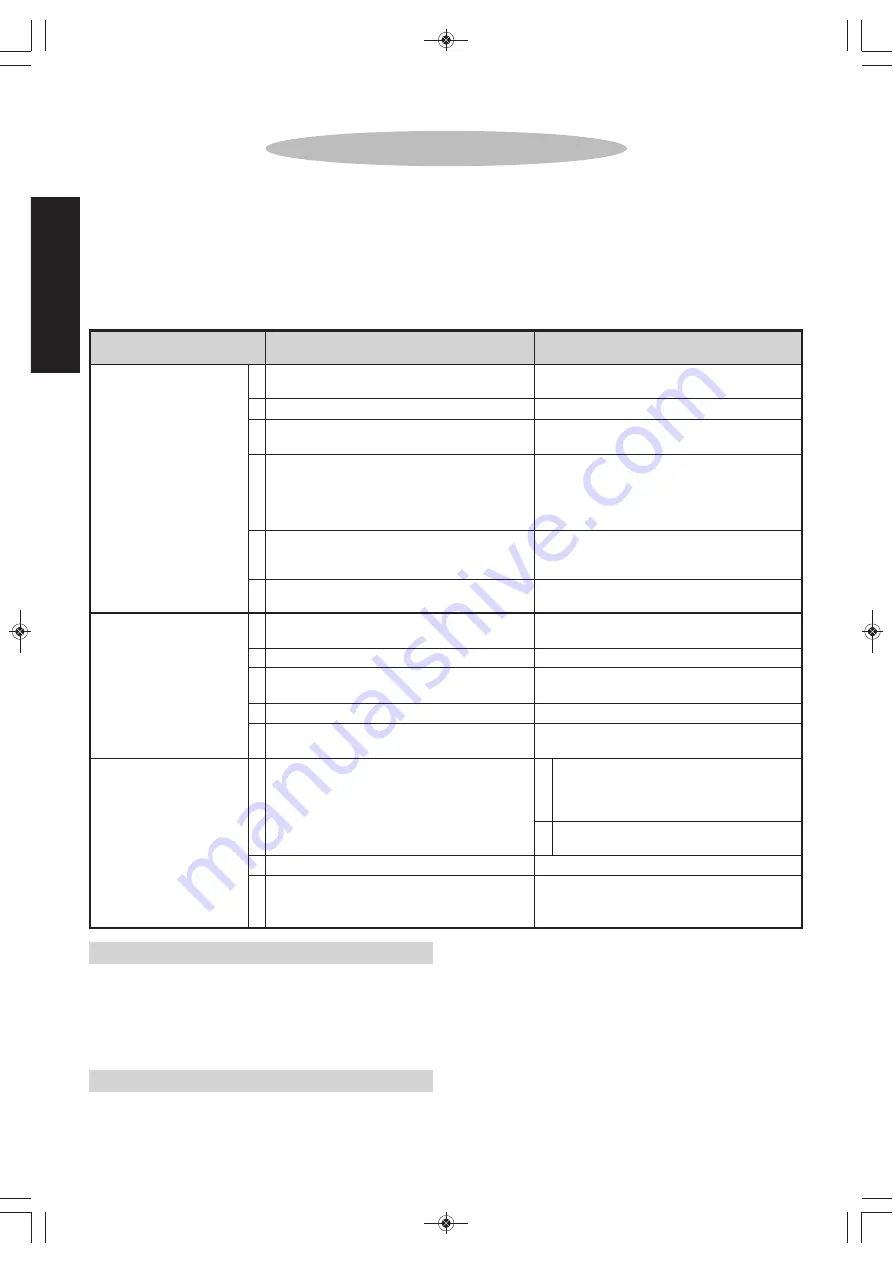
TROUBLESHOOTING
If a problem occurs, check the following.
If the problem persists after checking the items in the table below, contact your nearest “LOBSTER”
dealer or direct to us.
In making any enquiries about this product or requests for repair work, first check the
troubleshooting items below, and then make a note of the model number, the usage conditions and
the trouble symptoms in as much detail as possible. If you can provide this kind of information, it
will contribute to reducing the amount of time required for delivery or repairs to be completed.
The rivet does not go
in, or the cut mandrel
does not come out
after riveting.
Number of switch
operations increases
before riveting is
complete.
Piston does not
operate, or returns
very slowly, or
operation is not
smooth.
Incorrect combination of replacement parts
being used.
Nosepiece or frame head is loose.
Jaw case is incorrectly assembled.
Contact surfaces between the jaws and the
jaw case head are not smooth.
The inside of the cylinder is dirty so that the
air piston cannot return to its proper position.
Oil filling was not performed correctly, so that
there is excess hydraulic oil inside the tool.
The rivet length is not correct for the
workpiece thickness.
Compressor air pressure is incorrect.
Jaw case is incorrectly assembled.
Jaws are worn.
Insufficient hydraulic oil, causing a shorter
stroke.
Spool is not moving properly.
Air outlet hole muffler is blocked.
The inside of the cylinder is dirty so that the
air piston cannot return to its proper position.
1
2
3
4
5
6
1
2
3
4
5
1
2
3
Replace with the correct part which matches
the rivet size. (Refer to page 7.)
Use a spanner or similar to tighten securely.
Check the jaw case setting position. (Refer to
pages 9 and 10.)
Clean the jaws and inside the jaw case head,
and apply “LOBSTER” brand jaw lube (or
spray-type lubricating oil or the accessory
hydraulic oil) to the backs of the jaws. (Refer
to pages 9 and 10.)
Clean inside the cylinder, and apply grease
inside the cylinder and to the O-ring. (Refer to
pages 11 and 12.)
Loosen the bleed plug to allow the excess
hydraulic oil to drain out. (Refer to page 12.)
Use rivets which match the workpiece
thickness.
Check the air pressure.
Check the jaw case setting position. (Refer to
page 10.)
Replace the jaws. (Refer to page 9.)
Add hydraulic oil. (Refer to page 14.)
Remove the rear part of changeplug (refer
to page 13) and push the spool 2~3mm
with a plastic (soft) stick. In case of no
improvement, take the
II
measure.
Clean the spool and apply grease to the O-
rings. (Refer to page 13.)
Replace the muffler. (Refer to pages 11 and 12.)
Clean inside the cylinder, and apply grease
inside the cylinder and to the O-ring. (Refer to
pages 11 and 12.)
Trouble
Cause
Countermeasure
“LOBSTER” brand Hydraulic Oil is supplied in a plastic filler
bottle with the tool, and can also be obtained from your “Lobster”
dealer or agent in your town. If this is not possible, a good quality
mineral oil with the following properties should also be used.
Viscosity ISO
: VG46
Viscosity Index
: 113
Viscosity at 40°C
: 46 c.s.t.
Viscosity at 100°C : 7.06 c.s.t.
Flash Point
: 228
RECOMMENDED OILS are:
Shell Tellus No. 46
Esso Teresso No. 46
Mobil D.T.E. 25 Oil (Medium)
I
II
15
英語/E
N
G
L
ISH
ULTRA JAWS (AR2000M
(A)
/AR2000H
(A)
)
The AR2000M
(A)
and AR2000H
(A)
use ultra jaws which
have greater durability. Be sure to specify “Ultra jaws
M” (AR2000M
(A)
) or “Ultra jaws H” (AR2000H
(A)
) as
replacement parts for these models.
HYDRAULIC OIL REQUIREMENTS
Use only clean hydraulic oil, as the viscosity of the oil used will
affect tool performance.
AR-2000S-M-H(A)取扱(GB):AR-2000S̲M-H(A)取扱(GB) 14/08/27 13:55 ページ 15