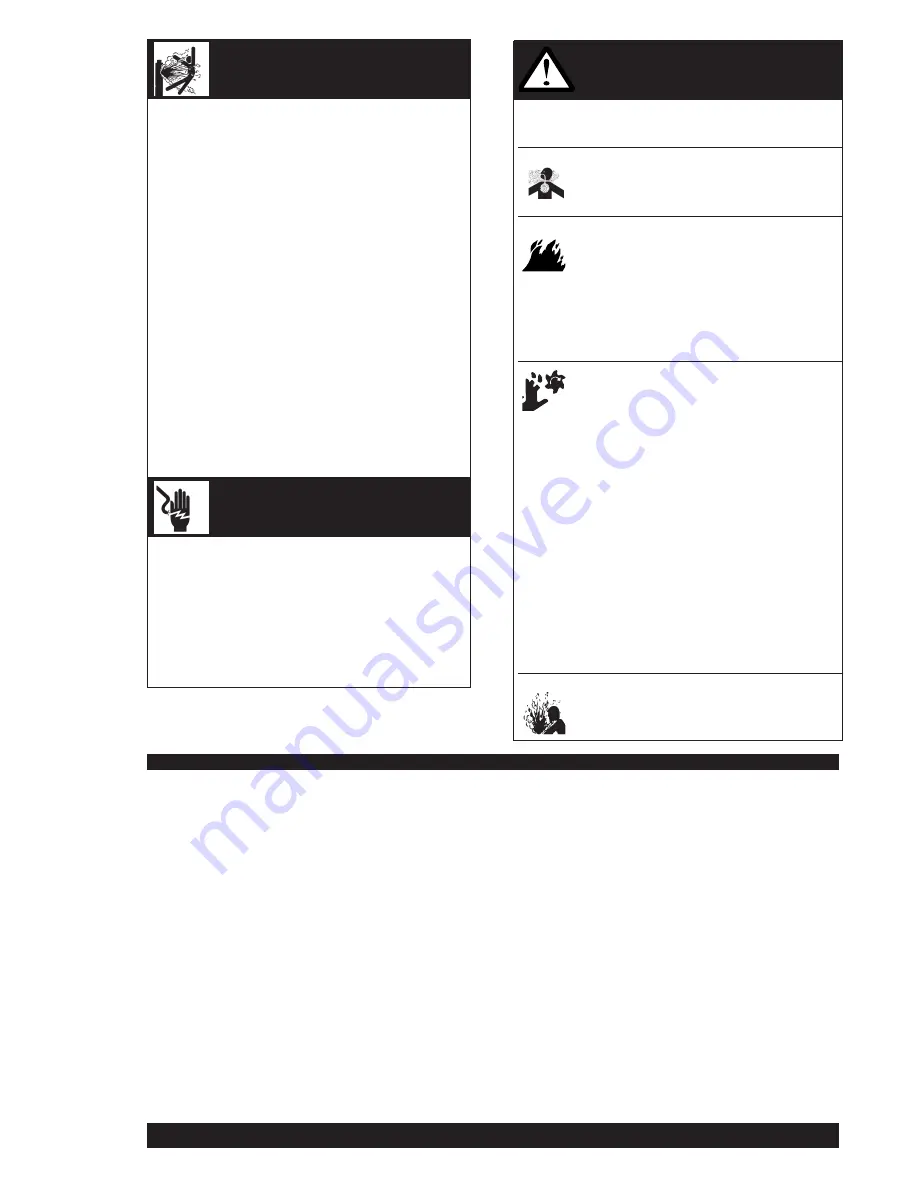
IMA 600A
REDI-MIG 4D
Page 3
5.
a.
Use only compressed gas cylinders containing the
correct shielding gas for the process used and
properly operating regulators, designed for the gas
and pressure used. All hoses, fittings, etc. should be
suitable for the application and maintained in good
condition.
b.
Always keep cylinders in an upright position and
securely chained to an undercarriage or fixed support.
c.
Cylinders should be located :
•
Away from areas where they may be struck or
subjected to physical damage.
•
A safe distance from arc welding or cutting
operations and any other source of heat, sparks
or flame.
d.
Never allow the electrode, electrode holder, or any
other electrically “hot” parts to touch a cylinder.
e.
Keep your head and face away from the cylinder valve
outlet when opening the cylinder valve.
f.
Valve protection caps should always be in place and
hand-tight except when the cylinder is in use or
connected for use.
g.
Read and follow the instructions on compressed gas
cylinders and associated equipment, and AS 2030
Parts 1 & 2.
6.
a.
Turn off input power using the disconnect switch at the
fuse box before working on the equipment.
b.
Install equipment in accordance with the SAA Wiring
Rules, all local codes and the manufacturer’s
recommendations.
c.
Ground the equipment in accordance with the SAA
Wiring Rules and the manufacturer’s
recommendations.
7.
a.
Turn the engine off before troubleshooting and
maintenance work unless the maintenance
work requires it to be running.
b.
Operate engines in open, well ventilated
areas or vent the engine exhaust fumes
outdoors.
c.
Do not add fuel near an open flame,
welding arc or when the engine is running.
Stop the engine and allow it to cool before
refuelling to prevent spilled fuel from
vaporizing on contact with hot engine parts
and igniting. Do not spill fuel when filling
tank. If fuel is spilled, wipe it up and do not
start engine until fumes have been
eliminated.
d.
Keep all equipment, safety guards, covers
and devices in position and in good repair.
Keep hands, hair, clothing and tools away
from V-belts, gears, fans and all other
moving parts when starting, operating or
repairing equipment.
e.
In some cases it may be necessary to
remove safety guards to perform required
maintenance. Remove guards only when
necessary and replace them when the
maintenance requiring their removal is
complete. Always use the greatest care
when working near moving parts.
f.
Do not put your hands near the engine fan.
Do not attempt to override the governor or
idler by pushing on the throttle control rods
while the engine is running.
g.
To prevent accidentally starting petrol
engines while turning the engine or welding
generator during maintenance work,
disconnect the spark plug wires, distributor
cap or magneto wire as appropriate.
h.
To avoid scalding do not remove the
radiator pressure cap when the engine is
hot.
CYLINDER may explode
if damaged
FOR ELECTRICALLY
powered equipment
FOR ENGINE
powered equipment
HAVE ALL INSTALLATIONS, OPERATION, MAINTENANCE AND REPAIR WORK PERFORMED BY QUALIFIED PEOPLE
HOW TO ORDER REPLACEMENT PARTS
To ensure that you receive the correct replacement part the following procedure should be followed:
1. Quote Serial Number and Code Number.
2. Quote the Description, Item Number and Parts List Number of the desired part. When ordering parts for items carrying brand
names of other companies, such as fan motors, drive shafts, etc., be sure to include the other company’s name and part number
and other relevant information.
3. Should the primary cord be damaged, a special cord is required, and is available from Lincoln Electric.
4. Parts should be ordered from Lincoln, its offices or the nearest Authorised Service Facilities. (The “Lincoln Service Directory”
listing these shops geographically is available on request.)
Note:
“Hardware” in the Lincoln Parts Lists are not Lincoln stock items but can be obtained via the Authorised Service Facilities.
Component parts of assemblies such as stator coils or armature coils, etc., which require electrical testing or locating fixtures are not
considered replaceable items. This is to ensure that the customer receives parts which will keep the welder in the best operating condition.
BUY ONLY GENUINE REPAIR PARTS
For more detailed information it is strongly recommended that you purchase a copy of “Safety in Welding and Allied Processes AS1674
Parts 1 & 2” and WTIA Technical Note 7. All WTIA publications are available from the Welding Technology Institute of Australia, P.O. Box
6165, Silverwater NSW 2128. For copies of various Australian Standards contact your local S.A.A. office.
Содержание KA 1435
Страница 14: ...Page 14 REDI MIG 4D Remote IMA 600A NOTES...
Страница 18: ...Page 18 REDI MIG 4D Remote IMA 600A Wire Drive Assembly AP 56 E Operative Apr 2004 Supersedes NEW Ref 410...
Страница 20: ...Page 20 REDI MIG 4D Remote IMA 600A Wire Drive Assembly AP 56 F Operative Apr 2004 Supersedes NEW Ref 410 2...
Страница 22: ...Page 22 REDI MIG 4D Remote IMA 600A NOTES...
Страница 23: ...IMA 600 REDI MIG 4D Remote Page 23 NOTES...