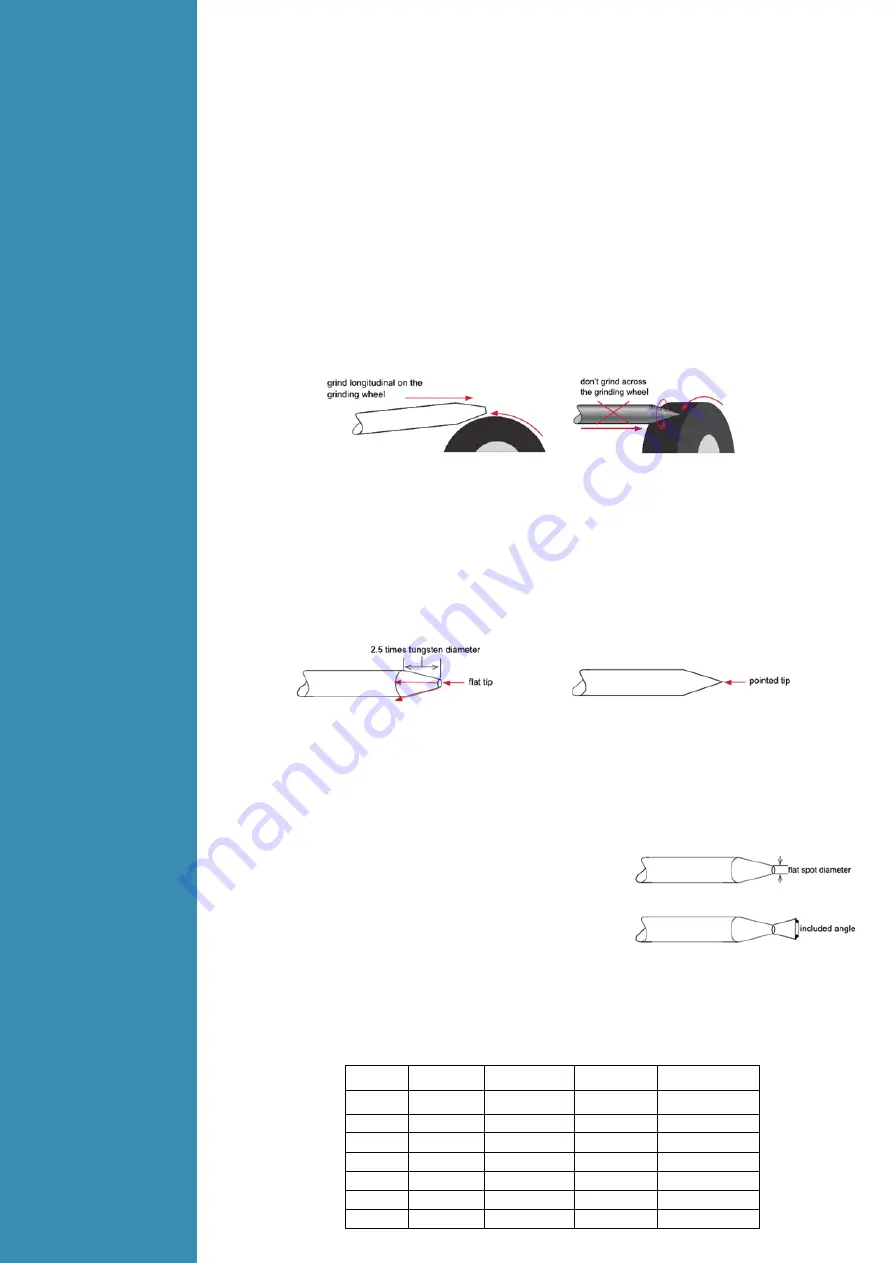
It is necessary in many situations with TIG welding to add a filler wire into the
weld pool to build up weld reinforcement and create a strong weld. Once
the arc is started the torch tungsten is held in place until a weld pool is
created, a circular movement of the tungsten will assist is creating a weld
pool of the desired size. Once the weld pool is established tilt the torch at
about a 75° angle and move smoothly and evenly along the joint. The filler
metal is introduced to the leading edge of the weld pool. The filler wire is
usually held at about a 15° angle and fed into the leading edge of the
molten pool, the arc will melt the filler wire into the weld pool as the torch is moved forward.
Also a dabbing technique can be used to control the amount of filler wire added, the wire is fed into
the molten pool and retracted in a repeating sequence as the torch is moved slowly and evenly
forward. It is important during the welding to keep the molten end of the filler wire inside the gas shield
as this protects the end of the wire from being oxidised and contaminating the weld pool.
3.4.5
Electrodes
Tungsten Preparation
Always use DIAMOND wheels when grinding and cutting. While tungsten is a very hard material, the
surface of a diamond wheel is harder, and this makes for smooth grinding. Grinding without diamond
wheels, such as aluminium oxide wheels, can lead to jagged edges, imperfections, or poor surface
finishes not visible to the eye that will contribute to weld inconsistency and weld defects.
Always ensure to grind the tungsten in a longitudinal direction on the grinding wheel. Tungsten
electrodes are manufactured with the molecular structure of the grain running lengthwise and thus
grinding crosswise is “grinding against the grain.” If electrodes are ground crosswise, the electrons have
to jump across the grinding marks and the arc can start before the tip and wander.
Grinding longitudinally with the grain, the electrons flow steadily and easily to the end of the tungsten
tip. The arc starts straight and remains narrow, concentrated, and stable.
Electrode Tip/Flat
The shape of the tungsten electrode tip is an important process variable in precision arc welding. A
good selection of tip/flat size will balance the need for several advantages. The bigger the flat, the
more likely arc wander will occur and the more difficult it will be to arc start. However, increasing the
flat to the maximum level that still allows arc start and eliminates arc wonder will improve the weld
penetration and increase the electrode life. Some welders still grind electrodes to a sharp point, which
makes arc starting easier. However, they risk decreased welding performance from melting at the tip
and the possibility of the point falling off into the weld pool.
Electrode Included Angle/Taper
DC Welding Tungsten electrodes for DC welding should be ground longitudinally and concentrically
with diamond wheels to a specific included angle in conjunction with the tip/flat preparation. Different
angles produce different arc shapes and offer different weld penetration capabilities. In general,
blunter electrodes that have a larger included angle provide the following benefits
:
• Last Longer
• Have better weld penetration
• Have a narrower arc shape
• Can handle more amperage without eroding.
Sharper electrodes with smaller included angle provide:
• Offer less arc weld
• Have a wider arc
• Have a more consistent arc
The included angle determines weld bead shape and size. Generally, as the included angle
increases, penetration increases and bead width decreases.
Tungsten
Diameter
Diameter at the
Tip - mm
Constant Included
Angle - Degrees
Current Range
Amps
Current Range
Pulsed Amps
1.0mm
.250
20
05 - 30
05 - 60
1.6mm
.500
25
08 - 50
05 - 100
1.6mm
.800
30
10 - 70
10 - 140
2.4mm
.800
35
12 - 90
12 - 180
2.4mm
1.100
45
15 - 150
15 - 250
3.2mm
1.100
60
20 - 200
20 - 300
3.2mm
1.500
90
25 - 250
25 - 350
Tungsten Electrode Preparation
Содержание GRAND TIG 200 DC
Страница 19: ...4 4 Electrical schematic drawing...