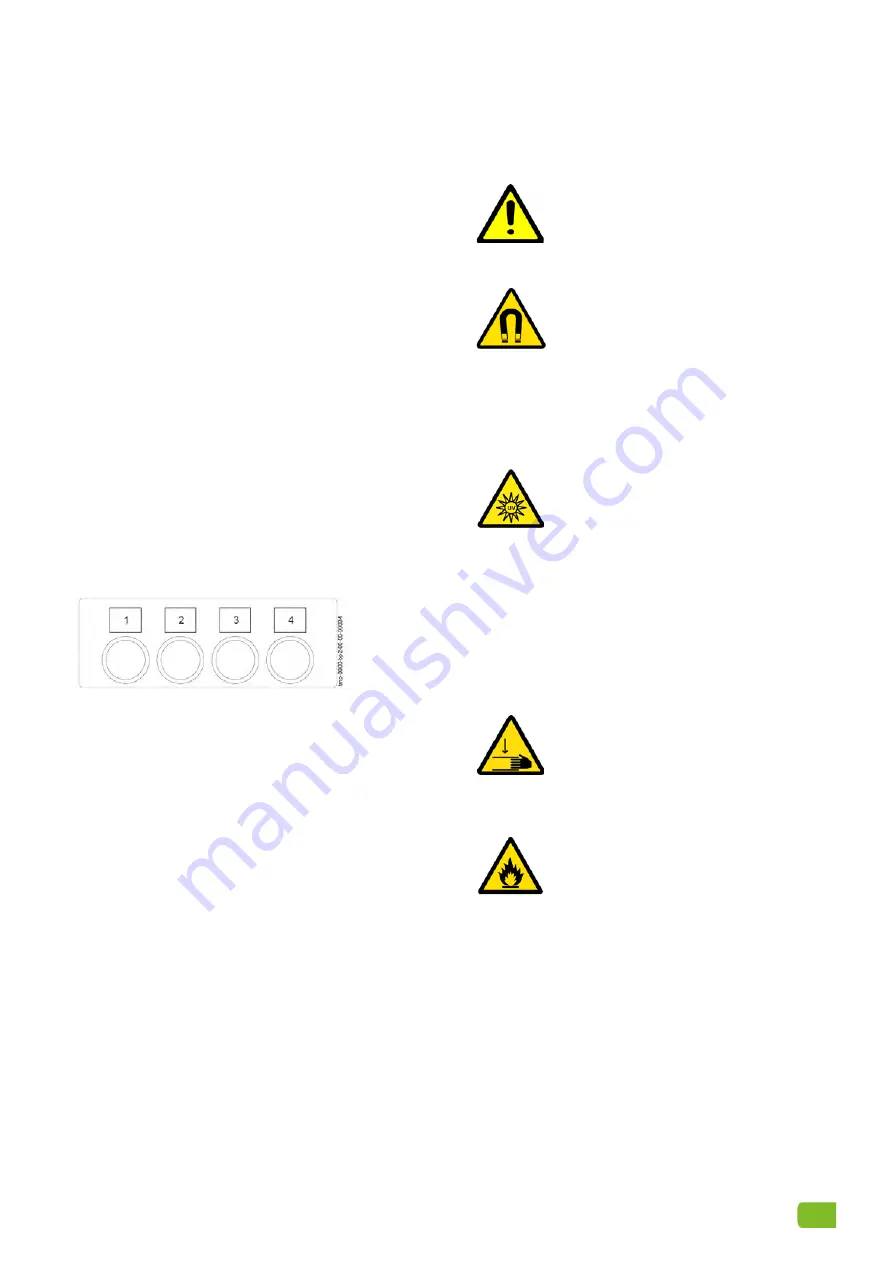
Push-button: Magnetising
Function:
turns on the magnetisation as long as the
button remains pressed.
Prerequisite:
workpiece clamped
Push-button: Demagnetising
Function:
starts demagnetisation
Button pressed:
• In
automatic mode:
demagnetisation is controlled
by PLC.
• In manual mode: the workpiece is magnetised with
the set intensity. For sufficient magnetisation, press
and hold the button for 5 seconds.
Button released:
the magnetising current is controlled
to zero along an e-function.
Prerequisite:
workpiece clamped.
Push-button with indicator light: Clamp (option)
Function of button:
clamps the sleeves
Light on:
workpiece clamped
3.5 RIGHT OPERATING PANEL
1. Push-button:
Rotate workpiece
2. -
3. -
4. -
4. GENERAL SAFETY INFORMATION
4.1 HAZARDS WHEN USING THE MACHINE
WARNING:
This manual must be
kept with the machine and must be
freely accessible for operating and
maintenance personnel at all times.
WARNING:
High magnetic field
strengths during magnetising can
cause damage to health and have
negative effects on medical implants.
• Always comply with the applicable accident
prevention regulations
• Keep a safe distance from the machine during
magnetisation.
WARNING:
Ultraviolet radiation can
damage skin and eyes.
• Never look directly into an UV lamp.
• Avoid skin contact.
• Ensure that only authorised personnel are allowed
within the danger zone.
• Operate UV lamps only if fitted with an undamaged
and properly mounted filter.
• If required, wear eye and skin protection.
CAUTION:
Heavy workpieces can
crush hands. Do not reach between
workpieces and machine components
during loading and unloading. Use
hand protection.
CAUTION:
Fire hazard: test oils are
highly flammable. Only use flame-
retardant test oils with a flash point >
100°C.
When using oily test liquids:
• have suitable fire extinguishers nearby,
• keep magnetising contacts clean at all times,
• observe the instructions provided by the test liquid
manufacturer.
When using the Universal SW, you must be aware of
hazards for:
• the life and limbs of the operator and other personnel
• the machine itself
• other assets
12
Содержание Universal SW Series
Страница 1: ...Operating Manual Universal SW...