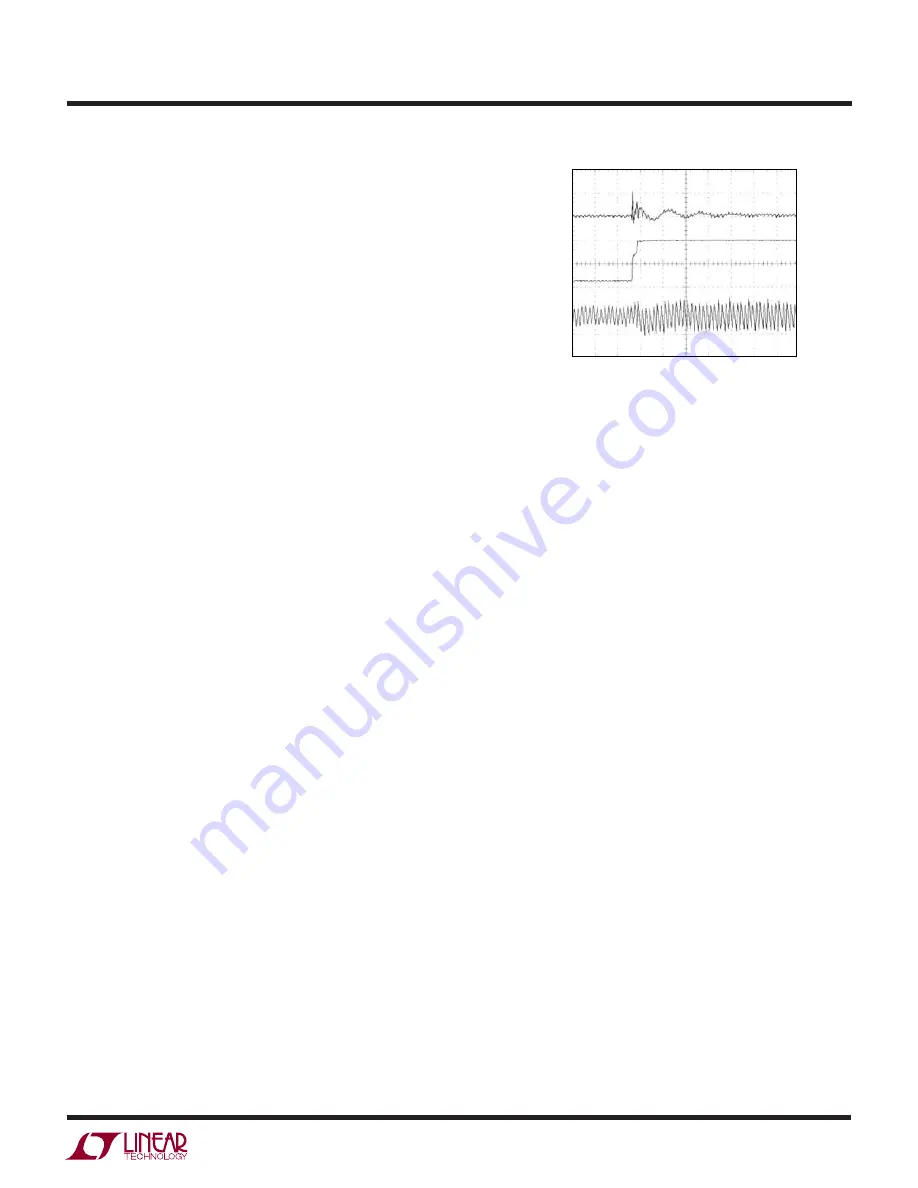
LTC3703-5
9
37035fa
OPERATIO
U
(Refer to Functional Diagram)
When the load current increases, it causes a drop in the
feedback voltage relative to the reference. The COMP volt-
age then rises, increasing the duty ratio until the output
feedback voltage again matches the reference voltage. In
normal operation, the top MOSFET is turned on when the
RS latch is set by the on-chip oscillator and is turned off
when the PWM comparator trips and resets the latch. The
PWM comparator trips at the proper duty ratio by compar-
ing the error amplifier output (after being “compensated”
by the line feedforward multiplier) to a sawtooth waveform
generated by the oscillator. When the top MOSFET is turned
off, the bottom MOSFET is turned on until the next cycle
begins or, if Pulse Skip Mode operation is enabled, until
the inductor current reverses as determined by the reverse
current comparator. MAX and MIN comparators ensure
that the output never exceed
±
5% of nominal value by
monitoring V
FB
and forcing the output back into regulation
quickly by either keeping the top MOSFET off or forcing
maximum duty cycle. The operation of its other features—
fast transient response, outstanding line regulation, strong
gate drivers, short-circuit protection, and shutdown/
soft-start—are described below.
Fast Transient Response
The LTC3703-5 uses a fast 25MHz op amp as an error am-
plifier. This allows the compensation network to be opti-
mized for better load transient response. The high
bandwidth of the amplifier, along with high switching fre-
quencies and low value inductors, allow very high loop
crossover frequencies. The 800mV internal reference allows
regulated output voltages as low as 800mV without exter-
nal level shifting amplifiers.
Line Feedforward Compensation
The LTC3703-5 achieves outstanding line transient re-
sponse using a patented feedforward correction scheme.
With this circuit the duty cycle is adjusted instantaneously
to changes in input voltage, thereby avoiding unaccept-
able overshoot or undershoot. It has the added advantage
of making the DC loop gain independent of input voltage.
Figure 1 shows how large transient steps at the input have
little effect on the output voltage.
20
µ
s/DIV
V
OUT
50mV/DIV
AC COUPLED
V
OUT
= 12V
I
LOAD
= 1A
25V TO 60V V
IN
STEP
V
IN
20V/DIV
I
L
2A/DIV
37035 F01
Figure 1. Line Transient Performance
Strong Gate Drivers
The LTC3703-5 contains very low impedance drivers
capable of supplying amps of current to slew large MOSFET
gates quickly. This minimizes transition losses and allows
paralleling MOSFETs for higher current applications. A
60V floating high side driver drives the top side MOSFET
and a low side driver drives the bottom side MOSFET (see
Figure 2). They can be powered from either a separate DC
supply or a voltage derived from the input or output
voltage (see MOSFET Driver Supplies section). The bot-
tom side driver is supplied directly from the DRV
CC
pin.
The top MOSFET drivers are biased from floating boot-
strap capacitor C
B
, which normally is recharged during
each off cycle through an external diode from DRV
CC
when
the top MOSFET turns off. In Pulse Skip Mode operation,
where it is possible that the bottom MOSFET will be off for
an extended period of time, an internal counter guarantees
that the bottom MOSFET is turned on at least once every
10 cycles for 10% of the period to refresh the bootstrap
capacitor. An undervoltage lockout keeps the LTC3703-5
shut down unless this voltage is above 4.1V.
The bottom driver has an additional feature that helps
minimize the possibility of external MOSFET shoot-thru.
When the top MOSFET turns on, the switch node dV/dt
pulls up the bottom MOSFET’s internal gate through the
Miller capacitance, even when the bottom driver is holding
the gate terminal at ground. If the gate is pulled up high
enough, shoot-thru between the top side and bottom side