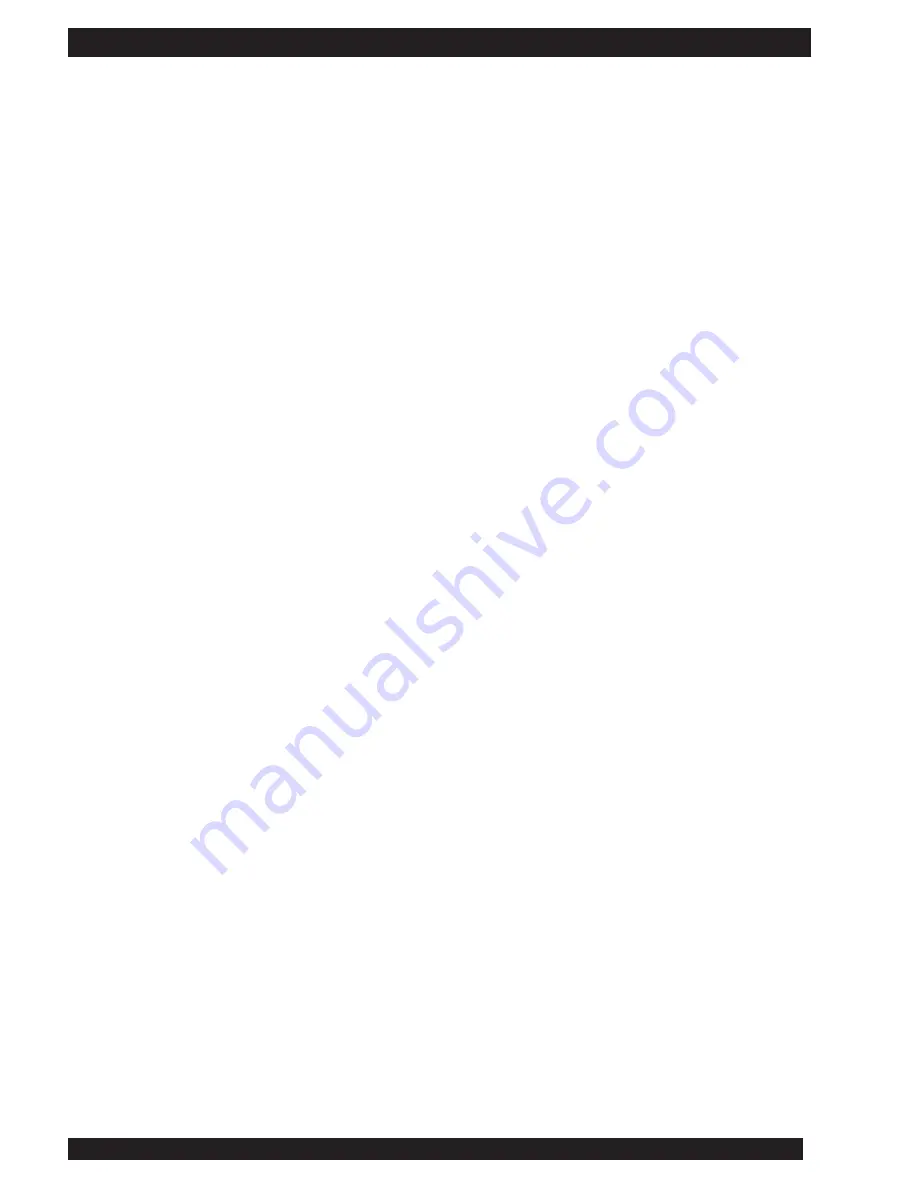
Page 4
CV320-I
IMA 574B
All welders should follow safe practices that minimize their
exposure to electric and magnetic fields (EMF).
For welders wearing implanted pacemakers, safe welding
practices are particularly important and additional procedures
should be followed by those who have decided to continue to
weld. (Hopefully in keeping with a doctor’s advice).
The following procedures will not eliminate exposure to EMF or
the possibility of arc welding having an effect on a pacemaker,
however if followed, they will significantly reduce exposure to
electric and magnetic fields. Electric and magnetic fields are
created any time electric current flows through a conductor,
however it is not clear whether such exposure affects ones health.
Some researchers have reported that exposure to EMF may
cause leukemia or other illnesses. These claims originally arose in
relation to high voltage electric power lines and are very much in
dispute in the medical and scientific arena, however the best
advice is to minimise your exposure to EMF to protect your health
should doctors eventually decide there is a risk.
There are four fundamental fact about EMF:
•
With direct current (DC), the field strength is relatively
constant and does not change.
•
With alternating current (AC), the field strength constantly
changes.
•
The greater the current flow, i.e. the higher the amps, the
stronger the field created by the current
•
The closer the conductor or electrical device is to the body,
the greater the exposure to the field.
Minimising Exposure
All welders should use the following procedures to minimise EMF
exposure.
•
Route electrode or gun and work cables together. Secure
them with tape if possible.
•
Never coil the electrode lead around your body.
•
Do not place your body between the electrode and work
cables. If your electrode cable is on your right side the work
cable should also be on your right side.
•
Connect the work cable to the work piece as close as possible
to the area being welded. (This is also a good practice to
eliminate a common problem on welding - a poor work
connection).
•
Do not work next to the welding power source.
Welders with Pacemakers
There is no question that the fields in arc welding can interfere
with a pacemakers function. Generally the interference does not
permanently damage the pacemaker. Once the wearer leaves the
arc welding environment or stops welding, the pacemaker returns
to normal functioning. The welding arc has little or no effect on the
operation of some pacemakers, especially designs that are bi-
polar or designed to filter out such interference.
For a welder or anyone working around electrical equipment the
selection of a pacemaker is very important. Get a doctor’s advice
about which pacemaker is the least sensitive to interference from
welding while still being medically suitable.
In addition to the normal safety precautions, the following
additional procedures should be adopted by welders with
pacemakers.
•
Use gas welding when the application is suitable.
•
Use the lowest current setting appropriate for the application.
Do not exceed 400 amps. Low current (75-200 amps) direct
current (DC) welding should be used if arc welding is
necessary. Do not TIG weld with high frequency.
•
Do not use repeated, short welds. Wait about ten seconds
between stopping one weld and starting the next. When
having difficulty starting an electrode, do not re-strike the rod
repeatedly.
•
If you feel light headed, dizzy or faint, immediately stop
welding. Lay the electrode holder down so that it does not
contact the work and move away from any welding being
performed. Arrange your work in advance so that, if you
become dizzy and drop the electrode holder, the electrode
holder will not fall on your body or strike the work.
•
Do not work on a ladder or other elevated position or in a
cramped, confined place.
•
Do not work alone. Work only in the presence of an individual
who understands these precautions and the possible effect
welding may have on your pacemaker.
•
Do not work near spot welding equipment.
•
If you have a pacemaker and wish to continue arc welding,
discuss this an any other questions you may have with your
physician and follow his or her advice. The doctor may wish to
contact the pacemaker manufacturer for a recommendation.
As mentioned before, the design of the pacemaker
significantly affects the degree to which it is subject to
interference from a welding circuit. Do not rely on the fact that
you know another welder with a pacemaker who has welded
for years without experiencing a problem. That welder and his
or her pacemaker may be quite different from you and your
pacemaker.
WELDING, EMF AND PACEMAKERS