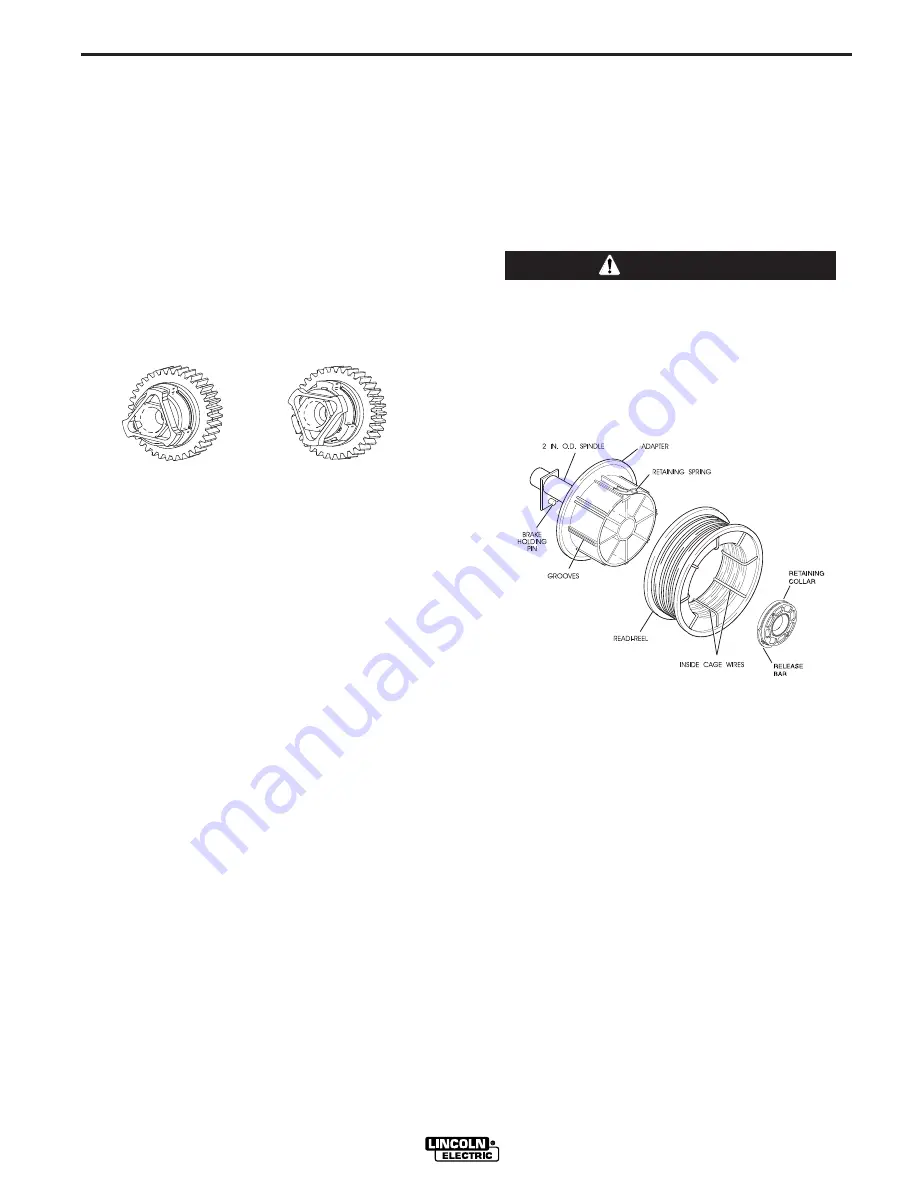
B-3
B-3
OPERATION
PROCEDURE FOR CHANGING
DRIVE AND IDLE ROLL SETS
1. Turn off the power source.
2. Release the pressure on the idle roll by swinging
the adjustable pressure arm down toward the back
of the machine. Lift the cast idle roll assembly and
allow it to sit in an upright position..
3. Remove the outside wire guide retaining plate by
loosening the two large knurled screws.
4. Twist the drive roll retaining mechanism to the
unlocked position as shown below and remove the
drive roll. (See Figure A.4)
5. Remove the inside wire guide plate.
6. Replace the drive and idle rolls and inside wire
guide with a set marked for the new wire size.
NOTE: Be sure that the gun liner and contact tip
are also sized to match the selected wire size.
7. Manually feed the wire from the wire reel, over the
drive roll groove and through the wire guide and
then into the brass bushing of the gun and cable
assembly.
8. Replace the outside wire guide retaining plate by
tightening the two large knurled screws. Reposition
the adjustable pressure arm to its original position
to apply pressure. Adjust pressure as necessary.
WIRE REEL LOADING - READI-REELS,
SPOOLS OR COILS
To Mount a 30 Lb. (14 kg) Readi-Reel Package
(Using the Molded Plastic K363-P Readi-Reel
Adapter:)
1. Open the Wire Drive Compartment Door
2. Depress the Release Bar on the Retaining Collar and remove it from
the spindle.
3. Place the Optional Adapter on the spindle
4. Re-install the Retaining Collar. Make sure that the Release Bar
“
pops
up
”
and that the collar retainers fully engage the retaining ring groove
on the spindle.
5. Rotate the spindle and adapter so the retaining spring is at the 12
o'clock position.
6. Position the Readi-Reel so that it will rotate in a direction when feed-
ing so as to be de- reeled from top of the coil.
7. Set one of the Readi-Reel inside cage wires on the slot in the retain-
ing spring tab.
8. Lower the Readi-Reel to depress the retaining spring and align the
other inside cage wires with the grooves in the molded adapter.
9. Slide cage all the way onto the adapter until the retaining spring
"pops up" fully.
CHECK TO BE SURE THE RETAINING SPRING HAS FULLY
RETURNED TO THE LOCKING POSITION AND HAS SECURELY
LOCKED THE READI-REEL CAGE IN PLACE. RETAINING SPRING
MUST REST ON THE CAGE, NOT THE WELDING ELECTRODE.
-----------------------------------------------------------------------------------------------
10. To remove Readi-Reel from Adapter, depress retaining spring tab
with thumb while pulling the Readi-Reel cage from the molded
adapter with both hands. Do not remove adapter from spindle.
FIGURE B.1
To Mount 10 to 44 Lb. (4.5-20 kg) Spools (12"/300
mm Diameter) or 14Lb.(6 Kg) Innershield Coils:
(For 13-14 lb. (6 Kg) Innershield coils, a K435 Coil Adapter must be
used).
1. Open the Wire Drive Compartment Door
2. Depress the Release Bar on the Retaining Collar and remove it
from the spindle.
3. Place the spool on the spindle making certain the spindle brake
pin enters one of the holes in the back side of the spool (Note:
an arrow mark on the spindle lines up with the brake holding pin
to assist in lining up a hole). Be certain the wire comes off the
reel in a direction so as to de-reel from the top of the coil.
4. Re-install the Retaining Collar. Make sure that the Release Bar
“
pops up
”
and that the collar retainers fully engage the retaining
ring groove on the spindle.
TO START THE WELDER
Turn the
“
Power Switch
”
switch to
“
ON
”
. This lights the red LED dis-
play lights. With the desired voltage and wire speed selected, oper-
ate the gun trigger for welder output and to energize the wire feed
motor.
CAUTION
POWER MIG 200
LOCKED POSITION
UNLOCKED POSITION
FIGURE A.4