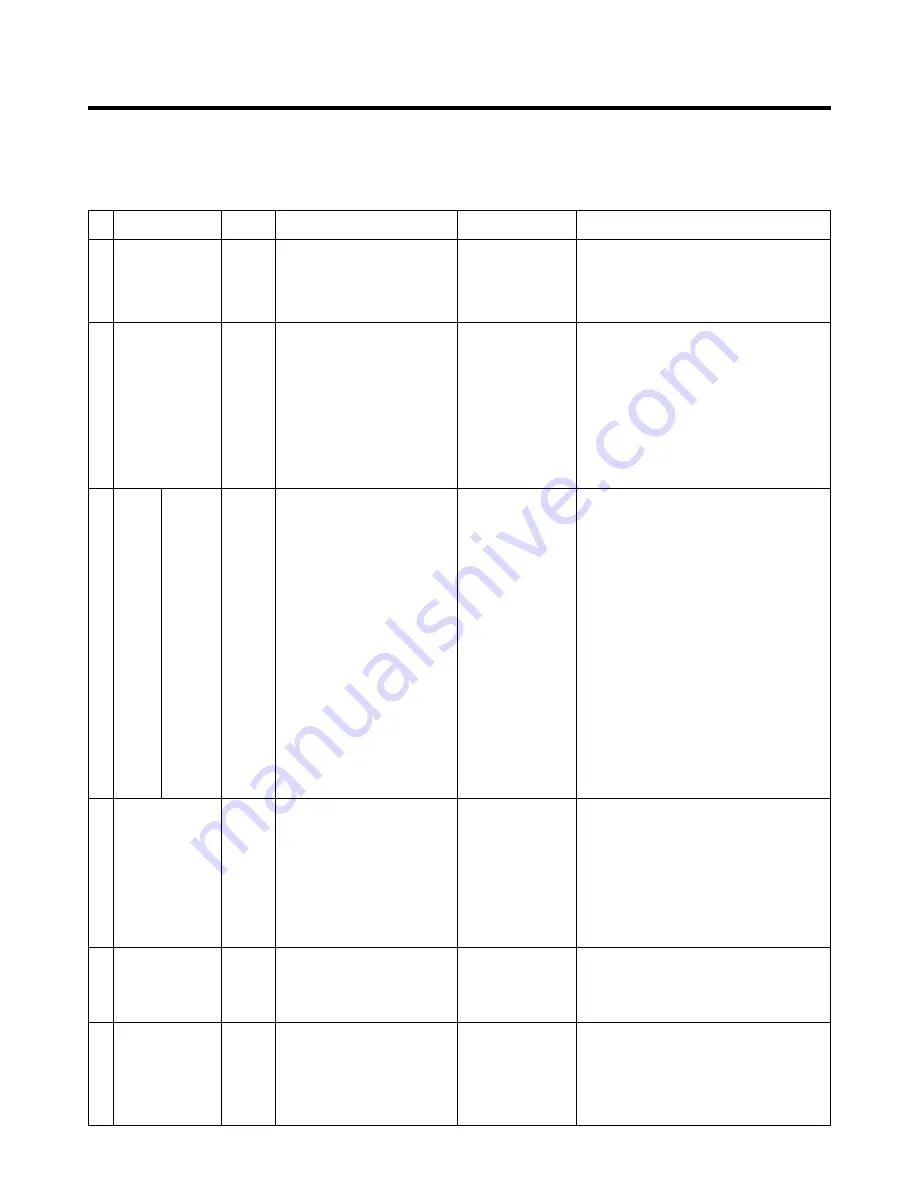
Chapter 8. Major repair method for freezing cycle
8-1. Major repair work standard for refrigerator using R134a refrigerant
Major repair method for freezing cycle
- 35 -
1
2
3
4
5
6
Opening time
for pipe and
piping parts
Welding work
Refrig
erator
cycle
Refrigerator
cycle
Refrigerant
measurement
(BOMBE)
Exchange drier
Leakage test
Min
Nitrogen
supply
pressure
Min
Torr
EA
EA
EA
EA
EA
Vacuum
time
Vacuum
degree
Vacuum
part
Vacuum
piping
Pipe
coupler
Socket
Plug
Pipe part: Within 1 hour
Compressor: Within 10 minutes
Drier: Within 20 minutes
Do the welding while supplying
the nitrogen.
(Nitrogen pressure: .1-0.2kg/cm
2
)
40 minutes or more
0.03 Torr or below (reference)
Simultaneous vacuum for high
and low pressure
Use manifold for R134a
Model name: 40134A
Manufacturer: US Robin Air
For R134a
Model name: PCV630-2SV 1EA
Model name: PCV400-2PV 1EA
Manufacturer: Japanese Nito
For R134a
Model name: 2SV
For R134a
Model name: 2PV
Use the one for R134a and the
measurement tolerance is ±5g.
Note) If it is -5g for winter and +5g
for summer, it is well
managed. (manufactured
by LG)
- For R134a
- When repairing the refrigerator
cycle piping, always exchange
the drier.
- Never do a soap water test. The
soap water can leak into the
piping from the vibration.
- Leakage detector model: 16170,
16500. Manufacturer: US Robin Air
Prevent moisture
penetration
Prevent oxidization
scale generation
within the pipe from
high temperature
heat during welding
Remove moisture
Prevent mixed
penetration of
mineral oil and
ether oil
Prevent mixed
penetration of R12
refrigerant
Prevent mixed
penetration of R12
refrigerant
Prohibit mixed use
of R12 refrigerant
Prohibit mixed use
of R12 refrigerant
Remove moisture
existing within the
piping
Detect refrigerant
leakage part
(for reference)
Specially manage to half or lower of the prior
standard during rain or rainy season.
(Especially the water penetration within the
piping can be crucial)
- Refer to the Caution section of the major repair
part for work methods of each part.
- Because the R134a refrigerant has a smaller
molecular size than that of R12 refrigerant,
special care is needed when welding the pipe
because leakage can occur more easily.
- Do not apply pressure to the parts of the piping
before and after the welding. It can cause the
pipe to crack and cause leakage.
Manufacturer of 113l/min model WVP-Z: US
Asco
Note) The model should have a counter-current
blocker.
The vacuum effect can be increased during a
vacuum with both high and low pressure while
operating the compressor.
For the refrigerant piping (rubber type), using
the existing piping for R12 for the new R134a
refrigerant can cause the rubber to be melted
(can cause leakage).
- When measuring the refrigerant, do not measure
it in a very hot or cold location (ambient
temperature of 25°C is best) When manufacturing
an additional bombe, use copper for the material.
- End socket: 2SV plug: Use the proper one for
2PV R134a
Note) When welding the connection part of both ends,
make sure the internal O ring (rubber) does not burn.
- For the refrigerant leaking part, check if oil is
leaked and if not found, use the electric leakage
detector.
No.
Work item
Unit
Work standard
Objective
Remarks
Содержание GR-K192UF
Страница 8: ...Chapter 4 Circuit diagram Circuit diagram 8 ...
Страница 29: ...MICOM function and circuit description 29 ...
Страница 54: ...Assembly diagram and service parts list 54 249G 249D 248A 249B 212D 102A 102A 248D 147C 147A 270A 212G ...
Страница 55: ...P No MFL31842103 FEB 2008 Printed in Korea ...