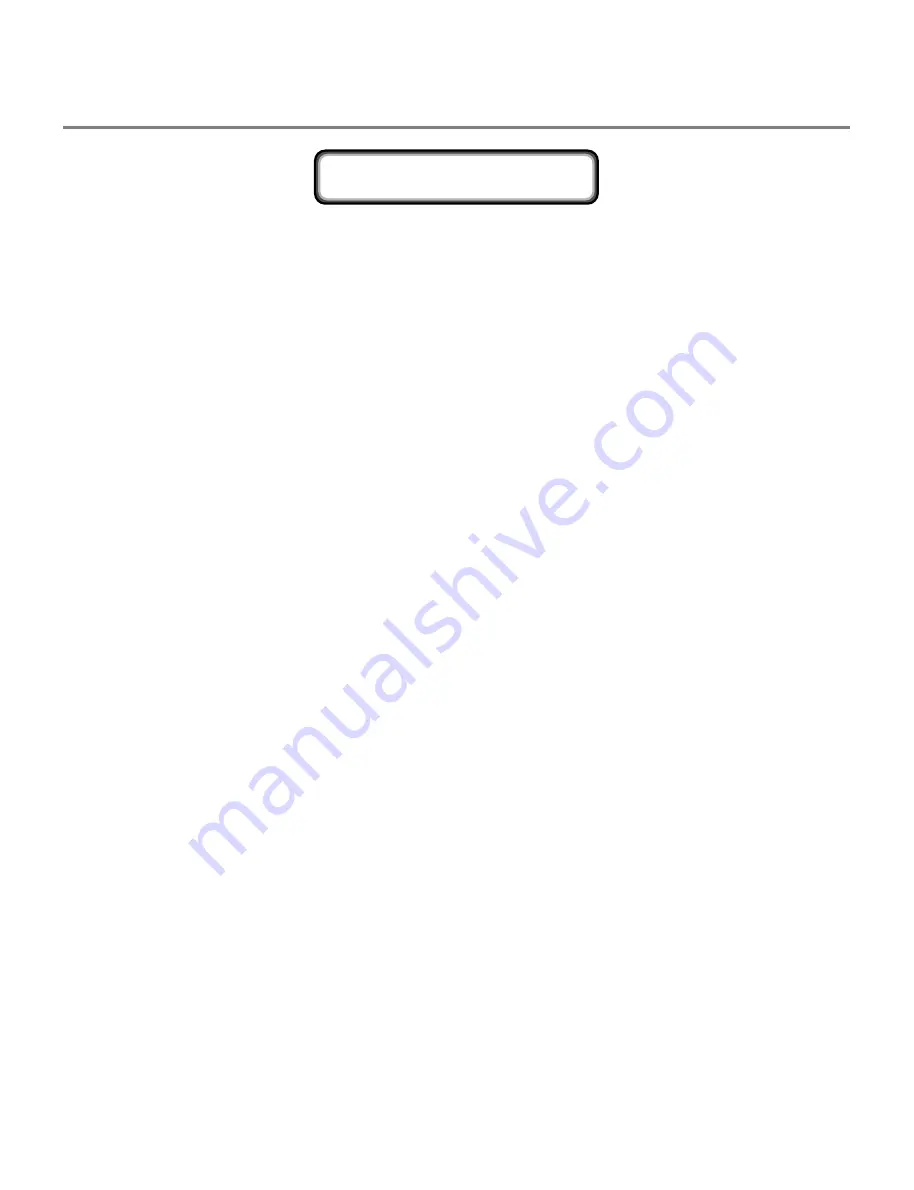
3
1. IMPORTANT SAFETY INSTRUCTIONS..................................................................................................................4
2. SPECIFICATIONS .............................................................................................................................................10
3. FEATURES AND BENEFITS ............................................................................................................................... 12
4. INITIAL STEPS FOR INSTALLING YOUR DRYER ...................................................................................................13
5. INSTALLATION INSTRUCTIONS ........................................................................................................................18
6. ELECTRICAL REQUIREMENTS FOR ELECTRIC DRYERS .........................................................................................20
7. ELECTRICAL REQUIREMENTS FOR GAS DRYERS ................................................................................................25
8. GAS REQUIREMENTS AND INSTRUCTIONS ......................................................................................................26
9. EXHAUST REQUIREMENTS AND MAINTENANCE..............................................................................................27
10. DRYER CYCLE PROCESS ................................................................................................................................ 29
11. COMPONENT TESTING INFORMATION .........................................................................................................30
12. MOTOR DIAGRAM AND SCHEMATIC ............................................................................................................33
13. CONTROL LAYOUT .......................................................................................................................................34
14. WIRING DIAGRAM .......................................................................................................................................35
15. DIAGNOSTIC TEST.........................................................................................................................................36
15-1. TEST 1 120VAC ELECTRICAL SUPPLY ...................................................................................................37
15-2. TEST 2 THERMISTOR TEST ...................................................................................................................40
15-3. TEST 3 MOTOR TEST ..........................................................................................................................41
15-4. TEST 4 MOISTURE SENSOR ...............................................................................................................42
15-5. TEST 5 DOOR SWITCH TEST ..............................................................................................................43
15-6. TEST 6 HEATER SWITCH TEST - ELECTRIC MODEL ................................................................................44
15-7. TEST 7 GAS VALVE TEST - GAS MODEL ..............................................................................................45
15-8. TEST 8 SEMI CONDUCTOR .................................................................................................................46
16. CHANGE GAS SETTING (NATURAL GAS, PROPANE GAS) ............................................................................47
17. DISASSEMBLY INSTRUCTIONS .......................................................................................................................49
18. EXPLODED VIEW ...........................................................................................................................................56
18-1. CONTROL PANEL & PLATE ASSEMBLY...................................................................................................56
18-2. CABINET & DOOR ASSEMBLY...............................................................................................................57
18-3-1. DRUM & MOTOR ASSEMBLY: ELECTRIC MODEL .................................................................................58
18-3-2. DRUM & MOTOR ASSEMBLY: GAS MODEL ........................................................................................59
19. REPLACEMENT PARTS LIST..............................................................................................................................60
20. MAINTENANCE.............................................................................................................................................64
21. TROUBLESHOOTING GUIDE...........................................................................................................................65
CONTENTS