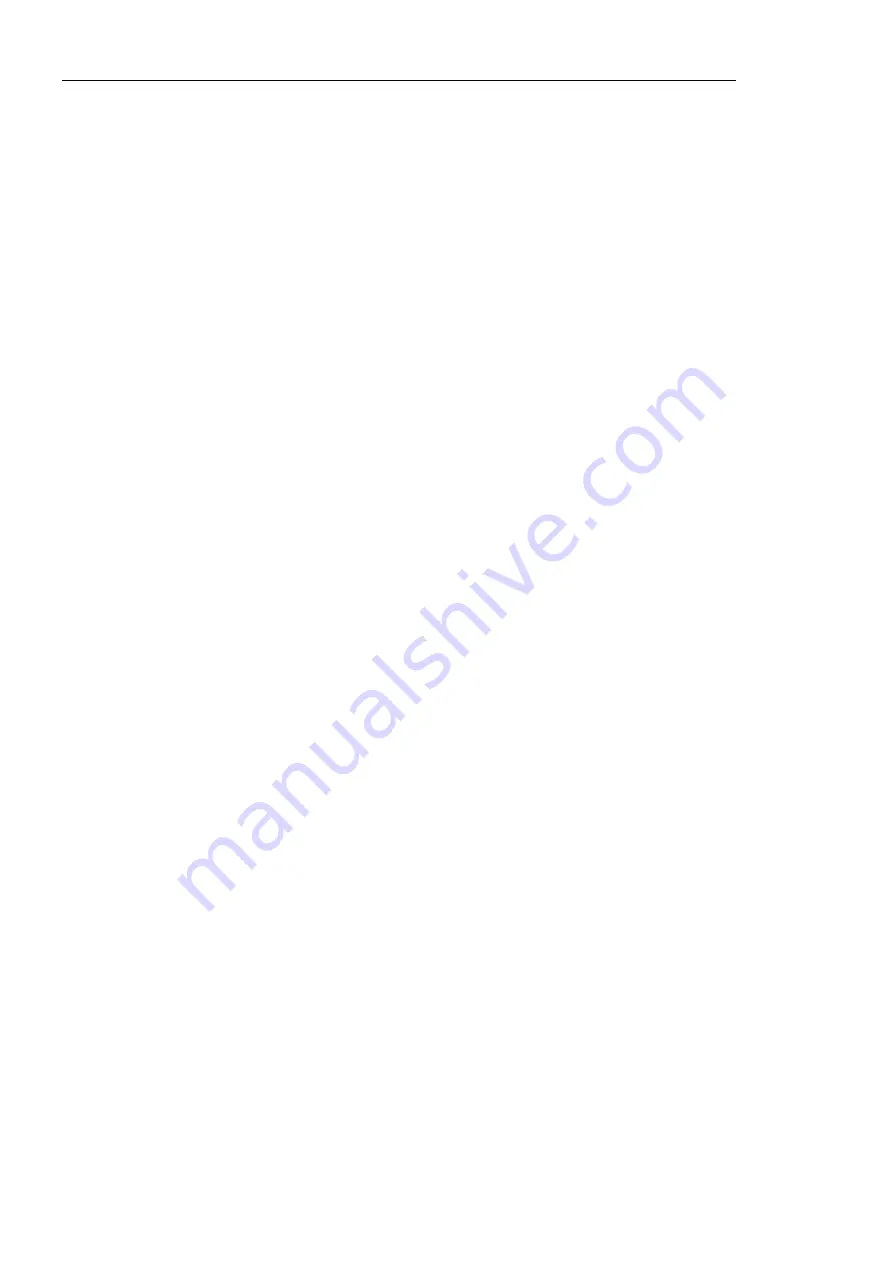
CHAPTER 3 ENGINE
T-Boss550 SERVICE MANUAL20.0
CHAPTER 3 ENGINE PAGE. 3- 1
CHAPTER 3 ENGINE
500 cc
3 .1 Removal and Installation of Engine
3.2 Engine Overhaul Information
3 .3 Checks & Adjustment
3 .4 Engine Removal, Inspection & Installation
3 .5
FUEL INJECTION SYSTEM
3 .6
Cooling and Lubrication System
3 .7
Troubleshooting
Содержание T-Boss 550
Страница 1: ...SERVICE MANUAL T Boss 550...
Страница 10: ...CHAPTER 1 GENERALINFORMATION T Boss550 SERVICE MANUAL 20 0 CHAPTER 1 GENERAL PAGE 1 6 1 3 VEHICLE DIMENSIONS...
Страница 11: ...CHAPTER 1 GENERALINFORMATION T Boss550 SERVICE MANUAL 20 0 CHAPTER 1 GENERAL PAGE 1 7 NOTES...
Страница 25: ...CHAPTER 2 MAINTENANCE T Boss550 SERVICE MANUAL 20 0 CHAPTER 2 MAINTENANCE PAGE 2 14 NOTES...
Страница 36: ...CHAPTER 3 ENGINE T Boss550 SERVICE MANUAL20 0 CHAPTER 3 ENGINE PAGE 3 11 3 2 5 Engine Exterior and Engine No...
Страница 87: ...CHAPTER 3 ENGINE T Boss550 SERVICE MANUAL20 0 CHAPTER 3 ENGINE PAGE 3 62 Primary and Secondary Sheave...
Страница 160: ...CHAPTER 3 ENGINE T Boss550 SERVICE MANUAL20 0 CHAPTER 3 ENGINE PAGE 3 135 3 6 7 8 Lubrication System Illustration...
Страница 166: ...CHAPTER 3 ENGINE T Boss550 SERVICE MANUAL20 0 CHAPTER 3 ENGINE PAGE 3 141 NOTES...
Страница 176: ...CHAPTER 4 CHASSIS T Boss550 SERVICE MANUAL20 0 CHAPTER 4 CHASSIS PAGE 4 10 NOTES...
Страница 209: ...CHAPTER 5 FINAL DRIVE T Boss550 SERVICE MANUAL18 0 CHAPTER 5 FINAL DRIVE 5 33 NOTES...
Страница 224: ...CHAPTER 6 BRAKES T Boss 550 SERVICE MANUAL20 0 CHAPTER 7 BRAKES PAGE 7 15 NOTES...
Страница 245: ...CHAPTER 7 ELECTRICAL T Boss550 SERVICE MANUAL 20 0 CHAPTER 7 ELECTRICAL CTRICAL PAGE 7 21 7 7 LIGHTING SYSTEM...
Страница 250: ...CHAPTER 7 ELECTRICAL T Boss550 SERVICE MANUAL 20 0 CHAPTER 7 ELECTRICAL CTRICAL PAGE 7 26 Switch table...
Страница 254: ...CHAPTER 7 ELECTRICAL T Boss550 SERVICE MANUAL 20 0 CHAPTER 7 ELECTRICAL CTRICAL PAGE 7 30 7 10 SWITCHES Optional...
Страница 258: ...CHAPTER 7 ELECTRICAL T Boss550 SERVICE MANUAL 20 0 CHAPTER 7 ELECTRICAL CTRICAL PAGE 7 34 7 13 WIRING DIAGR...