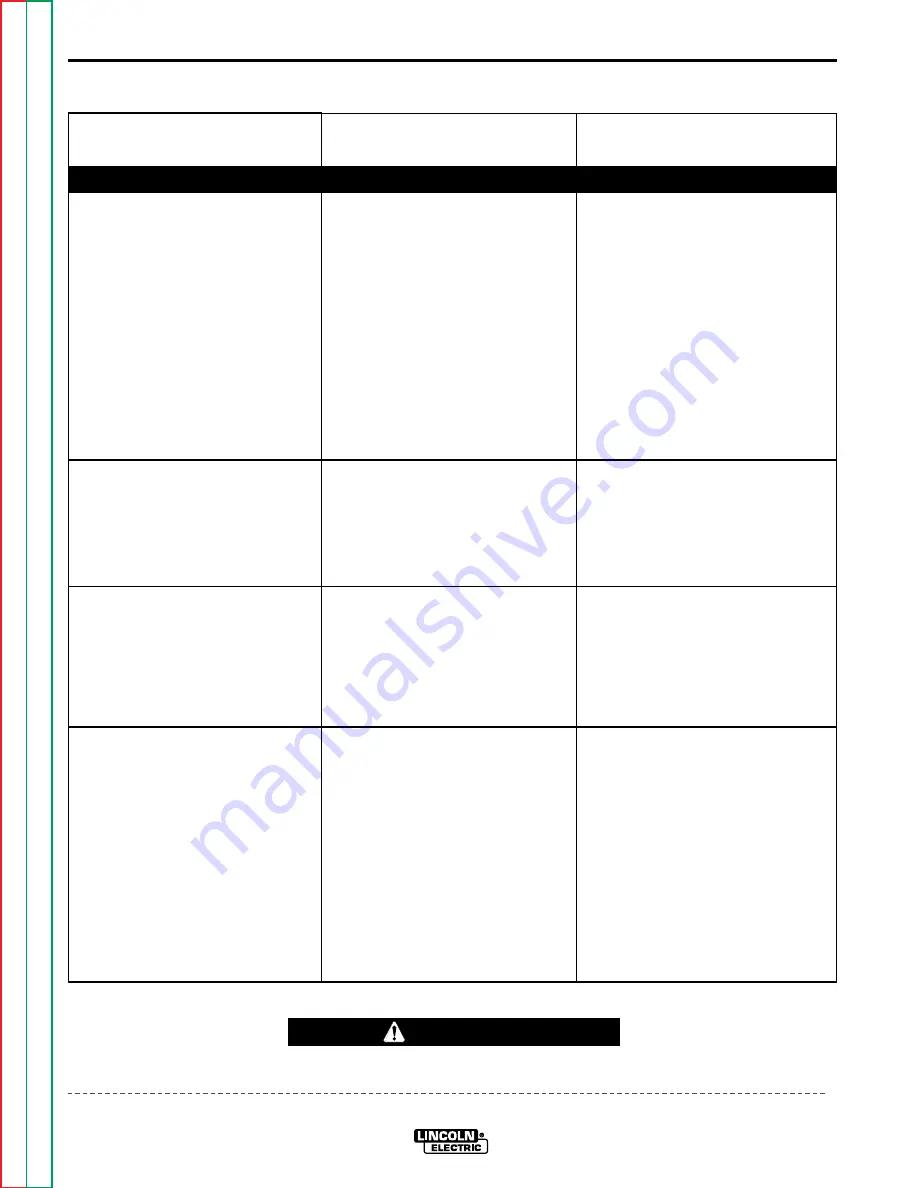
Retur
n to Section TOC
Retur
n to Section TOC
Retur
n to Section TOC
Retur
n to Section TOC
Retur
n to Master TOC
Retur
n to Master TOC
Retur
n to Master TOC
Retur
n to Master TOC
PROBLEMS
(SYMPTOMS)
POSSIBLE AREAS OF
MISADJUSTMENTS(S)
RECOMMENDED
COURSE OF ACTION
F-6
TROUBLESHOOTING AND REPAIR
F-6
Observe all Safety Guidelines detailed throughout this manual
FUNCTION PROBLEMS (Continued)
If for any reason you do not understand the test procedures or are unable to perform the tests/repairs safely, contact the Lincoln Electric
Service Department for technical troubleshooting assistance before you proceed. Call 216-383-2531 or 1-800-833-9353.
CAUTION
LN-742 & LN-742H
The LN-742 voltmeter does not
function or read correctly when the
actual arc voltage is present. The
wire feeder is feeding wire correctly.
The LN-742 shuts down while weld-
ing and the HXX symbol appears on
the display.
The display and/or indicator lights
do not change when the arrow or
select keys are pressed.
The arrow keys do not change the
welding wire feed speed.
1. Make sure the polarity switch on
the Lincoln welding power
source is in the correct position
for the welding process.
2. Check or replace the control
cable. Check the continuity
(zero ohms) of leads #21 and
#67.
1. Check for mechanical restric-
tions in the wire feed path.
1. Make sure the control cable is
connected to the welding power
source correctly.
2. Check the 42 VAC fuse or circuit
breaker in the welding power
source.
1. If a remote control unit is con-
nected to the LN-742 the arrow
keys will not change welding wire
feed speed. Use the WFS pot on
the remote control unit or discon-
nect the remote control unit and
use the arrow keys.
1. Check the DC voltage at plug J1
pin 6 (lead #67) to pin 11
(lead #21) when arc voltage is
present at the power source out-
put terminals. Arc voltage should
be present at these leads. If not,
check the leads between the
input cable receptacle and plug
J1. Plug J1 is located on the con-
trol board. See wiring diagram.
2. If arc voltage is present at plug J1
the control board may be faulty.
Replace.
1. Perform the
Drive Motor Test.
2. The gear box may be defective.
Check or replace.
3. The control board may be faulty.
1. Perform the
Keypad Resistance
Test.
2. The display board may be faulty.
3. The control board may be faulty.
1. The display board may be faulty.