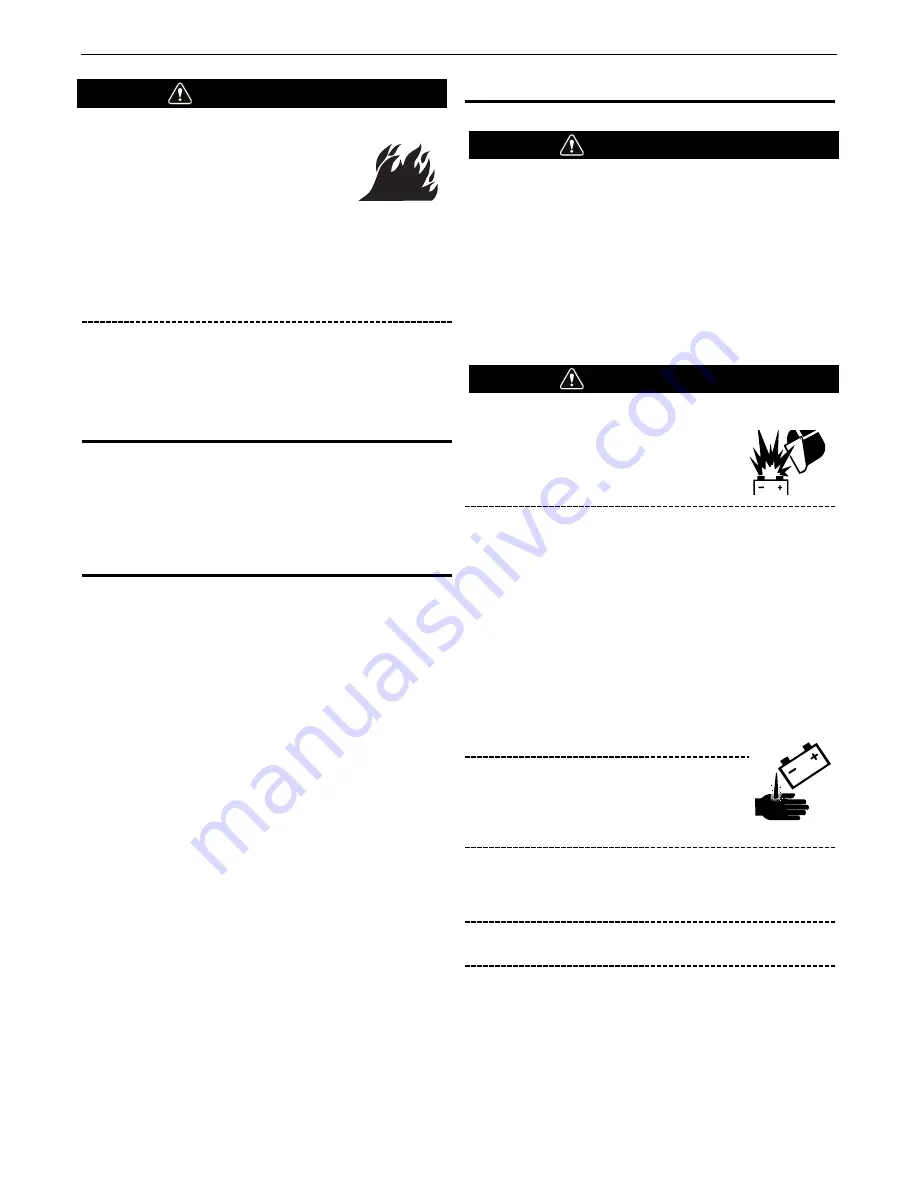
A-4
INSTALLATION
SAE-400
®
DIESEL FUEL can cause fire.
•
Stop engine while fueling.
•
Do not smoke when fueling.
•
Keep sparks and flame away from tank.
•
Do not leave unattended while fueling.
•
Wipe up spilled fuel and allow fumes to clear before
starting engine.
•
Do not overfill tank, fuel expansion may cause overflow.
DIESEL FUEL ONLY
Fill the fuel tank with clean, fresh diesel fuel. The capacity of the
fuel tank is 22.5 gallons (85.1 liters). See engine Operator’s
Manual for specific fuel recommendations.
Note: Before starting the engine, be sure the fuel shutoff valve is
in the open position.
ENGINE COOLING SYSTEM
The cooling system has been filled at the factory with a 50-50
mixture of ethylene glycol antifreeze and water. Check the
radiator level and add a 50-50 solution as needed. (See Engine
Manual or antifreeze container for alternate antifreeze recom-
mendation.)
ENGINE BREAK-IN PERIOD
Lincoln Electric selects high quality, heavy-duty industrial engines
for the portable welding machines we offer. While it is normal to
see a small amount of crankcase oil consumption during initial
operation, excessive oil use, wet stacking (oil or tar like substance
at the exhaust port), or excessive smoke is not normal.
Larger machines with a capacity of 350 amperes and higher,
which are operated at low or no-load conditions for extended
periods of time are especially susceptible to the conditions
described above. To accomplish successful engine break-in, most
diesel-powered equipment needs only to be run at a reasonably
heavy load within the rating of the welder for some period of time
during the engine’s early life. However, if the welder is subjected
to extensive light loading, occasional moderate to heavy loading of
the engine may sometimes be necessary. Caution must be
observed in correctly loading a diesel/generator unit.
1. Connect the welder output studs to a suitable resistive load
bank. Note that any attempt to short the output studs by
connecting the welding leads together, direct shorting of the
output studs, or connecting the output leads to a length of
steel will result in catastrophic damage to the generator and
voids the warranty.
2. Set the welder controls for an output current and voltage
within the welder rating and duty cycle. Note that any
attempt to exceed the welder rating or duty cycle for any
period of time will result in catastrophic damage to the
generator and voids the warranty.
3. Periodically shut off the engine and check the crankcase oil
level.
BATTERY CONNECTION
•
Use caution as the electrolyte is a strong acid that can
burn skin and damage eyes.
•
Remove and discard the insulating cap from the
negative battery terminal. Attach and tighten negative
battery cable terminal.
NOTE: This machine is furnished with a wet charged battery; if
unused for several months, the battery may require a booster
charge. Be careful to charge the battery with the correct polarity.
Make sure that the battery is level while charging.
Gases from battery can explode.
Keep sparks, flame and cigarettes away
from battery.
To prevent EXPLOSION when:
•
INSTALLING A NEW BATTERY — disconnect negative
cable from old battery first and connect to new battery
last.
•
CONNECTING A BATTERY CHARGER — remove
battery from welder by disconnecting negative cable
first, then positive cable and battery clamp. When
reinstalling, connect negative cable last. Keep well
ventilated.
•
USING A BOOSTER — connect positive lead to battery
first then connect negative lead to negative battery lead
at the lower control panel support.
BATTERY ACID can burn eyes and skin.
•
Wear gloves and eye protection and be
careful when working near battery.
•
Follow instructions printed on battery.
IMPORTANT: To prevent ELECTRICAL DAMAGE WHEN:
a) Installing a new batterie.
b) Using a booster.
Use correct polarity — Negative Ground.
To prevent BATTERY BUCKLING, tighten the nuts on battery
until snug. DO NOT OVERTIGHTEN.
WARNING
WARNING
WARNING
Содержание SAE-400 SEVERE DUTY IM727
Страница 28: ...No Image Miscellaneous Items 4 SAE 400 Perkins 12311 Printed 08 17 2015 at 08 38 18 Produced by Enigma ...
Страница 33: ...P 909 C jpg Final Assembly SAE 400 Perkins 12311 9 Printed 08 17 2015 at 08 38 18 Produced by Enigma ...
Страница 36: ...P 909 D jpg Engine Assembly 12 SAE 400 Perkins 12311 Printed 08 17 2015 at 08 38 18 Produced by Enigma ...
Страница 45: ...P 909 G jpg Control Panel Assembly SAE 400 Perkins 12311 21 Printed 08 17 2015 at 08 38 18 Produced by Enigma ...
Страница 49: ...P 909 J jpg Remote Control SAE 400 Perkins 12311 25 Printed 08 17 2015 at 08 38 18 Produced by Enigma ...
Страница 51: ...P 909 K jpg Generator Brush Holder SAE 400 Perkins 12311 27 Printed 08 17 2015 at 08 38 18 Produced by Enigma ...