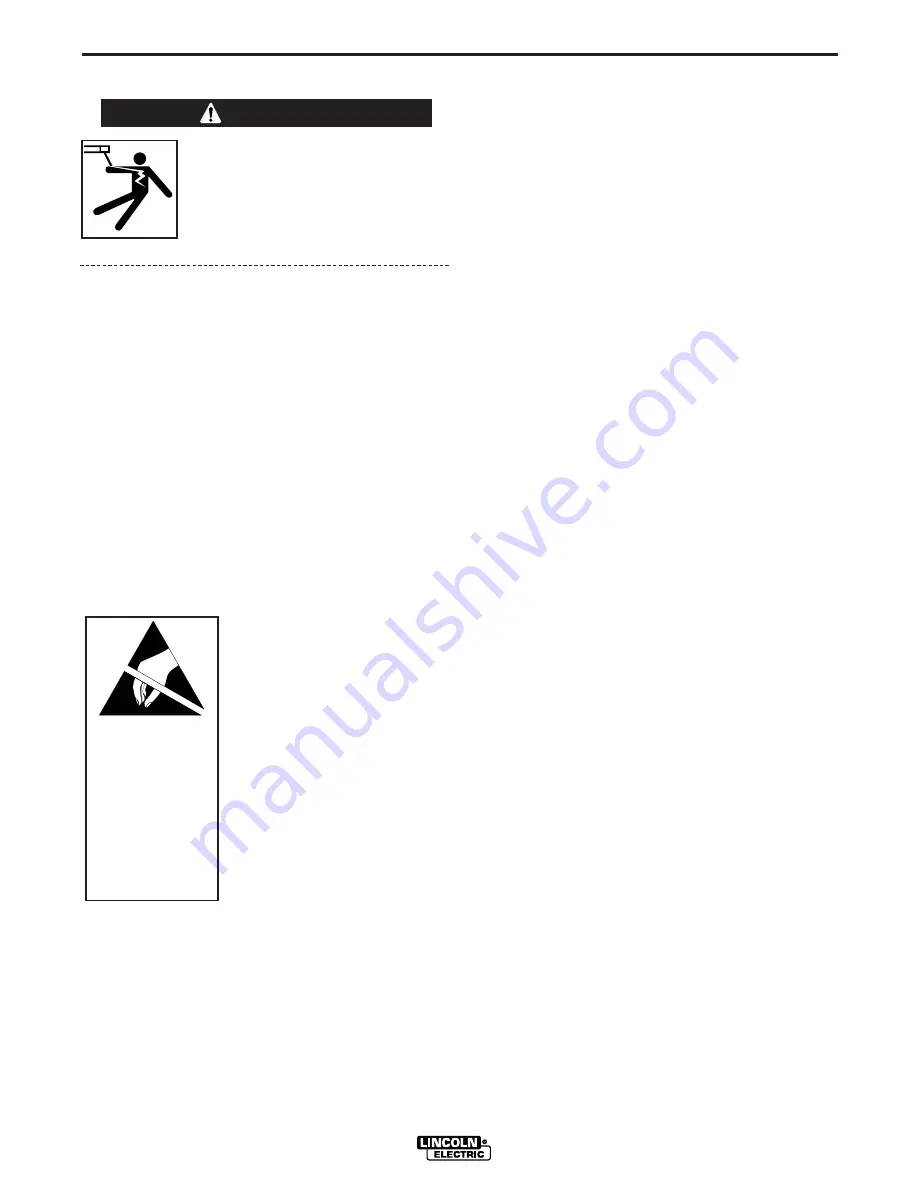
ELECTRIC SHOCK can kill.
Have an electrician install and ser-
vice this equipment. Turn the input
power OFF at the fuse box before
working on equipment. Do not touch
electrically hot parts.
E-2
TROUBLESHOOTING
E-2
DC-600
CAUTION:
Sometimes machine failures appear to be
due to PC board failures. These problems can some-
times be traced to poor electrical connections. To
avoid problems when troubleshooting and replacing
PC boards, please use the following procedure:
1. Determine to the best of your technical ability that
the PC board is the most likely component causing
the failure symptom.
2. Check for loose connections at the PC board to
assure that the PC board is properly connected.
3. If the problem persists, replace the suspect PC
board using standard practices to avoid static elec-
trical damage and electrical shock. Read the warn-
ing inside the static resistant bag and perform the
following procedures:
P.C. Board can be damaged by static electricity.
• Remove your body’s static
charge before opening the static-
shielding bag. Wear an anti-static
wrist strap. For safety, use a 1
Meg ohm resistive cord connect-
ed to a grounded part of the
equipment frame.
• If you don’t have a wrist strap,
touch an unpainted, grounded,
part of the equipment frame.
Keep touching the frame to pre-
vent static build-up. Be sure not
to touch any electrically live parts
at the same time.
• Tools which come in contact with the P.C. Board
must be either conductive, anti-static or static-dis-
sipative.
• Remove the P.C. Board from the static-shielding
bag and place it directly into the equipment. Don’t
set the P.C. Board on or near paper, plastic or
cloth which could have a static charge. If the P.C.
Board can’t be installed immediately, put it back in
the static-shielding bag.
• If the P.C. Board uses protective shorting jumpers,
don’t remove them until installation is complete.
• If you return a P.C. Board to The Lincoln Electric
Company for credit, it must be in the static-shield-
ing bag. This will prevent further damage and
allow proper failure analysis.
4. Test the machine to determine if the failure symp-
tom has been corrected by the replacement PC
board.
NOTE:
It is desirable to have a spare (known good)
PC board available for PC board troubleshooting.
NOTE:
Allow the machine to heat up so that all electri-
cal components can reach their operating tem-
perature.
5. Remove the replacement PC board and substitute it
with the original PC board to recreate the original
problem.
• If the original problem does not reappear by substi-
tuting the original board, then the PC board was not
the problem. Continue to look for bad connections
in the control wiring harness, junction blocks, and
terminal strips.
• If the original problem is recreated by the substitu-
tion of the original board, then the PC board was
the problem. Reinstall the replacement PC board
and test the machine.
6. Always indicate that this procedure was followed
when warranty reports are to be submitted.
NOTE:
Following this procedure and writing on the
warranty report, “INSTALLED AND SWITCHED PC
BOARDS TO VERIFY PROBLEM,” will help avoid
denial of legitimate PC board warranty claims.
PC BOARD TROUBLESHOOTING PROCEDURES
ATTENTION
Static-Sensitive
Devices
Handle only at
Static-Safe
Workstations
Reusable
Container
Do Not Destroy
WARNING
Содержание DC-600 series
Страница 52: ...NOTES DC 600...
Страница 53: ...NOTES DC 600...