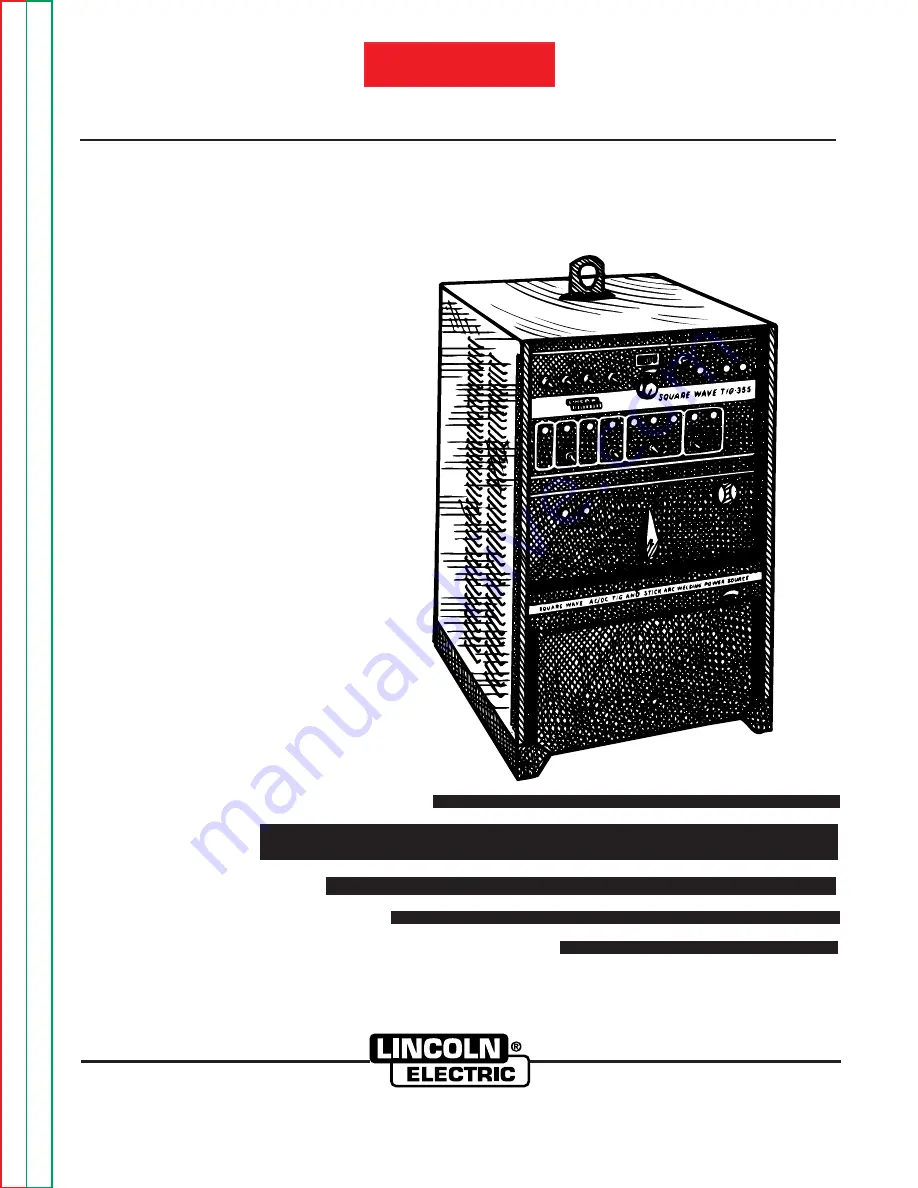
SERVICE MANUAL
World’s Leader in Welding and Cutting Products Premier Manufacturer of Industrial Motors
Sales and Service through subsidiaries and Distributors Worldwide
22801 St. Clair Ave. Cleveland, Ohio 44117-1199 U.S.A. Tel. (216) 481-8100
SVM118-A
August, 1998
For use with machines having Code Numbers:
9951
9952
9953
9954
9955
SQUARE WAVE TIG 355
Safety Depends on You
Lincoln arc welding and cutting
equipment is designed and
built with safety in mind.
However, your overall safety
can be increased by proper
installation . . . and thoughtful
operation on your part. DO
NOT INSTALL, OPERATE OR
REPAIR THIS EQUIPMENT
WITHOUT READING THIS
MANUAL AND THE SAFETY
PRECAUTIONS CONTAINED
THROUGHOUT. And, most
importantly, think before you
act and be careful.
RETURN TO MAIN INDEX
Retur
n to Master TOC
Retur
n to Master TOC
Retur
n to Master TOC
Retur
n to Master TOC
V
iew Safety Info
V
iew Safety Info
V
iew Safety Info
V
iew Safety Info