests of steps 4a or 4b proceed to step 5.
d.) Adjust the Time Delay Pot to the original setting. Use HI/LOW DIP switch (as described in
step 2e) to confirm that delay is returned to original setting.
e.) Proceed to step 6.
continued on next page