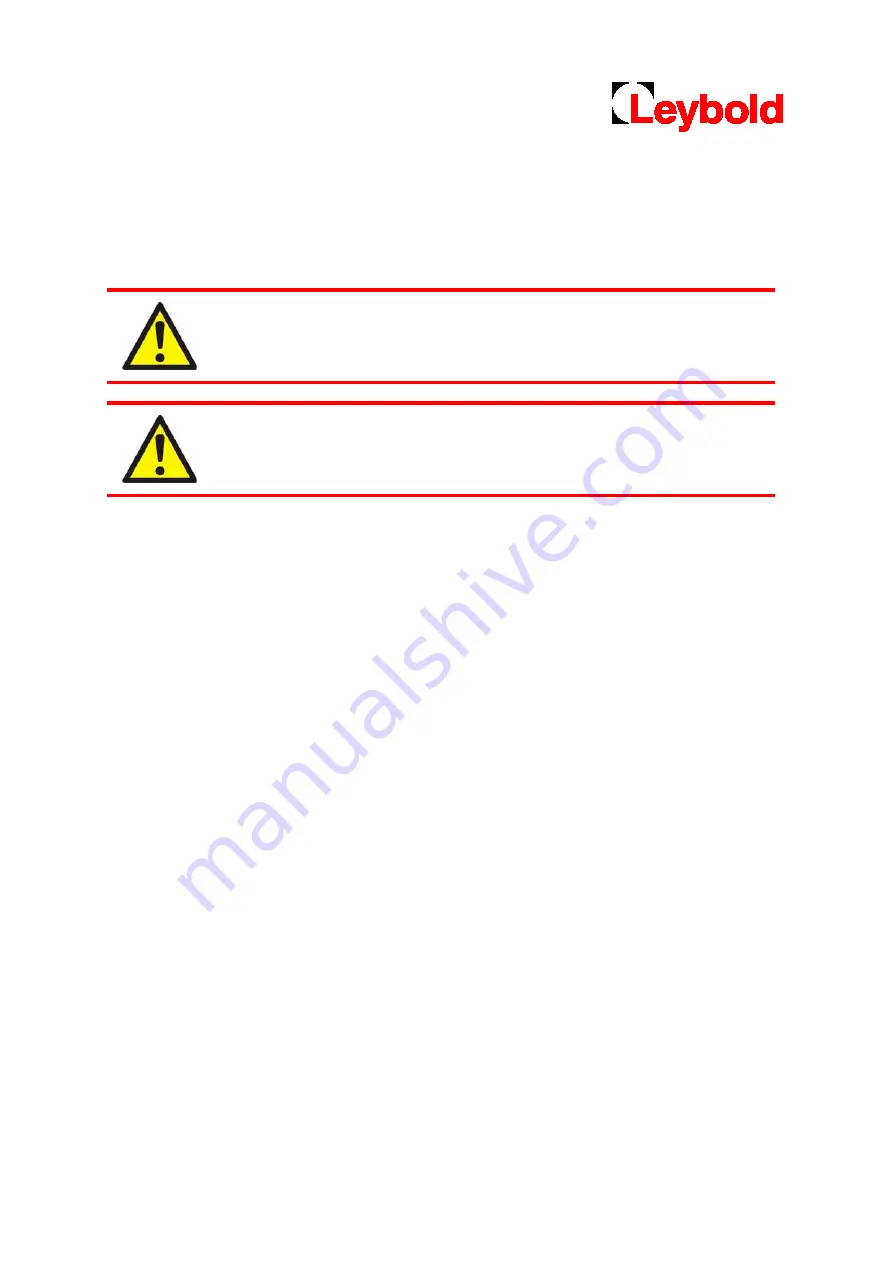
Maintenance
28
300692481_002_C0 – 08/2018 – © Leybold
5
Maintenance
5.1
Safety information
WARNING
Obey the safety instructions given below and take note of appropriate precautions.
Failure to follow the instructions can cause injury to people and damage to
equipment.
WARNING
Condensation from cooling surface in some environments, or lubricating oil
spillages can cause a slip hazards. Failure to follow instructions could lead to
injury.
A suitably trained and supervised technician must maintain the pump. Obey your local and
national safety requirements.
Ensure that the maintenance technician is familiar with the safety procedures which relate to the
gases pumped/compressed by the system in which the pump is installed.
Make sure to verify that pump internal pressure is completely equalized to atmospheric pressure.
Allow the pump to cool to a safe temperature before starting maintenance work.
Isolate the RUVAC WA 40000 pump from the electrical supply/drive system so that it cannot be
operated accidentally.
Recheck the pump rotation direction (see
) if the motor electrical supply or drive and
transmission system has been disconnected and then reconnected.
Take care to protect inlet/outlet port sealing faces from damage.
Do not reuse seals/gaskets if they are damaged.
Check the leak tightness of the system connections after maintenance work is completed if the
pump inlet or outlet joints are connected or disconnected. The leak tightness of the system
connections must be in accordance with the requirements of the applications.
The RUVAC WA 40000 pump will be contaminated with the process gases that have been
pumped. Take adequate precautions to protect people from the effects of dangerous substances
if contamination has occurred.
Содержание RUVAC WA 40000
Страница 2: ...This page has been intentionally left blank...
Страница 4: ...This page has been intentionally left blank...
Страница 8: ...This page has been intentionally left blank...
Страница 41: ...300692481_002_C0 08 2018 Leybold 41 Declaration of conformity...
Страница 42: ...42 300692481_002_C0 08 2018 Leybold Declaration of contamination...
Страница 43: ...300692481_002_C0 08 2018 Leybold 43...
Страница 44: ...44 300692481_002_C0 08 2018 Leybold...