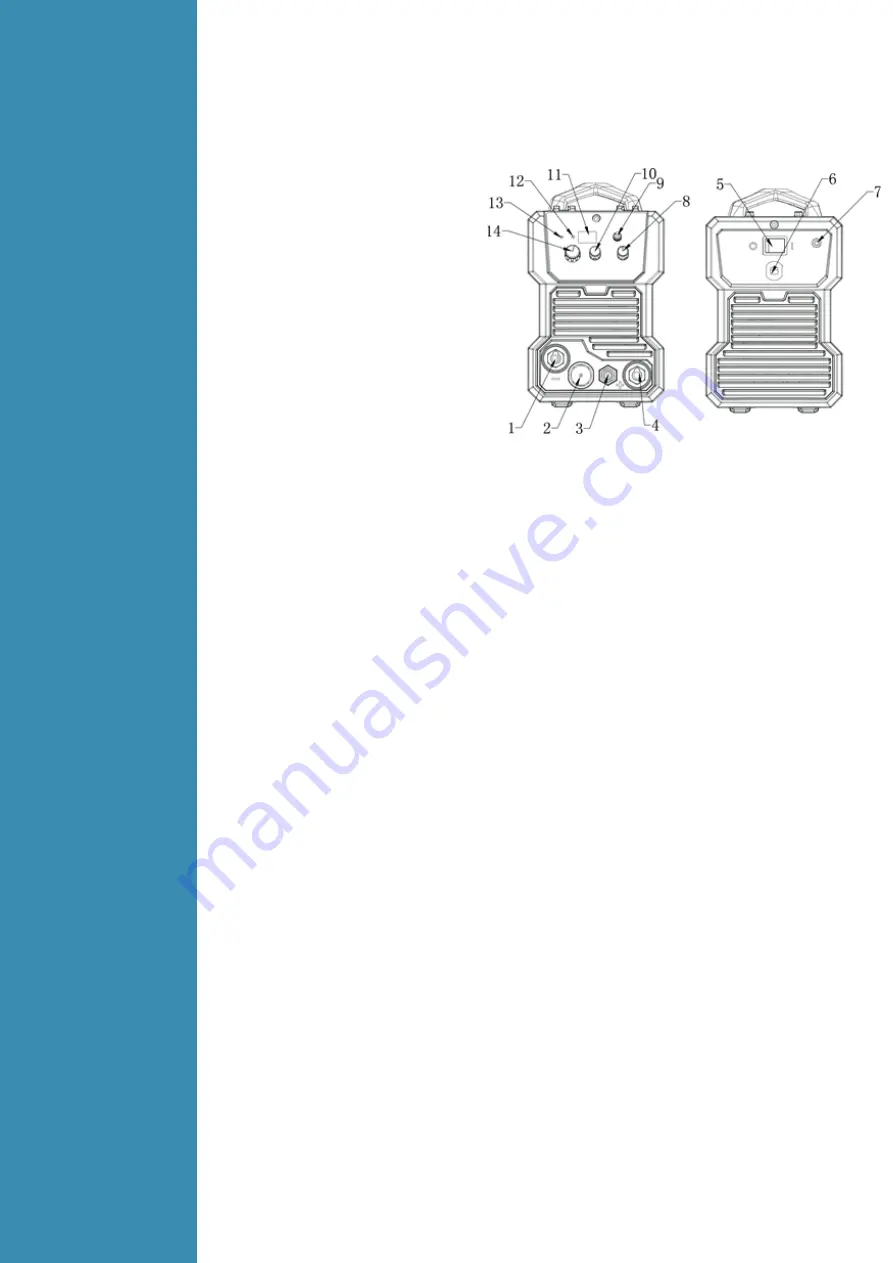
3
Installation
&
Operation
3.1
Layout for
the front
and rear
panel
(
1
)
“-” Output terminal.
(
2
)
TIG torch remote connection socket.
(
3
)
TIG torch gas connector.
(
4
)
“+” Output terminal.
(
5
)
Power switch: control the power
Supply on and off.
(
6
)
Input power cable.
(
7
)
Inlet gas connector.
(
8
)
TIG post gas flow control knob.*
(
9
)
Welding output mode switch:
Sets power source in TIG 2T,
TIG 4T or MMA mode. *
(
10
)
Down slope control knob. *
(
11
)
Digital current display meter.
(
12
)
Alarm light. *
(
13
)
Power light: Lights when input power
connected and machine switched on.
(
14
)
Welding current control knob.
*Denotes more detailed explanation of function to follow.
Further Controls Explained
Post Flow control knob
Controls the period of time the shielding gas continues to flow for after the arc is stopped. This protects
the weld area and torch tungsten from contamination while it is still hot enough to react with
atmospheric gases, after the weld is finished. Post flow time(0-7S) adjust by turning the knob when
TIG welding.
Down slope control knob
When the trigger is released, the welding current will reduce gradually over the time selected down
to 0. This allows the operator to complete the weld without leaving a ‘crater’ at the end of the
weld pool. Down slope time(0-10S) adjust by turning the knob when TIG welding.
TIG 2T/4T
In 2T mode the trigger is pulled and held on to activate the welding circuit, when the trigger is
released, the welding circuit stops. 4T is known as ‘latching’ mode. The trigger is pulled once and
released to activate the welding circuit, pulled and released again to stops the welding circuit. This
function is useful to longer welds as the trigger is not required to be held on continuously.
Alarm Indicator
Lights when over voltage, over current or electrical overheating (due to exceeding duty cycle) is
+detected and protection is activated. When protection is activated, welding output will be disabled
until the safety system senses the overload has reduced sufficiently and indicator lamp goes out. May
also trigger if machine experiences an internal power circuit failure.
The TIG series of welding machines is designed to operate on a 230V AC power supply.
When the power supply voltage is over the safe work voltage, there are over voltage and under
voltage protection inside the welder, the alarm light will on, at the same time, the current output will be
cut off.
If the power supply voltage continually goes beyond the safe work voltage range, it will shorten the
welder life-span. The below measures can be used:
-
Change the power supply input net. Such as, connect the welder with the stable power supply
voltage of distributor;
-
Induce the machines using power supply in the same time;
-
Set the voltage stabilization device in the front of power cable input.
3.2
Power
supply
input
Connection
Содержание GRAND TIG 200 DC
Страница 19: ...4 4 Electrical schematic drawing...