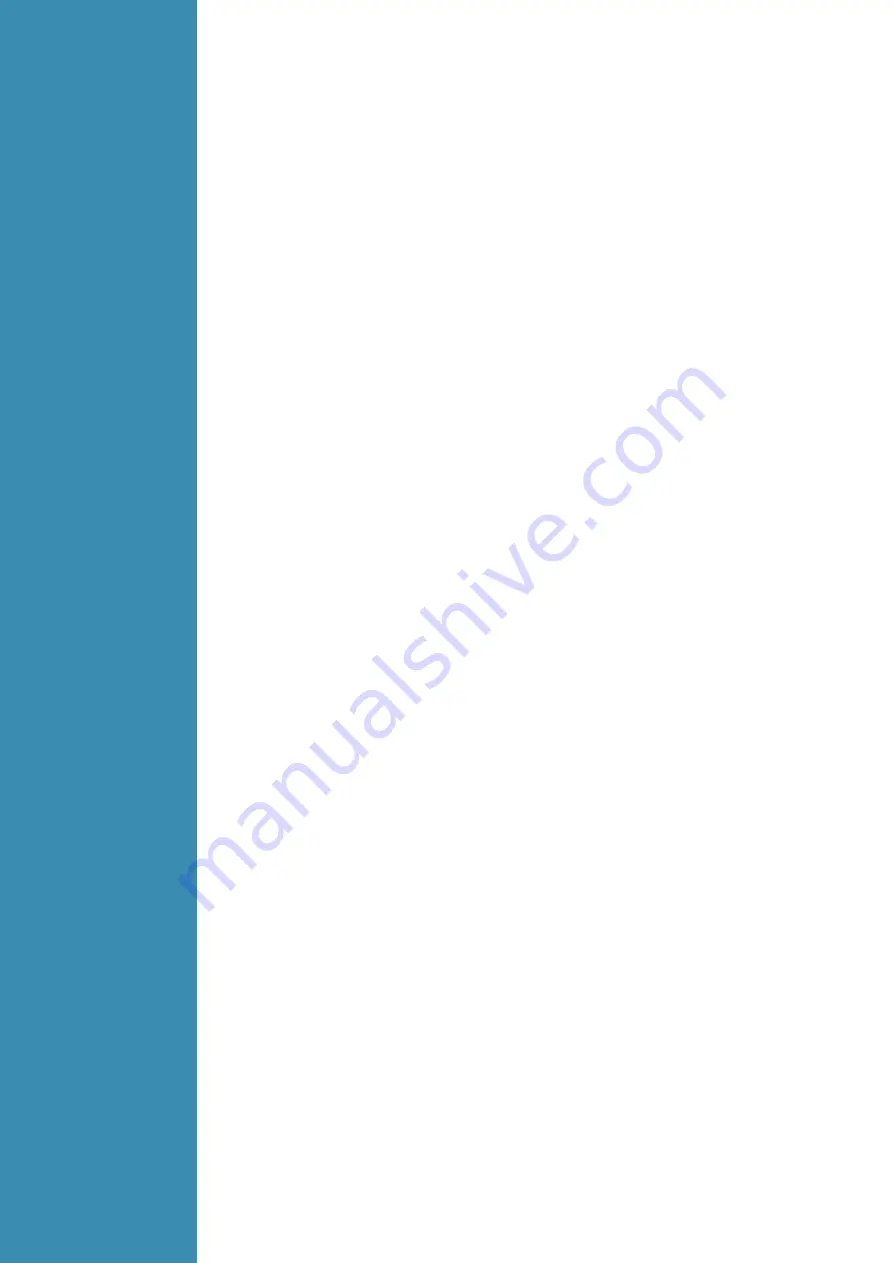
(1) According to the above method to install is correct, turn the power switch to
the “ON” position, the power LED light should illuminate, the fan comes on, the
device work properly.
(2) Set the welding mode to ‘Lift TIG’ or ‘HF TIG’.
(3) If a water cooled torch and water cooler is used, check the water cooler has
sufficient coolant level and all connections are firmly secured. Set the water/air
setting button (14) to ‘water (16)’. The water cooler should now start operating.
If using an air cooled torch, set the button (14) to ‘air’ setting (15).
(4) Set the welding parameters as required using the parameters control knob
(following the instructions in the previous section).
(5) The tungsten must be ground to a blunt point in order to achieve optimum
welding results.
3.4.2
Operation
for TIG
Welding
Switch the ON/OFF Switch (located on the rear panel) to OFF.
(1) Connect the earht lead to “+”, tighten clockwise. Connect the earth clamp to
the work piece. Contact with the work piece must be firm contact with clean
bare metal, with no corrosion, paint or scale at the contact point.
(2) Connect the TIG torch cable to “-”, tighten clockwise.
(3) Connect TIG torch gas connection to the TIG gas outlet and TIG torch remote
plug to remote socket, ensuring all connections are tight.
(4) If using a water cooled torch, connect the water cooling lines from the TIG
torch to the front of the water cooler, ensuring the red and blue return and
supply lines match the connectors.
(5) If using a water cooled torch, connect the water cooler interface cable from
the rear of the power source to the rear of the water cooler.
(6) Connect the gas regulator to the gas cylinder and connect the gas line to the
gas regulator.
(7) Connect the gas line to the machine inlet gas connector via the quick push
lok connector located on the rear panel.
Check for Leaks!
(8) Open gas cylinder valve and adjust regulator, flow should be between
5-10 l/min depending on application. Re-check regulator flow pressure with
torch valve open as static gas flow setting may drop once gas is flowing.
(9) Each machine is equipped with a power cable should be based on the input
voltage welding power cable connected to the appropiate position, not to
pick the wrong voltage.
NOTE:
Secure the gas cylinder in an upright position by chaining them to a stationary
support to prevent falling or tipping.
Содержание Grand Tig 200
Страница 31: ...4 4 Electrical schematic drawing...