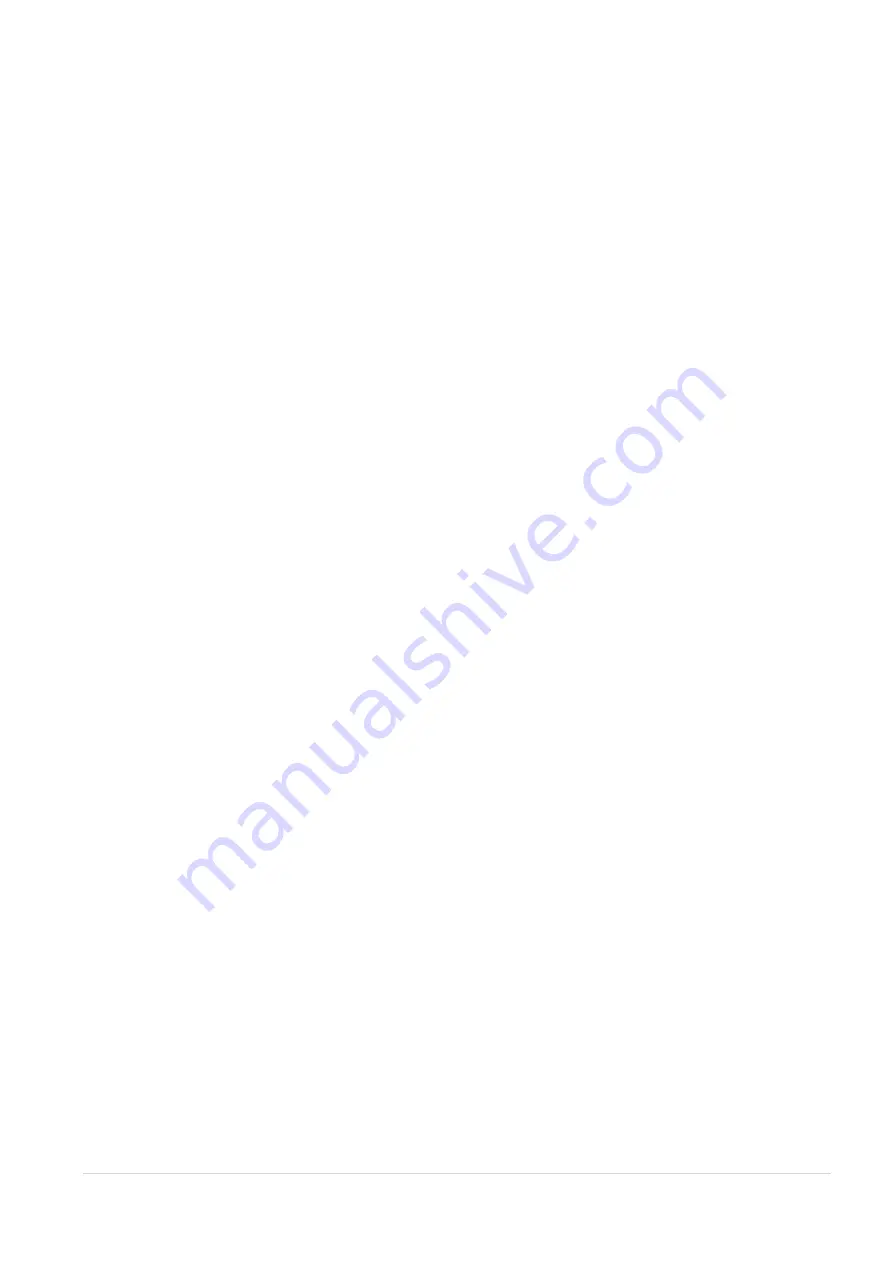
Chapter 4: Product description
_________________________________________________________________________________________
10 | Installation, Operation & Maintenance Instructions EASYCHLORGEN
4. Product description
4.1 Scope of delivery
Please compare the delivery note with the scope of delivery:
•
EASYCHLORGEN electrolyser cabinet
•
EASYCHLORGEN DC power supply cabinet
•
Insulated DC power busbars (2m), clamps, self-
amalgamating tape.
•
Brine break tank with float valve assy
•
Duplex softening system
•
Operating Instructions
•
Selectable Options
: Brine saturator tank, external
product tank, dosing pump/s & accessories.
4.2 Design and function
4.2.1 Function description
EASYCHLORGEN is a fully automatic system for the
preparation of dilute sodium hypochlorite solution containing
0.6% (+/-0.1%) Cl
2,
from the raw materials of salt, softened
water and electrical energy.
Sodium hypochlorite solution (the
product) is prepared by a simple, once through batch process,
initiated by the level switch within the Product Tank. Refer to
the diagram 4.2.3 in conjunction with the description below.
When the product level in the degassing tank (14), or optionally
the external product tank, falls below the start/stop fill level
switch
(11) the water solenoid valve (4) and brine solenoid
valve (3) are energised simultaneously, allowing softened
water to flow through the pressure reducing valve (7) and
through the volumetric flow meter (6). The water stream flows
through the brine inductor (2) to create a vacuum which draws
in a set amount of brine from the external brine saturator tank.
Once the predetermined quantity of brine is drawn, the water
and brine solenoid valves (4 & 3) are closed, whilst the water
dilution valve (5) is opened to allow a predetermined quantity of
dilution water to be delivered directly to the electrolyser
vessel/s, before closing. The resultant diluted brine solution
passes through the electrolyser/s (13). At the same time, d.c.
voltage is applied across the electrolyser cells where the
diluted brine solution completes the electrical path and allows
an electric current to flow between the cell plates. The
generated product is delivered to the degassing tank (14)
before transfer to an external product tank through the product
outlet connection (16). When the product reaches the start/stop
fill level (11) in the product/degassing tank, or, the start/stop
level switch in the external product tank, the generating
process is stopped. The process is restarted after a
predetermined time delay period has elapsed, initiated when
the liquid level in the product/degassing tank falls below the
start/stop fill level (11). The process can also be re-started and
stopped manually by pressing and holding the ‘scroll up’ arrow
key on the control panel keypad (1) for 3 seconds.
Hot climates:
In hot climates where water supply temperatures
may exceed 20
°
C, an external water chiller (supplied by
others) should be installed on the incoming water supply. The
water chiller must be correctly sized according to the liquid
output capacity of the model (refer to 5.1.1), the ambient air
temperature and the desired water temperature differential.
On 4250 & 8500 models the temperature of the generated
product is monitored by a PT100 sensor located close to the
degassing tank inlet (12); the reading can be viewed on the
EASYCHLORGEN control panel by using the ‘scroll’ keys. A
high temperature alarm set-point (adjusted in the control panel
Engineering menu) is provided to shut down production in the
event of abnormal temperature conditions.
Whilst the unit is generating sodium hypochlorite product,
hydrogen gas is produced as a by-product. Hydrogen gas is
diluted as it enters the degassing tank with a continuous flow of
fresh air from a centrifugal ventilation fan (9) and is vented
safely to atmosphere via ducting connected to the ventilation
outlet (15) to an external exhaust point (atmosphere). The
system is designed so that there are no external areas where
hydrogen levels can reach the LEL (lower explosive limit). An
air-flow sensor (10) is provided to shut down production in the
event the air flow fails to remain within normal operating
parameters.
A text display on the control panel (1) will advise of the reason
for the fault and initiate a volt-free contact which can be used
for
connection of a remote alarm device.