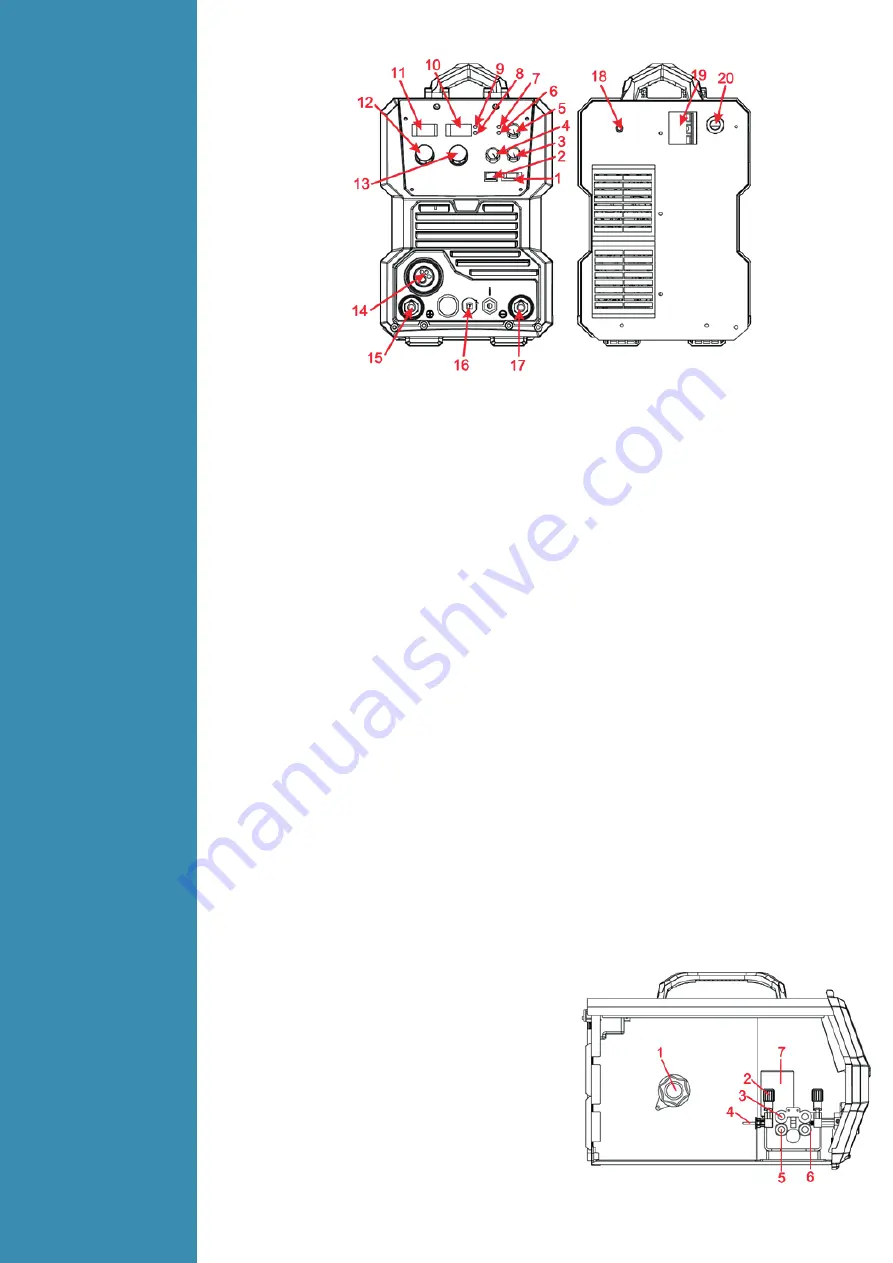
4
Operation
4.1
Layout for
the front
and rear
panel
1. Manual inch wire switch & test gas switch: left for manual inch wire and right for test gas.
2. Choose welding mode switch: left for 2T welding mode and right for 4T welding mode.
3. Burn back knob
4. Wave control knob: Controls arc characteristics, Determines the rate at which the amperage rises
when a short circuit is produced.
5. Soft arc knob: to select the speed of the wire at the start, before arc igniction.
6. Alarm Led: When the welder is over voltage, less voltage, over current or over heated, the alarm
pilot lamp will be on.
7. Power Led: Power led is lighted when switch on the machine.
8. Current LED: When the current LED is on, it display the actual output welding current.
9. Wire speed LED: You can use current setting knob to set the wire speed when the wire speed
LED is on.
10. Current display: Welding Current display when machine is working, Set current display before
welding. Unit
:
A.
11. Voltage display: Welding voltage display when machine is working, Set voltage display when MIG
mode before welding. Unit
:
V.
12. Welding volt knob: Set the welding volt
13. Welding current/wire speed knob: Set the welding current/wire speed.
14. MIG GUN Connect.
15. Output positive
16. MIG Torch Polarity Change Power Connection: Connect to”+”, the MIG gun connecter will be
“+”, connect to “-”, the MIG gun connecter will be “-”;
17. Output negative
18. Shield gas input joint: To connect one head of the gas hose while the other head of which is
connected to argon gas cylinder.
19. On/off switch: Control the power supply on and off.
20. Power source input cable: To connect power source.
4.2
Wire
Feeder of
welding
machine
1. Spool holder.
2. Wire feed tension adjustment (2x).
3. Wire feed tension arm (2x).
4. Wire feeder inlet guide.
5. Drive roller retainer (2x).
6. Wire drive roller (2x).
7. Wire feed motor.