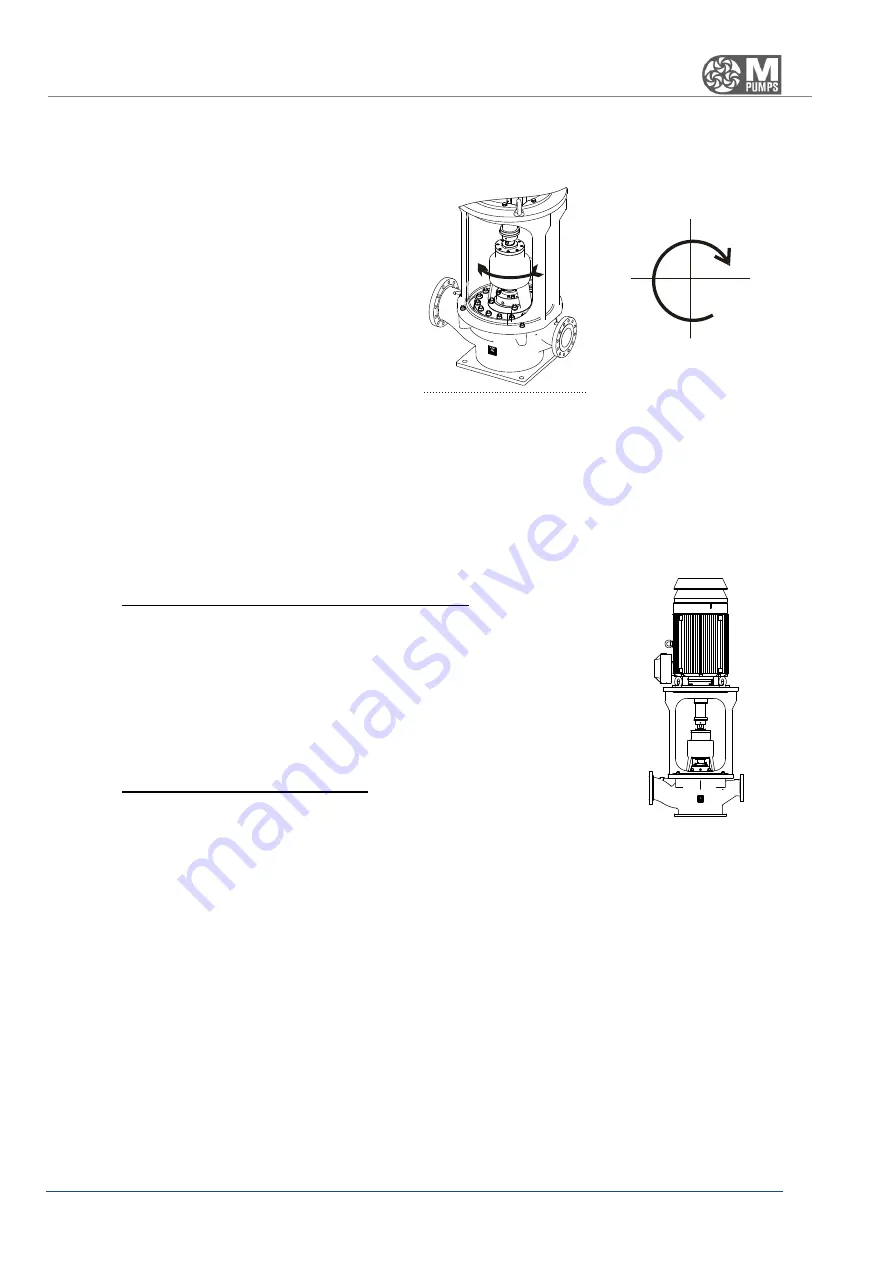
Doc. ISM0076_MANUALE_CN SEAL-MV_ENG_REV04.DOCX
Pag. 21/49
The
M PUMPS PROCESS
series CN SEAL-MV
are
not reversible
so the rotation cannot be reversed.
The proper direction is
clockwise.
If you put in front of the pump casing, an arrow
indicates the correct direction of rotation; to reverse
the direction of rotation may cause damages to the
pump.
To control the direction of rotation, give and
immediately remove voltage, then observe the
direction of rotation.
ROTATION SENSE:
Make sure that rotating parts, such as flexible coupling or other related organs, are always protected when the
pump is running.
Operators using the pump must have read this manual in the sections committed to the functioning, use and
maintenance, as well as being qualified to fully understand the features and to be able to identify the problems of
the pump.
By carrying out the functions mentioned in the previous section and all controls listed in APPENDIX B and in the
maintenance register, the pump is ready for use.
14.6.
Self-priming pumps and non-self-priming pumps
CN SEAL-MV pumps are not self-priming: Make sure that the pump is
always filled with the pumping liquid to avoid any damage. Use a back flow
check valve to stop reverse flow when operating with suction lift, dry run
should be avoided.
14.7.
Coupling of the pump to the motor
If pump and motor have to be coupled, respect the following sequences to
proceed with the installation:
Fit the two elastic coupling halves on the pump and the motor.