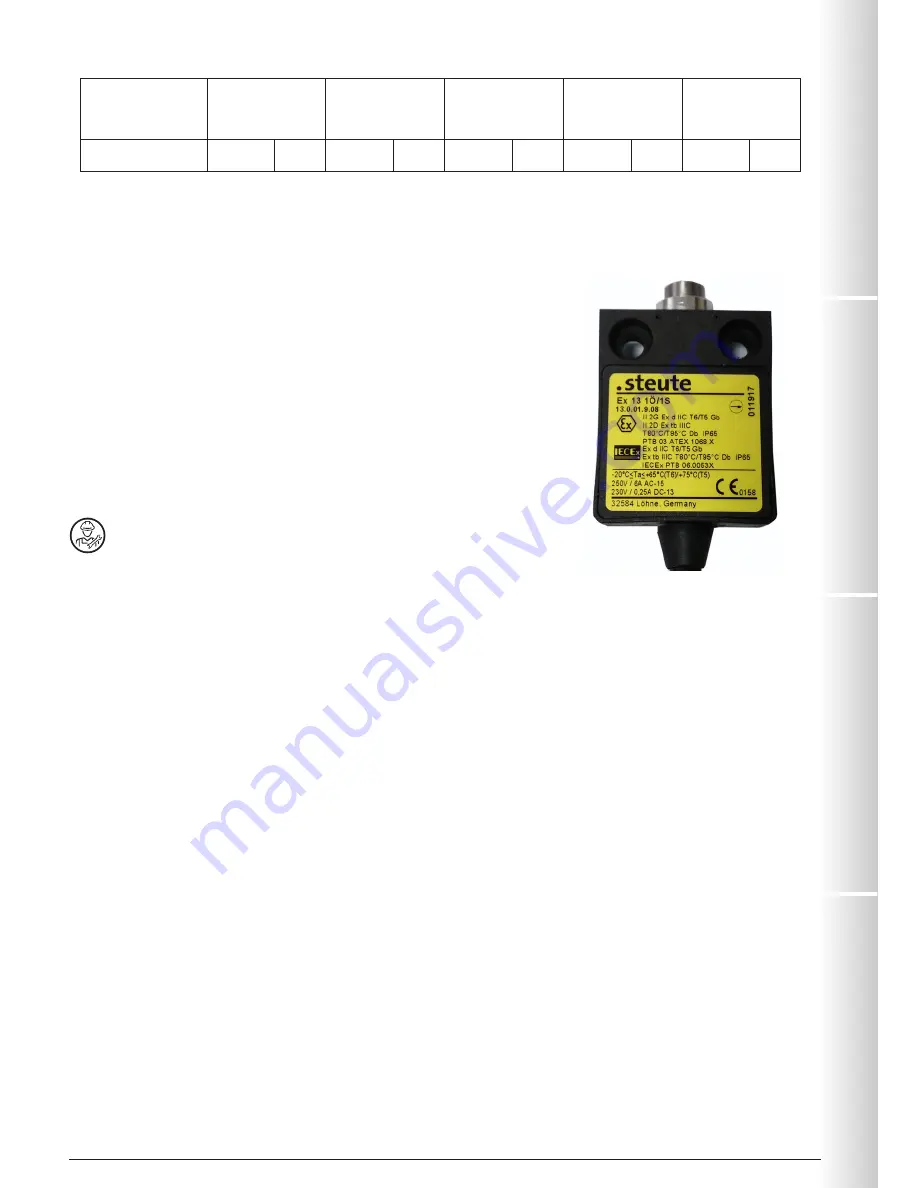
15
IT
EN
FR
ES
M16/RM N.C. EEX
Madas Technical Manual
- 2|2.2b - REV. 0 of 10
th
May 2018
• Tighten the screws gradually, following a “cross” pattern, until the torque (tolerance -15%) indicated in the table below is
reached. Use a calibrated torque wrench to do this;
Screw
M5
M6
M8
M10
M12
Galvanised Stain.
STEEL Galvanised
Stain.
STEEL Galvanised
Stain.
STEEL Galvanised
Stain.
STEEL Galvanised
Stain.
STEEL
Max. torque (N.m)
6
4,5
10
7,5
25
18,5
49,5
37
84,5
63,5
• Check the body/cover seal;
NOTE
: for internal inspections (see fig.1), it is recommended:
• also check the obturator’s (
11
) integrity and, if necessary, replace the rubber seal (
10
);
• replace the seals before reassembling.
7.0 - CPI SWITCH
If the solenoid valve comes with CPI, the position of the micro switch is already
calibrated and set, therefore, for operation you simply need to connect it to the
power supply. If it is supplied separately (as a kit), it must be installed on the
solenoid valve and then calibrated.
In both cases, follow the instructions in 7.1 and 7.2.
7.1 - TECHNICAL DATA and CPI SWITCH WIRING
(see figure on the side)
Refer to the attached technical manual regarding CPI.
7.2 - CPI SWITCH INSTALLATION and CALIBRATION
if the CPI kit is supplied separately, you must proceed as follows to install in
on the solenoid valve:
DN 65 - DN 80 - DN 100 - DN 125 - DN 150
(see fig. 3):
• Loosen the fastening screw (
24
) inside the reset knob (
1
) and remove it;
• In the pin without the knob, insert the eccentric grub screw (
22
) with the larger part of the half moon on the left, and the
new knob supplied with the kit. The knob (
1
) must be inserted with the threaded hole facing up and making said threaded
hole match up with the pin hole. Secure the knob (
1
) by tightening and securing the grub screw (
24
) inside;
• Loosen the 2 screws (
15
) of the upper cover (
25
);
• Secure the upper cover (
25
) to the support bracket (
21
) of the micro switch using the 2 screws (
15
);
• For calibration, change the position of the microswitch from the 2 screws (
28
) and 2 nuts (
20
) so that when the solenoid
valve is closed, the micro switch’s pin (
26
) is pressed;
• Secure the micro switch (
27
) in that position by tightening the 2 nuts (
20
);
• The kit is now installed. Reset and close the solenoid valve (by cutting off the power) to make sure the microswitch is signalling
correctly. Repeat the operation 2-3 times;
• Position the cover of the knob (
13
) and secure it in that position with the screw (
23
).
DN 200 - DN 250 - DN 300
(see fig. 4):
• Use the knob (
1
), to insert the eccentric ring nut (
22
) with the larger part of the half moon on the left and the fastening
grub screw holes facing up;
• Secure the eccentric ring nut (
22
) with the 2 grub screws (
29
);
• Loosen the 2 screws (
15
) of the upper cover (
25
);
• Secure the support bracket (
21
) of the micro switch to the upper cover, using the screws (
15
);
• For calibration, change the position of the microswitch (
27
) from the 2 screws (
28
) and 2 nuts (
20
) so that when the
solenoid valve is closed, the micro switch’s pin (
26
) is pressed;
• Secure the micro switch (
27
) in that position by tightening the 2 nuts (
20
);
• The kit is now installed. Reset and close the solenoid valve (by cutting off the power) 2-3 times to make sure the microswitch
is signalling correctly;
• Position the cover of the knob (
13
) and secure it in that position with the screw (
23
).