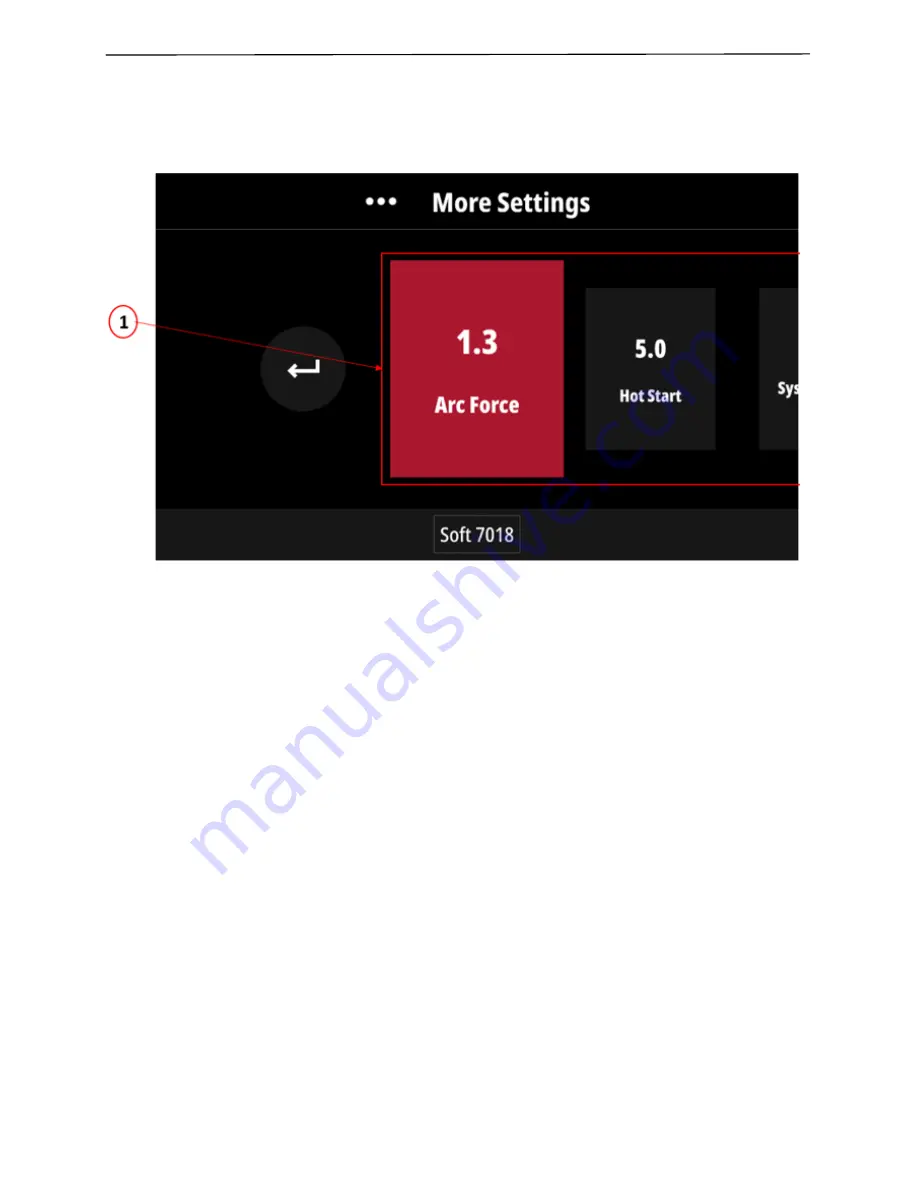
OPERATION
B-19
MORE SETTINGS MENU (ALL PROCESSES)
FIGURE B.15
1.
Advanced process se�ngs will appear here. Each weld process will have different se�ngs. The
most common advanced se�ngs are: Pinch, Arc Force, Hot Start, Pre-Flow Time, Post-Flow
Time, 2-Step/4-Step Trigger, and Ul�marc. Advanced se�ngs will only be displayed when set
to a non-zero value.
POWER WAVE 300C
®
Содержание POWER WAVE 300C
Страница 64: ...POWER WAVE 300C DIMENSION PRINT F 3 39 67 20 51 39 44 25 92 25 70...
Страница 65: ...POWER WAVE 300C NOTES...