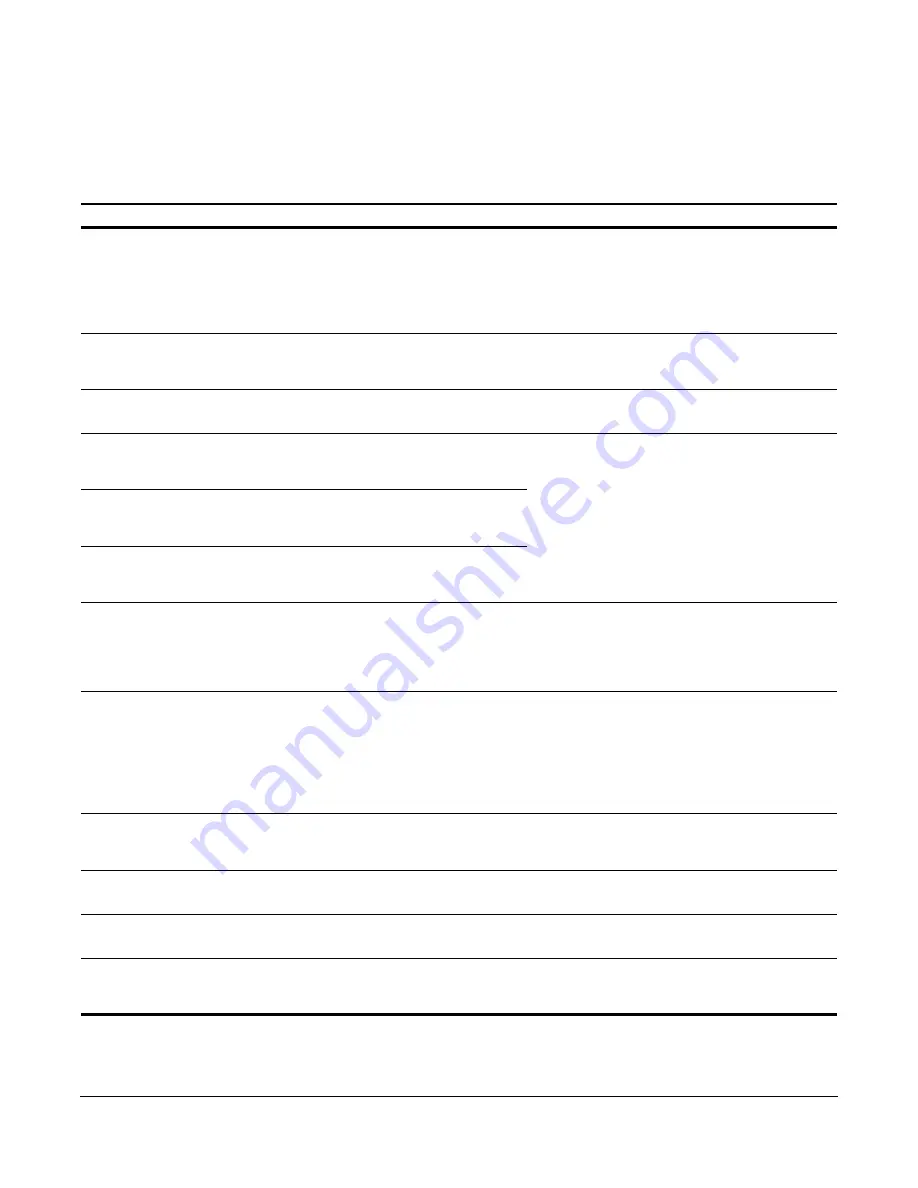
IMPULSE•G+/VG+ Series 4 Technical Manual
November 2022
Page 210
6.3 Auto-Tuning Errors
The following are errors during auto-tuning and corrective actions. If any of the following errors are detected, the
keypad will display the error text and the motor will coast to stop, if running. No fault or alarm output is triggered.
Table 6-5: Error Display and Corrective Actions
Display
Description
Corrective Action
Er-01
Data Invalid
Motor Data Fault.
Motor data input fault for auto-
tuning. Relationship between motor output and
motor rated current fault. Relationship between
input motor rated current and set no-load current
fault (at vector control method and line-to-line
resistance tuning.)
• Check input data.
• Check VFD and motor capacity.
• Check motor rated current and no-load current.
Er-02
Minor Fault
Alarm.
An alarm is detected during auto-tuning.
• Check input data.
• Check wirings.
• Check load.
Er-03
STOP Key
STOP Key Input.
The stop key is pressed during
auto-tuning.
Er-04
Resistance
Line to Line Resistance Fault.
Auto-tuning is not
completed within the expected time. The auto-
tuning is outside the parameter setting.
• Check input data.
• Check motor wiring.
• If a motor and a load are connected, disconnect
the motor from machinery system.
Er-05
No-Load Current
No-load Current Fault.
Auto-tuning is not
completed within the expected time. The auto-
tuning is outside the parameter setting.
Er-08
Rated Slip
Rated Slip Fault.
Auto-tuning is not completed
within the expected time. The auto-tuning is
outside the parameter setting.
Er-09
Acceleration
Acceleration Fault.
The motor did not accelerate
at the expected time.
• Increase B05-01 (acceleration time).
• If C07-01 and C07-02 (torque limit value) are
decreased, increase values.
• If a motor and a load are connected, separate
the motor from the load.
Er-10
PG Direction
Motor Direction Error.
The encoder signal lines
are not properly connected to the VFD; the motor
direction and PG direction are opposite; or the
load pulled the motor in the opposite direction of
the speed reference and the torque exceeded
100%.
• Check and correct wiring to the PG encoder.
• Check the motor speed monitor U01-05 while
manually turning the motor forward. If the sign
displayed is negative, change the setting of
parameter F01-02.
• Uncouple the motor from the load and restart
Auto-Tuning.
Er-11
Motor Speed
Motor Speed Fault (Rotational tuning only).
The motor speed was over 100% at auto-tuning
(flux vector control without PG only).
• Increase B05-01 (acceleration time).
• If a motor and a load are connected, separate
the motor from the load.
Er-12
I-det. Circuit
Current Detection Fault.
Current exceeded the
motor rated current.
• Release brake.
• Check for open motor lead.
Er-13
Leakage L Err
Leakage Inductance Fault.
Auto-tuning did not
finish within the set time.
• Check the T1 parameters.
• Check motor wiring.
End 1*
High V/f Setting
Excess V/f setting (Rotational tuning only).
The torque reference exceeded 100% and no load
current exceeded 70%.
• Check the T1 parameters.
• Disconnect the motor from the load.
Содержание Impulse G+ series 4
Страница 20: ...IMPULSE G VG Series 4 Technical Manual November 2022 Page 20 Figure 2 1 Capacitor Reform Diagrams...
Страница 30: ...IMPULSE G VG Series 4 Technical Manual November 2022 Page 30 Figure 3 1 Typical Connection Diagram...
Страница 53: ...IMPULSE G VG Series 4 Technical Manual November 2022 Page 53 4 3 2 Menu Structure Figure 4 1 Menu Structure...
Страница 243: ...IMPULSE G VG Series 4 Technical Manual November 2022 Page 243 Figure B 5 Figure B 6 Figure B 7...
Страница 246: ...IMPULSE G VG Series 4 Technical Manual November 2022 Page 246 Figure B 8 Figure B 9 Figure B 10 Figure B 11...
Страница 248: ...IMPULSE G VG Series 4 Adjustable Frequency Vector Crane Controls Technical Manual November 2022...