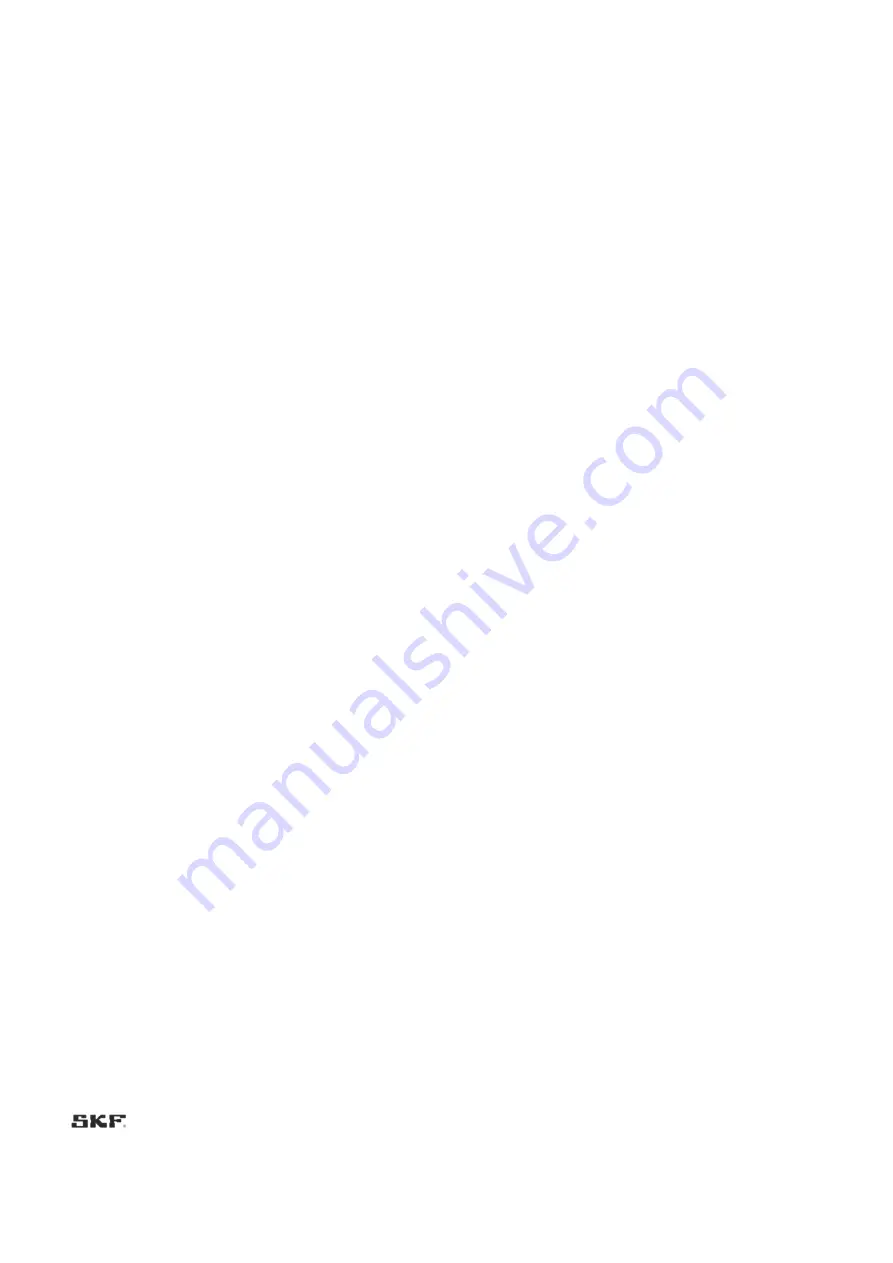
11
2. Lubricants
2.1 General information
Lubricants are selected specifically for the relevant application.
The manufacturer or operator of the machine should ideally
make the selection in consultation with the supplier of the
lubricant. If you have no or little experience in selecting
lubricants for lubrication systems, please contact us. We would
be happy to assist you in selecting suitable lubricants and
components to build a lubrication system optimized for your
particular application. Consider the following points when
selecting/using lubricants. This will spare you potential
downtime and damage to the machine or lubrication system.
2.2 Material compatibility
The lubricants must generally be compatible with the following
materials:
•
Plastics: ABS, CR, FPM, NBR, NR, PA, PET, PMMA, POM, PP,
PS, PTFE, PU, PUR
•
Metals: steel, gray cast iron, brass, copper, aluminum
2.3 Temperature properties
The lubricant used must be suitable for the specific ambient
temperature of the product. The viscosity approved for proper
functioning must neither be exceeded at low temperatures nor
fall too low at high temperatures. For the approved viscosity,
see the “Technical data” chapter.
2.4 Aging of lubricants
Based on past experience with the lubricant used, checks should
be conducted at regular intervals defined by the operator, to
determine whether the lubricant needs to be replaced due to
aging processes (oil separation). In case of doubt regarding the
continued suitability of the lubricant, it must be replaced before
the system is started up again. If you do not yet have any
experience with the lubricant used, we recommend conducting
a check after just one week.
2.5 Avoidance of faults and hazards
To avoid faults and hazards, please observe the following:
•
When handling lubricants, observe the relevant safety data
sheet (SDS) and any hazard labeling on the packaging.
•
Due to the large number of additives, some lubricants that
meet the pumpability requirements specified in the manual
are not suitable for use in centralized lubrication systems.
•
Whenever possible, always use SKF lubrication greases. They
are ideal for use in lubrication systems.
•
Do not mix lubricants. This can have unpredictable effects on
the properties and usability of the lubricant.
•
Use lubricants containing solid lubricants only after technical
consultation with SKF.
• The lubricant’s ignition temperature has to be at least
50 kelvin above the maximum surface temperature of the
components.
2.6 Solid lubricants
Solid lubricants may only be used after prior consultation with
SKF. When solid lubricants are used in lubrication systems, the
following rules generally apply:
Graphite:
•
Maximum graphite content 8%
•
Maximum grain size 25 μm (preferably in lamellar form)
MoS2:
•
Maximum MoS2 content 5%
•
Maximum grain size 15 μm
Copper:
•
Lubricants containing copper are known to lead to coatings
forming on pistons, bore holes, and mating surfaces. This can
result in blockages in the centralized lubrication system.
Calcium carbonate:
•
Lubricants containing calcium carbonate are known to lead to
very heavy wear on pistons, bore holes, and mating surfaces.
Calcium hydroxide:
•
Lubricants containing calcium hydroxide are known to harden
considerably over time, which can lead to failure of the
centralized lubrication system.
PTFE, zinc, and aluminum:
•
For these solid lubricants, it is not yet possible to define any
limit values for use in lubrication systems on the basis of
existing knowledge and practical experience.