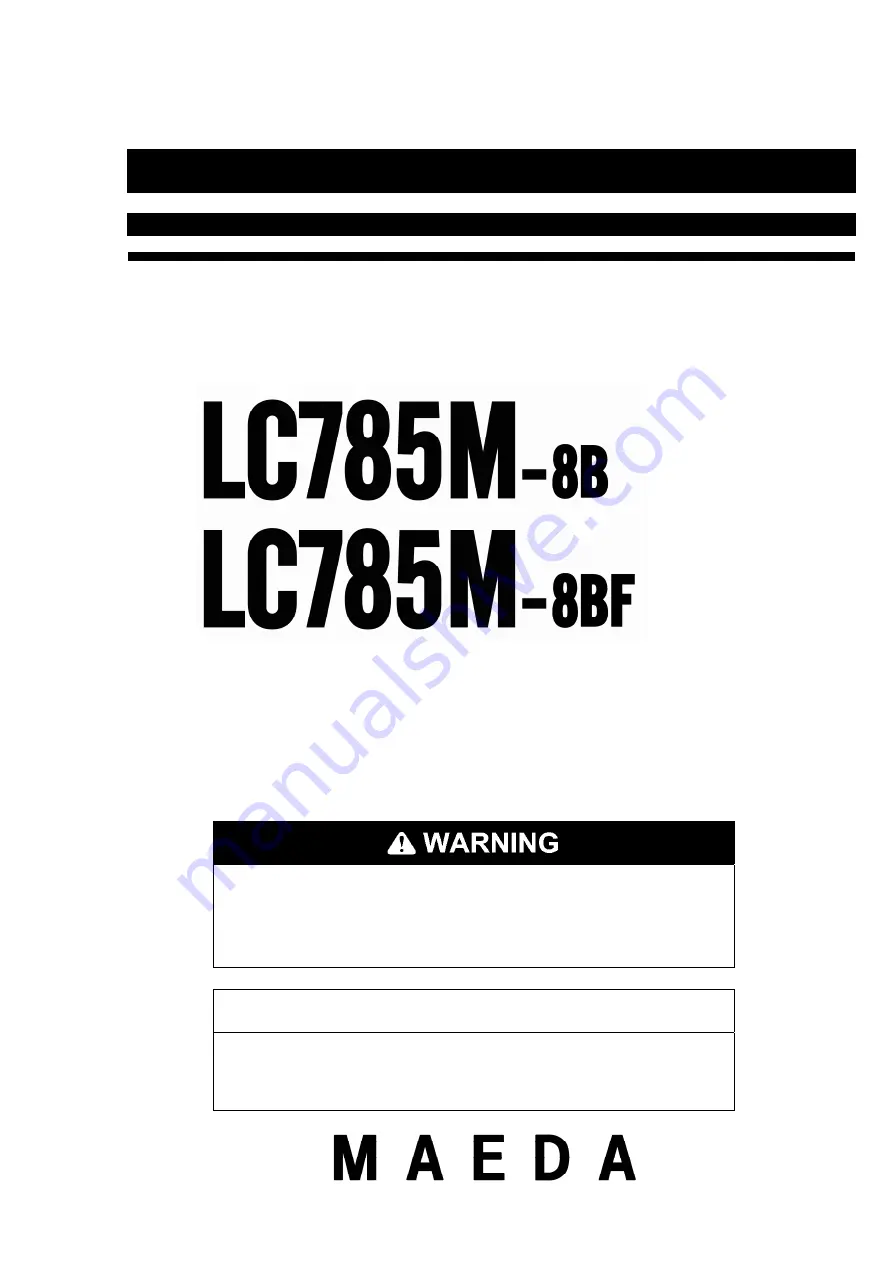
557E-OM1202-00
OPERATION MANUAL
CRAWLER CRANE
Serial No. 32024 and up
Unsafe use of this machine may cause serious injury or death. Operators
must read this manual before operating this machine. This manual should
be kept near the machine for reference and periodically reviewed by all
personnel who will come into contact with it.
NOTICE
MAEDA has Operation Manuals written in some other languages. If a
foreign language manual is necessary, contact your local distributor for
availability.
Содержание LC785M-8B
Страница 2: ......
Страница 21: ...Gauges and meters To be shown at service meter section on machine monitor 1 13 ...
Страница 22: ...1 14 ...
Страница 56: ... SAFETY LABEL LOCATIONS ON CHASSIS 2 34 ...
Страница 57: ... 1 Working range and rated total load chart 557 2221400 2 For your safe operation 556 3367900 2 2 35 ...
Страница 58: ... 3 Moment limiter operation 557 2221500 4 Warning for operation inspection and maintenance 584 3469700 2 36 ...
Страница 64: ... 29 Safety plate 09659 A057B 2 42 30 Warning for hook block 553 4267400 2 places ...
Страница 218: ... Use the horn switch and toot the horn to warn danger to persons nearby when necessary during crane operations 3 154 ...
Страница 310: ...8 Press the button of dust indicator to return the red piston to its original position 4 30 ...
Страница 323: ...4 43 ...
Страница 364: ...2 SPECIFICATION DIMENSIONAL DRAWING 5 4 ...
Страница 368: ...4 WORKING RADIUS AND LIFTING HEIGHT WORKING RADIUS AND LIFTING HEIGHT AT WIRE ROPE 4 FALLS 5 8 ...
Страница 369: ...WORKING RADIUS AND LIFTING HEIGHT AT WIRE ROPE 2 FALLS 5 9 ...
Страница 370: ...WORKING RADIUS AND LIFTING HEIGHT AT WIRE ROPE 1 FALLS 5 10 ...
Страница 375: ...3 WORKING RANGE CHART 6 5 ...
Страница 398: ......
Страница 400: ......
Страница 401: ......